Особливості пристрою
Основні розміри клапанів, що направляють втулок та сідел клапанів дано на рис. 2-45.
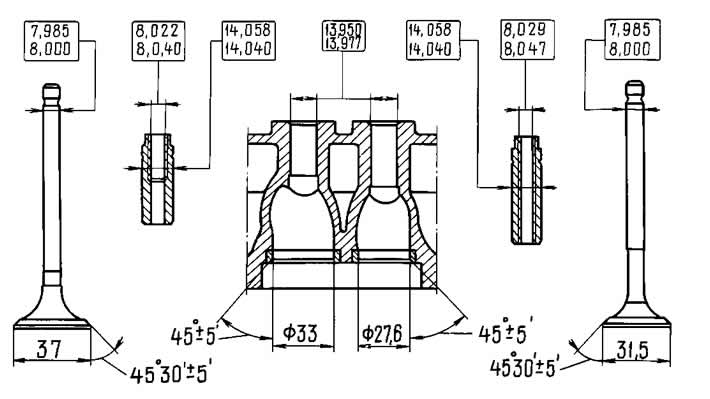
Мал. 2-45. Основні розміри клапанів, що направляють втулок та сідел клапанів.
Головка циліндрів відлита з алюмінієвого сплаву, має запресовані чавунні сідла та напрямні втулки клапанів. Верхня частина втулок ущільнюється гумометалевими масловідбивними ковпачками.
У запасні частини напрямні втулки поставляються із збільшеним на 0,2 мм зовнішнім діаметром.
На головці циліндрів закріплений корпус підшипників, у якому знаходиться розподільний вал.
Механізм приводу клапанів
Клапани 2 (рис. 2-46) наводяться в дію кулачками розподільних валів через важелі 3. Одним кінцем важіль тисне на клапан, а іншим спирається на сферичну головку гідравлічної опори 6. Гідроопори автоматично усувають зазор у клапанному механізмі і тому при технічному обслуговуванні автомобіля та регулювати зазор у клапанному механізмі не потрібно.

Мал. 2-46. Механізм приводу клапанів:
1 – головка циліндрів;
2 – клапан;
3 – важіль клапана;
4 - рампа олійна;
5 – розподільчий вал;
6 - гідравлічна опора штовхача;
7 – гайка;
8 - втулка гідроопори;
9 – проставка.
Гідронатягувач ланцюга
Олія із системи мастила по трубці 3 (див. рис. 2-12) надходить у порожнину «Е» (рис. 2-47) натягувача, далі через отвір «Д» і клапанний вузол 2 потрапляє в робочу порожнину «В» і тисне на плунжер 5. У корпусі 1 натягувача є отвір діаметром 1 мм для стравлювання повітря з порожнини "Е".
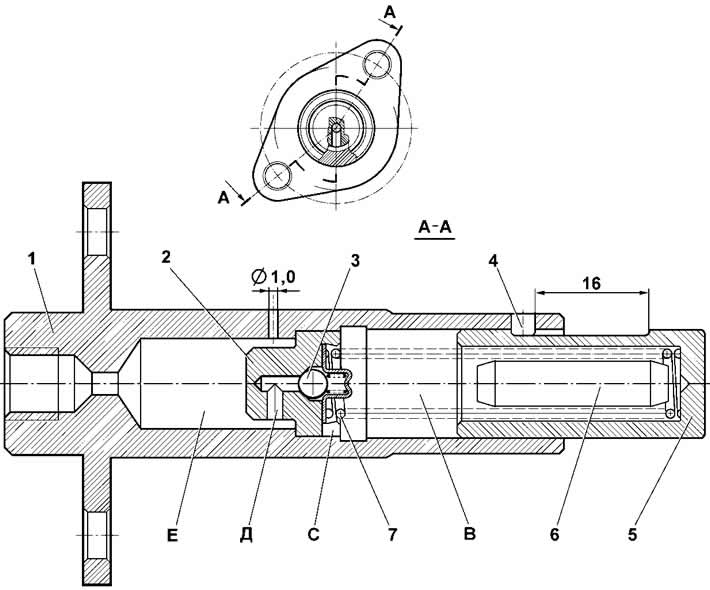
Мал. 2-47. Гідравлічний натягувач ланцюга:
1 - корпус натягувача;
2 – клапанний вузол;
3 - кулька зворотного клапана;
4 – обмежувальний штифт;
5 - плунжер натягувача;
6 - обмежувач обсягу;
7 – пружина плунжера;
В – робоча порожнина;
С - паз настановний;
Д – отвір;
Е – резервна порожнина.
