Maintenance Methods
There are several basic principles of car maintenance and repair that are constantly mentioned throughout this manual. Following them allows the car owner to rationally and efficiently carry out various repair procedures, as well as effectively carry out maintenance.
Threaded connections
Threaded fasteners refer to nuts, bolts, studs and screws that hold two or more parts together. When handling such elements, some features of this group of parts should be taken into account. Connections almost always include some type of locking device: a spring washer, lock nut, or pin. Sometimes a fastening compound is applied to the threads to secure the connection. All connection fasteners must be pre-cleaned and inspected for compliance with their geometric shape. The threads should not show signs of damage or wear, and the edges of the hexagon wrenches should not be rounded. When assembling, get used to replacing damaged threaded parts with new elements. Locknuts with plastic sleeves can only be used for their intended purpose once. When unscrewed, the locknuts lose their ability to perform their functions, and there is a need to replace them.
Threaded connections are subject to extreme corrosion. If the threaded fastener does not come loose, apply penetrating oil, kerosene or another product to it and wait until the liquid is absorbed. You can try using a pneumatic or electric impact wrench. If the above methods are ineffective, you can try to gently warm up the connection. If this does not lead to achieving the required result, then you will have to resort to using a hacksaw or chisel.
Flat washers and spring washers should always be replaced during assembly. Do not place spring washers between soft metal parts (for example, from aluminum alloys), thin sheet steel or plastic.
Threaded connection sizes
For a number of reasons, car manufacturers widely use fasteners with metric threads. It is important to distinguish between SAE standard fasteners (operating in the USA) and metric connectors, since these groups of parts are not interchangeable.
The designation of bolts of all standards determines the diameter, as well as the pitch and length of the thread. For example, the SAE designation 1/2-13x1 indicates a bolt thread diameter of 1/2 inch with a pitch of 13 threads per 1 inch of length, which is 1 inch. The designation of a metric bolt M12 -1.75 x 25 means: thread diameter - 12 mm, thread pitch - 1.75 mm (thread spacing), and the length of the threaded part of the bolt is 25 mm. The bolts described above are visually almost indistinguishable. They are easy to confuse, but are not interchangeable.
SAE bolts and metric bolts differ not only in diameter, pitch and thread length, but also in head height, which is given in inches for SAE bolts and millimeters for metric bolts.
The above differences apply equally to nuts.
Therefore, different standards of wrenches must be used on the corresponding nuts and bolts. Among other things, most SAE bolts have grooves on the surface of the head, the number of which determines the class and permissible tightening force. The permissible tightening force of such bolts is directly proportional to the number of grooves on the head. On cars, bolts from class zero to class five are usually used. The class of metric bolts is indicated in their designation and does not depend on the presence and number of grooves on the surface of the head. The permissible load on metric bolts is directly proportional to their class. Vehicles typically use metric bolts of classes 8.8, 9.8 and 10.9.
Sometimes the nuts of both standards are marked with appropriate markings that determine the permissible load on the threaded connection. Typically, SAE nuts have dots marked on one side, while metric nuts are marked with numbers. The permissible load on the nut is directly proportional to the number of points marked or the value of the indicated number.
Metric studs are also marked depending on their class. The class of large diameter studs is indicated in their designation (same as metric bolts), while studs of small diameters are marked with geometric shapes that determine the class.
It should be noted that most threaded fasteners are not rated, especially if they are grade 0 to 2. If a fastener is not marked, the only way to determine its standard is to measure the thread pitch or compare the part to a similar part of a known standard.
When talking about threaded parts of the SAE standard, the name of the standard is often mentioned directly «BAE». However, it should be noted that the name «BAE» applies only to high-precision connectors. Low grade threaded parts are usually referred to as USS standard parts.
Considering that fasteners of similar sizes may have different load ratings (both SAE and metric), when reassembling, they should be installed in their respective original locations. In addition, when replacing fasteners, you must make sure that the class of the fastener being installed is not lower than the class of the part being replaced.
Sequence and method of tightening threaded connections
Most threaded connections should be tightened to the specified torque (tightening force - the torque that must be applied to a nut or bolt to unscrew it). Exceeding the specified torque results in the destruction of fasteners, while insufficient torque ultimately leads to loosening and spontaneous separation of the fastener. Depending on the thread diameter and material of manufacture, bolts, screws and studs have specific tightening forces, which in most cases are indicated at the beginning of the relevant chapters. When tightening connections, follow certain rules.
Connectors for which the tightening torque is not specified are tightened in accordance with the recommendations given in the table.
Data is based on ungreased steel or cast iron fasteners (made from non-aluminum alloys). As defined above, the load capacity of a threaded connection is determined by the material from which the fasteners are made and the diameter of the threads. The values below are averages for the second and third classes of connectors. When increasing the class of parts, higher tightening torque values are permissible.
