По программе, записанной на магнитном носителе (возможна работа стенда непосредственно с CD-диском, поставляемым вместе с платой сопряжения для IBM PC настольных компьютеров), управляющая ЭВМ выполняет следующие действия: измерение пассивного и активного сопротивления обмотки каждой форсунки; измерение тока в цепи при напряжении 10-14 В; проверка герметичности клапанов электромагнитных форсунок при давлении 1-5 Па; измерение контрольного расхода газа (воздуха) при частоте 1-100 Гц, а также испытание электромагнитных форсунок на отказ при частоте 1-100 Гц. Перечисленные диагностические тесты могут выполняться в комплексе или выборочно как для одной форсунки, так и всего комплекта (четырех) форсунок одновременно.
Диагностирование бензинового клапана. Клапан устанавливают на стенд с помощью специального зажима и подключают к проверочной магистрали. Затем запускают программу его диагностирования по программе ЭБУ совместно с исполнительными устройствами системы питания (электробензонасос с приводом от электрического двигателя, запорная арматура, источник постоянного тока и т.д.). Программа обеспечивает измерение пассивного и индуктивного сопротивлений обмотки бензинового клапана, измерение тока в цепи при напряжении 10-14 В с замером температуры обмотки, проверку герметичности клапана при давлении 0,4-0,5 МПа, проверку расхода топлива через бензиновый клапан (тестирование проходного сечения клапана), испытание клапана в рабочем режиме на четкость срабатывания в течение 1000 циклов «Вкл/Выкл». Перечисленные диагностические тесты могут быть выполнены в комплексе или выборочно.
Диагностирование расходомера воздуха. Расходомер воздуха устанавливают в разрыв специального патрубка стенда и подключают к диагностическому разъему. Затем запускают программу диагностирования и осуществляют тестирование датчика. Программа работает по следующему алгоритму: запуск нагнетающей турбины; замер потребляемого датчиком тока от источника 5 В; замер потребляемого тока от источника 12 В; изменение частоты вращения нагнетающей турбины в пределах, соответствующих расходу воздуха двигателем на режимах холостого хода и максимальной частоте вращения КВ (3000 мин-1 для автомобилей «Лада-110»). В дальнейшем проводят замер показаний датчика и сравнивают их с показаниями датчика, принятого за эталон. Измерения в процессе контроля можно видеть на приборах, дублирующих работу программы - осциллографе, микроамперметре, вольтметре.
Схема подключения нитевого датчика ДМРВ приведена на рис. 6.7. Обрыв в проводе 57(К) - отключить БУ и ДМРВ от жгута проводов. Следует убедиться в отсутствии такого обрыва, измерив сопротивление между контактами «5» в розетке Р75 и контактом «1» в розетке диагностического разъема.
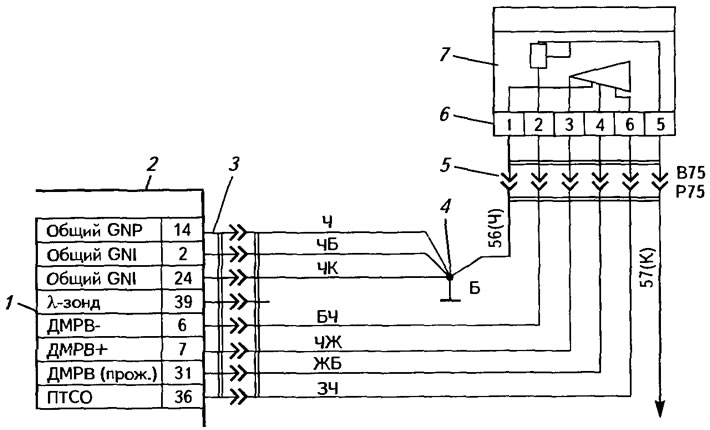
Рис. 6.7. Цепь нитевого датчика ДМРВ: 1 - параметры; 2 - электронный блок управления; 3 - розетка; 4 - «масса»; 5 - розетка; 6 - контакты датчика; 7 - датчик массового расхода воздуха
Цепь пленочного датчика приведена на рис. 6.8. Признак неисправности связан с высоким уровнем сигнала пленочного датчика массового расхода воздуха. Двигатель запущен, напряжение на контактах «3» и «2» ДМРВ выше 4,5 В (см. рис. 6.8), обрыв провода «6» (БЧ) ЭБУ. При отключенных от жгута проводах ЭБУ и ДМРВ следует убедиться в отсутствии обрыва в проводе «6» (БЧ), измерив сопротивление между контактами «3» и «5» в разъеме Р75 датчика.