Діаметральний зазор між корпусом 1 і плунжером 2 повинен бути 0,018-0,024 мм і вимірюється як різницю максимального діаметра вимірювання плунжера 2 і мінімального вимірюваного діаметра корпусу 1.
При ремонті корпус натягувача та плунжер складають пару, в якій заміна однієї деталі іншою після підбору зазору не допускається. Плунжер 2 повинен без заїдання переміщатися в корпусі 1 величину ходу рівну 16 мм.
При встановленні на двигун натягувач повинен бути вільний від олії, штифт 4 не повинен виступати з корпусу.
Зняття та встановлення головки циліндрів на автомобілі
Головку циліндрів знімають із двигуна на автомобілі, якщо для усунення несправності не потрібно розбирати весь двигун. Наприклад, якщо необхідно видалити нагар з поверхні камер згоряння та клапанів або замінити клапани або напрямні втулки клапанів.
Знімайте головку циліндрів у такому порядку:
- встановіть автомобіль на підйомник та скиньте тиск у системі подачі палива. Для цього від'єднайте колодку джгута проводів електробензонасоса від джгута проводів системи запалювання, запустіть двигун, дайте йому попрацювати до зупинки;
- від'єднайте провід від клеми «мінус» акумуляторної батареї;
- підніміть автомобіль і злийте охолоджувальну рідину з радіатора та блоку циліндрів, дотримуючись рекомендацій, викладених у підрозділі «Зняття та встановлення двигуна»;
- від'єднайте приймальну трубу глушників від випускного колектора, зніміть кронштейн труби, що підводить, насоса охолоджуючої рідини;
- опустіть автомобіль, від'єднайте шланг (див. мал. 2-4) підведення палива від паливної трубки. Заглушіть отвори шланга та трубки, щоб у них не потрапив бруд;
- від'єднайте трос 2 (див. рис. 2-5) приводу акселератора від дросельного патрубка і кронштейна 4 на ресивері;
- зніміть шланги витяжної вентиляції картера, від'єднавши їх від патрубків на кришці головки циліндрів, від шланга впускної труби та від дросельного патрубка;
- послабте стяжні хомути та від'єднайте від дросельного патрубка шланг 1 (див. рис. 2-6) впускної труби, шланг продувки адсорбера, шланги підведення та відведення охолоджуючої рідини;
- від'єднайте від ресивера шланг відбору розрідження до вакуумного підсилювача гальм;
- від'єднайте дроти від свічок запалювання, від датчиків контрольної лампи тиску олії та покажчика температури охолоджуючої рідини, від дросельного патрубка; від'єднайте дроти від джгута проводів форсунок;
- від'єднайте шланги від патрубка, що відводить, сорочки охолодження двигуна;
- зніміть кришку головки циліндрів із прокладкою, кронштейнами екрана двигуна та троса акселератора;
- поверніть колінчастий вал до суміщення мітки на зірочці розподільного валу з міткою на корпусі підшипників (див. рис. 2-26);
- відкрутіть болт кріплення зірочки розподільного валу, відкрутіть штуцер, гайки і зніміть гідронатягувач ланцюга, зніміть зірочку розподільчого валу;
- відкрутіть болти кріплення головки циліндрів до блоку та зніміть головку циліндрів з прокладкою.
Встановлюйте головку циліндрів у порядку, зворотному зняттю, дотримуючись рекомендацій, викладених у підрозділі «Складання двигуна». Прокладку між головкою та блоком циліндрів повторно застосовувати не допускається, тому замініть її на нову.
Після встановлення головки циліндрів відрегулюйте привід акселератора.
Перевірте роботу системи керування двигуном.
Розбирання та збирання головки циліндрів
Розбирання. Якщо потрібна заміна тільки однієї деталі, то можна не розбирати повністю головку циліндрів і зняти тільки те, що необхідно для заміни.
Встановіть головку циліндрів на підставку, відверніть гайки та зніміть впускну трубу, випускний колектор та екран впускної труби. Зніміть патрубок сорочки охолодження і патрубок відведення рідини до обігрівача. Виверніть свічки запалювання та датчик температури охолоджуючої рідини.
Відкрутіть гайки кріплення та зніміть корпус підшипників у зборі з розподільчим валом. Відкрутіть гайки кріплення упорного фланця до корпусу підшипників. Зніміть фланець і вийміть розподільний вал із корпусу підшипників.