Threaded fasteners such as cylinder head bolts, pan bolts, differential housing bolts, etc. should be tightened and unscrewed in certain sequences, which prevents deformation of the fastened elements. These sequences are usually given in the relevant chapters. If there is no specific tightening sequence, the following principles must be followed to prevent possible deformation of the fastened parts.
At the initial stage, tighten the bolts/nuts by hand. They should then be tightened one full turn in a cross or diagonal pattern. After finishing tightening one full turn, return to the first fastener and tighten the connectors half a turn in the same sequence.
Finally, before tightening to the specified torque, tighten each connector a quarter turn. When loosening the tightening force and unscrewing the connectors, perform the above procedure in reverse order.
Disassembly of elements
Disassembly of elements should be done carefully, taking during this procedure measures aimed at facilitating subsequent assembly and installation.
Always note the sequence in which parts are removed. It is also necessary to mark the original position on a pad or paint directly on parts that may be installed in different positions, such as the original position of a corrugated thrust washer on a shaft. It is recommended to lay out the removed parts on a clean surface in the order they were removed. It is also recommended to make sketches or photographs of elements in their original positions.
When removing threaded connectors, always mark their original position. Sometimes temporarily screwing the bolts into their original positions can prevent possible confusion later, as can temporarily tightening the nuts and putting washers on the corresponding studs. If it is not possible to do the above, you should store fasteners in labeled boxes or in compartments of one large box. A plastic candy box with compartments is ideal for this purpose, since each of them can accommodate bolts and nuts removed from their respective original positions (for example, bolts and nuts securing the pan, valve cover, engine mounts, etc.).
The pallet of such a box is indispensable when working with small-sized elements, such as a carburetor, generator, elements of the valve mechanism or internal panels and cladding.
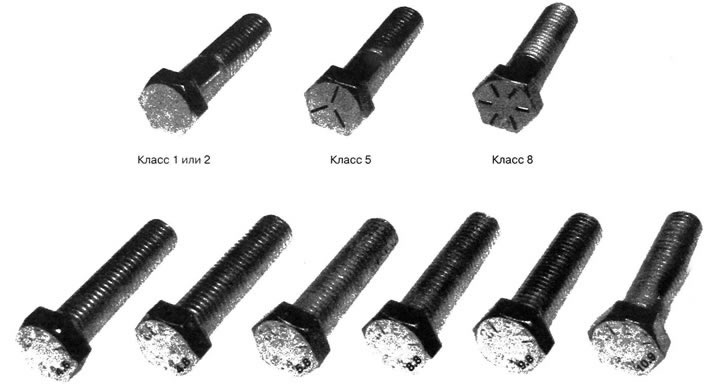
Marking of bolts depending on permissible load (SAE, USS standards; bottom row - metric bolts)
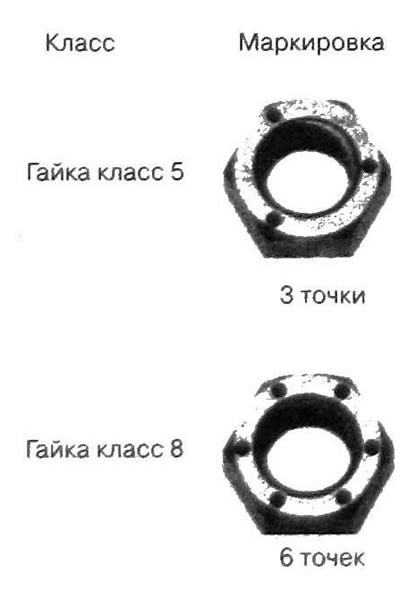
Marking depending on the permissible load on SAE nuts
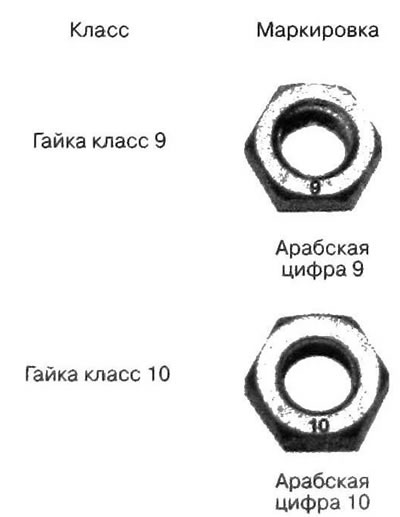
Marking depending on the permissible load on metric nuts
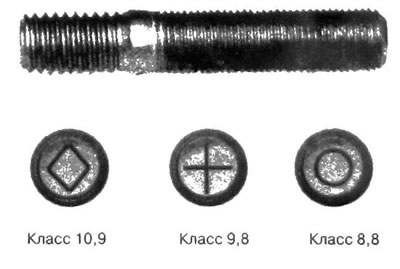
Marking depending on the permissible load on metric studs
Box compartments can be marked with paint or colored tags to identify fasteners according to their original positions.