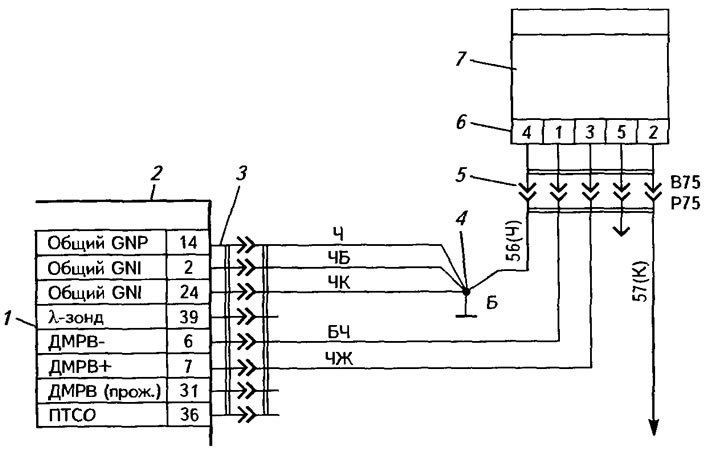
Рис. 6.8. Цепь пленочного датчика ДМРВ. Условные обозначения см. на рис. 6.7
Диагностирование датчика детонации. Датчик детонации устанавливают на специальном виброэлементе стенда, его резьбовая часть вворачивается в специальную втулку. После надежного фиксирования датчика детонации и подключения его вывода к диагностическому разъему стенда запускают тестирующую программу датчика детонации. Выполняются следующие проверки и тесты: замер сопротивления датчика (нормальное значение сопротивления 3300-4500 Ом), включение генератора детонации, замер напряжения на частотах 1-20 Гц.
Диагностирование датчика положения дроссельной заслонки. Датчик устанавливают на дроссельный патрубок. При этом следует соблюдать осторожность, так как датчик снабжен пластмассовым корпусом и может быть поврежден. Затем запускают программу тестирования датчика, которая выполнит следующую последовательность действий: измерение сопротивления потенциометра в начальном положении, т.е. при закрытой дроссельной заслонке; перемещение заслонки в максимально открытое положение; измерение сопротивления потенциометра в конечном (крайнем) положении; изменение угла открытия дроссельной заслонки; считывание показаний сопротивления в течение 5 мин.
Диагностирование датчика температуры охлаждающей жидкости. Датчик устанавливают в специальное гнездо на стенде, где происходит его нагрев и охлаждение в пределах от +40 до -40°С. Контроль параметров датчика выполняют по следующему алгоритму: измерение сопротивления датчика в течение 5 мин. при температуре 20°С; охлаждение датчика до температуры -40°С при одновременном измерении сопротивления датчика; нагрев датчика до температуры +140°С при одновременном измерении сопротивления датчика.
Диагностирование датчика положения КВ. Датчик устанавливают на стенде в специальном суппорте, который настраивают вручную на расстояние 0,3 мм до ближайшего зубца задающего колеса. Затем по программе тестирования датчика измеряют сопротивление его обмотки. Задающему диску сообщают частоту вращения 800-1500 мин-1 и измеряют ток и напряжение в обмотке при прохождении пропущенного зубца на задающем шкиве.
Диагностирование РХХ. Шток РХХ перед установкой необходимо переместить в крайнее открытое положение во избежание повреждения поверхности запорного конуса. Для этого необходимо подключить датчик к диагностическому разъему стенда и, запустив программу диагностирования РХХ, выбрать в меню команду установки датчика в исходное положение. После установки РХХ следует запустить программу комплексного диагностирования РХХ, работающую по следующему алгоритму: измерение сопротивления обмотки А; измерение сопротивления обмотки В; измерение тока в обоих обмотках при перемещении штока регулятора на один шаг в сторону открытия и закрытия; установка штока в исходное положение и отсчет количества шагов до полного закрытия обводного канала; измерение мгновенного значения тока в закрывающей обмотке в момент посадки запорного конуса в седло; установка штока в исходное положение.
Результаты контрольно-диагностических испытаний основных датчиков электронной системы подачи топлива автомобиля ВАЗ-211, полученные на стенде КЕ-1: датчик положения КВ индукционного типа имеет сопротивление обмотки 550-750 Ом и при частоте вращения КВ двигателя 300-400 мин-1 вырабатывает напряжение около 0,3 В. Датчик положения дроссельной заслонки при открытой заслонке имеет сопротивление 5,7 кОм, а при закрытой - 1,7 кОм. Датчик детонации имеет сопротивление внутреннего нагрузочного резистора 3300-4500 Ом и при резонансе вырабатывает напряжение 0,5-1,0 В. ДМРВ потребляет от источника напряжения 5 В ток 1,2 мА, а от источника напряжения 12В - 33,6-40,0 мА. Электрический сигнал датчика изменяется в пределах от 1 В, при отсутствии потока воздуха, до 4 В при максимальном расходе воздуха, т.е. на режиме максимальной нагрузки (3000 мин-1). Регулятор XX между контактами А и В, С и D имеет сопротивление 40-80 Ом. Ход штока регулятора холостого хода равен 30 мм.