Зніміть важелі 3 клапанів (див. мал. 2-46).
Викрутіть гідроопори 6 (див. мал. 2-46а) і зніміть масляну рампу 4.
На двигунах, укомплектованих гідроопорами ф. INA, витягніть гідроопори 6 (див. рис. 2-46б), виверніть втулки 8 гідроопор, зніміть масляну рампу 4 з проставками 8 у зборі.
Встановіть головку циліндрів на пристрій 67.7823-9567, стисніть пружини клапанів і звільніть сухарі.
Зніміть пружини клапанів із тарілками та опорними шайбами. Поверніть головку циліндрів і вийміть клапани. Зніміть масловідбивні ковпачки з напрямних втулок.
Складання. Складання головки циліндрів проводите в порядку, зворотному розбиранні. Клапани та масловідбивні ковпачки перед збиранням змастіть моторним маслом.
Перед встановленням корпусу підшипників розподільчого валу перевірте чи на місці установочні втулки (див. мал. 2-25). Гайки кріплення корпусу підшипників затягуйте у порядку, вказаному на рис. 2-27. При цьому зверніть увагу на те, щоб втулки без перекосу увійшли в гнізда корпусу підшипників.
Перед встановленням гідроопор із запасних частин помістіть кожну гідроопору в ємність з моторним маслом до повного її занурення в масло і зробіть кілька натискань зусиллям рук до видалення вільного ходу плунжера.
Перевірка технічного стану та ремонту
Головка циліндрів. Ретельно вимийте головку циліндрів та очистіть масляні канали. Видаліть нагар із камер згоряння та з поверхні випускних каналів металевою щіткою.
Огляньте голівку циліндрів. Тріщини у будь-яких місцях голівки циліндрів не допускаються. При підозрі на потрапляння рідини, що охолоджує, в масло перевірте герметичність головки циліндрів.
Для перевірки герметичності закрийте отвори охолоджувальної сорочки головки циліндрів заглушками, що входять до комплекту пристосування А.60334 (рис. 2-48). Подайте всередину головки стиснене повітря під тиском 0,15-0,2 МПа (1,5-2 кгс/см). Протягом 1-1,5 хв не повинно спостерігатись виходу бульбашок повітря з головки.
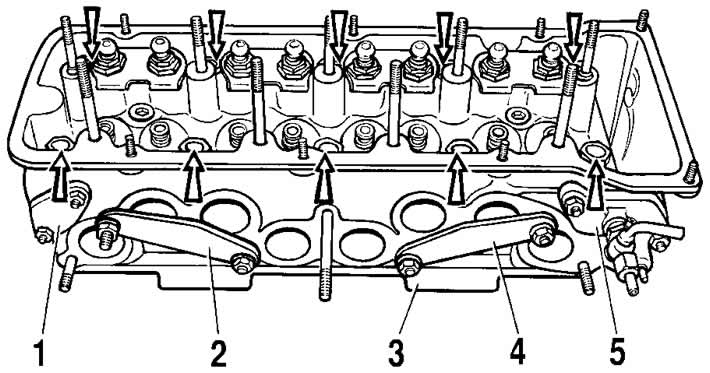
Мал. 2-48. Перевірка герметичності головки циліндрів на пристрої А.60334:
1, 2, 4 – заглушки;
3 – плита пристосування;
5 - фланець зі штуцером підведення повітря.
Сідла клапанів. Форма фасок сідел клапанів показана на рис. 2-49 та 2-50. На робочих фасках сідел (зона контакту з клапанами) не повинно бути точкових раковин, корозії та пошкоджень. Невеликі пошкодження можна усунути шліфуванням сідел, знімаючи якнайменше металу. Шліфувати можна як вручну, так і за допомогою шліфувальної машинки.
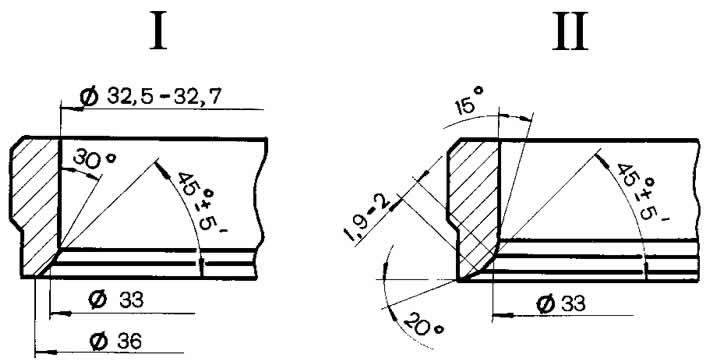
Мал. 2-49. Профіль сідла впускного клапана:
I – нове сідло;
II – сідло після ремонту.
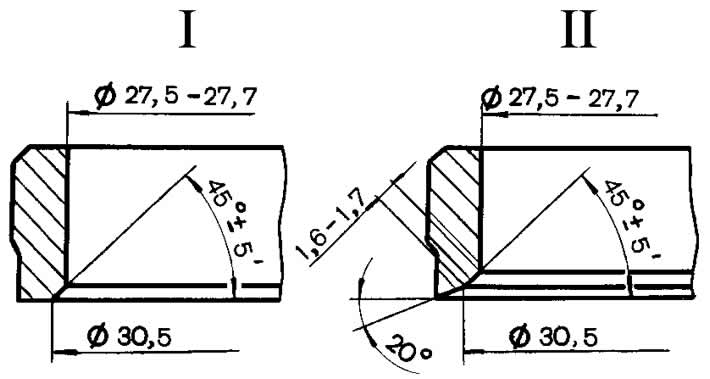
Мал. 2-50. Профіль сідла випускного клапана:
I – нове сідло;
II - сідло після ремонту
Для шліфування сідел встановіть головку циліндрів на підставку, вставте в направляючу втулку клапана стрижень А.94059 і очистіть фаски сідел від нагару зенкерами А.94031 і А.94092 для сідел випускних клапанів і зенкерами А.94003 і А9. Зенкера надягають на шпиндель А.94058 і центруються напрямним стрижнем А.94059. Ці стрижні існують двох різних діаметрів: А.94059/1 - для направляючих втулок впускних клапанів та А.94059/2 для направляючих втулок випускних клапанів.
Надягніть на напрямний стрижень А.94059 пружину А.94069/5, встановіть на шпиндель А.94069 конічний коло А.94078 для сідел випускних клапанів або коло А.94100 для сідел впускних клапанів, закріпіть шпиндель у шліфувальній машинці 2-51).
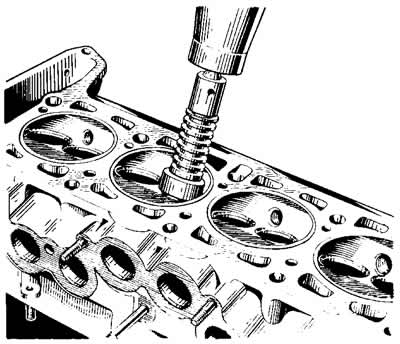
Мал. 2-51. Шліфування робочої фаски сідла клапана.
У момент зіткнення кола з сідлом машинка повинна бути вимкнена, інакше виникне вібрація і фаска буде неправильною. Рекомендується частіше проводити редагування кола алмазом.
Для сідел випускних клапанів ширину робочої фаски доведіть до величин, вказаних на рис. 2-51, зенкером А.94031 (кут 20°), і зенкером А.94092, яким усувається наклеп на внутрішньому діаметрі. Зенкери надягають на шпиндель А.94058 і, як і при шліфуванні, центруються стрижнем А.94059.
У сідел впускних клапанів ширину робочої фаски доведіть до величин, вказаних на рис. 2-52 спочатку обробивши внутрішню фаску зенкером А.94003 (рис. 2-52) до отримання діаметра 33 мм, а потім фаску 20°зенкером А.94101 до отримання робочої фаски шириною 1,9-2 мм.

Мал. 2-52. Звуження робочої фаски сідла клапана зенкером, встановленим на шпинделі А.94058.
Клапани. Видаліть нагар із клапанів. Перевірте, чи не деформовано стрижень і чи немає тріщин на тарілці. Пошкоджений клапан замініть.
Перевірте стан робочої фаски клапана. При дрібних пошкодженнях можна прошліфувати, витримуючи кут фаски 45°30'±5'. При цьому відстані від нижньої площини тарілки клапана до базових діаметрів (36 та 30,5 мм) мають бути в межах, вказаних на рис. 2-53.
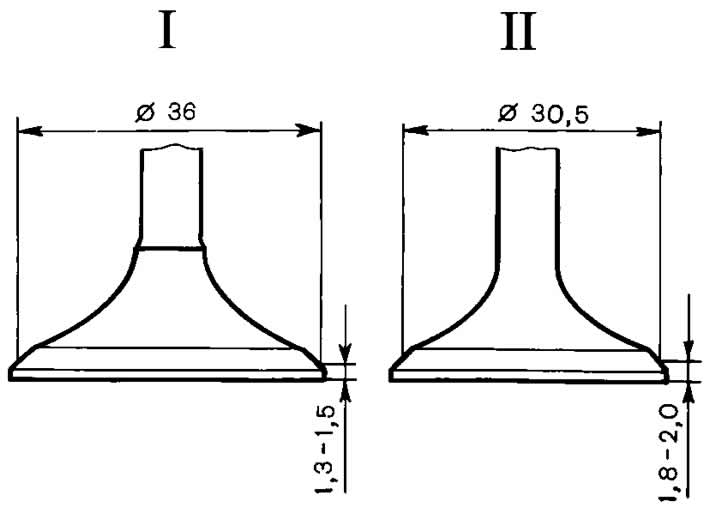
Мал. 2-53. Граничні розміри при шліфуванні фасок клапанів:
I - впускний клапан;
II – випускного клапана.
Напрямні втулки клапанів. Перевірте зазор між напрямними втулками та стрижнем клапана, вимірявши діаметр стрижня клапана та отвір напрямної втулки.
Розрахунковий зазор для нових втулок: 0,022-0,055 мм для впускних клапанів та 0,029-0,062 мм для випускних клапанів; гранично допустимий граничний зазор (при зносі) - 0,3 мм за умови відсутності підвищеного шуму газорозподільного механізму.
Якщо збільшений зазор між напрямною втулкою та клапаном не може бути усунений заміною клапана, замініть втулки клапанів, використовуючи для випресування та запресування оправкою A.60153/R (рис. 2-54).
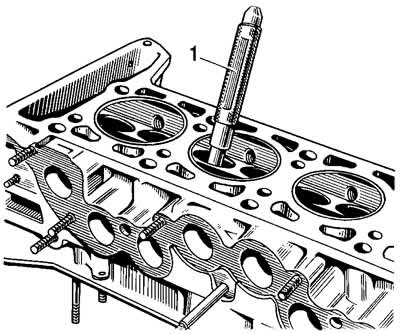
Мал. 2-54. Випресування напрямних втулок:
1 - виправлення A.60153/R.
Запресовуйте напрямні втулки з надітим стопорним кільцем до упору в тіло головки циліндрів.
Після запресування розгорніть отвори в напрямних втулках розгортками А.90310/1 (для втулок впускних клапанів) та А.90310/2 (для втулок випускних клапанів).
Масловідбивні ковпачки напрямних втулок під час ремонту двигуна завжди замінюйте новими.
Пошкоджені олійно-відбивні ковпачки замінюйте на знятій головці циліндрів. Для запресування ковпачків користуйтесь оправкою 41.7853.4016.
Пружини. Переконайтеся, що на пружинах немає тріщин і не зменшилася їхня пружність, для чого перевірте їхню деформацію під навантаженням (рис. 2-55).
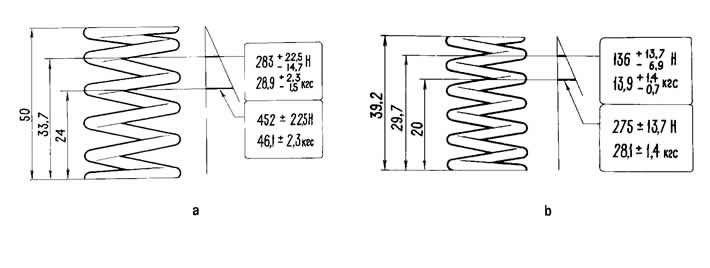
Мал. 2-55. Основні дані для перевірки зовнішньої (а) та внутрішньої (b) пружини клапана.
Болти кріплення головки циліндрів. При багаторазовому використанні болтів вони витягуються. Тому перевірте, чи не перевищує довжина стрижня болта (без урахування довжини головки) 117 мм і, якщо вона більша, то замініть болт новим.
Гідроопори. Перевірте стан гідроопор. Плунжер гідроопори, встановленої в голівку циліндрів, повинен переміщатися при різкому натисканні ними рукою. У разі вільного переміщення плунжера замініть гідроопору.
Важелі клапанів. Перевірте стан робочих поверхонь важеля, що сполучаються зі стрижнем клапана, з кулачком розподільчого валу та зі сферичним кінцем плунжера гідроопори. Якщо на цих поверхнях з'явилися задираки або ризики, замініть важіль новим.