When disconnecting harnesses, shields and wiring connectors, it is advisable to identify the open wires by labeling them with the appropriate numbers, thereby ensuring quick and correct subsequent connections during subsequent assembly.
Mating surfaces and gaskets
Gaskets are widely used in vehicle design to seal mating surfaces, which prevents joint depressurization or oil/fluid leakage. During assembly work, gaskets are often treated with lubricant or sealant. Over time, as well as under the influence of high temperature and pressure, the mating surfaces can become quite strongly attached to each other.
When separating mating parts, do not insert screwdrivers or similar tools between them. This can cause serious damage which, after reassembly, will result in leakage of oil, coolant, etc.
Separating is usually done by tapping along the mating surfaces with a hammer made of a soft material. The goal is to move or destroy the gasket. However, it should be borne in mind that this method is not suitable for disassembling pin connections.
If there must be a gasket between the mating surfaces of two parts, it should always be replaced during assembly; Install a dry gasket unless otherwise specified in the assembly manual.
Before installation, make sure that the mating surfaces are wiped clean and dry, and there are no traces of old sealant on them. When cleaning mating surfaces, if necessary, use an appropriate solvent and a tool that will not damage the surface.
Do not use solvents when cleaning the mating surfaces of parts made of plastic or other composite material. Remove burrs using a lubricated abrasive stone or a fine-grit file. It is recommended to use a copper scraper as this material is generally softer than the material used to separate the parts, preventing damage to surfaces during the cleaning process. Make sure all threaded holes are clean and do not allow any sealant to enter them unless otherwise specified in the assembly instructions.
Make sure that all holes, channels and tubes are not clogged, and if necessary, blow them out with compressed air.
Metric thread | ft - lbs | Nm |
M-6 | 6-9 | from 9 to 12 |
M -8 | 14-21 | from 19 to 28 |
M -10 | 28-40 | from 38 to 54 |
M -12 | 50-71 | from 68 to 96 |
M -14 | 80-140 | from 109 to 154 |
Inch thread on tubular connections | ft - lbs | Nm |
1/8 | 5-8 | 7-10 |
1/4 | 12- 18 | 17-24 |
3/8 | 22-33 | 30-44 |
1/2 | 25-35 | 34-47 |
US Standard | ft - lbs | Nm |
1/4-20 | 6-9 | 9- 12 |
5/16-18 | 12-18 | 17-24 |
5/16-24 | 14-20 | 19-27 |
3/8-16 | 22-32 | 30-43 |
3/8-24 | 27-38 | 37-51 |
7/16-14 | 40-55 | 55-74 |
7/16-20 | 40-60 | 55-81 |
1/2-13 | 55-80 | 75 - 108 |
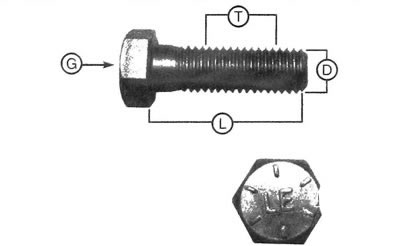
Designation of sizes and classes of bolts of SAE and USS standards: G - Marking of class (according to permissible load); L - length of the working part (in inches); T - Thread pitch (quantity in one inch); D - Nominal thread diameter (in inches)
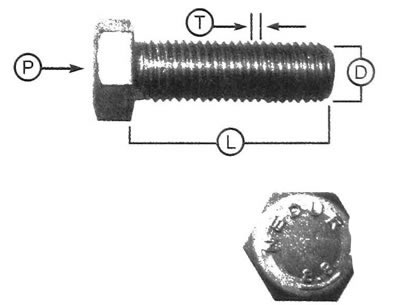
Designation of dimensions and class of metric bolts: P - Specified class (according to permissible load);L - length of the working part (in millimeters);T - Thread pitch (distance between threads in millimeters);D - Thread diameter
Disconnecting hoses
Warning: if the vehicle is equipped with an air conditioning system, do not disconnect the hoses of the system without first discharging it at a service station of the appropriate profile.
The precautions taken when disconnecting hoses are the same as when disconnecting gasket mating surfaces. Do not damage the surface of the connector, leading to liquid leakage or depressurization in the future. This phenomenon occurs especially often when the surfaces of the radiator pipes are damaged. Due to various chemical reactions, rubber can stick to the metal hose pipe. Before removing the hose, loosen the clamps. Then, grasping the part of the hose located on the nozzle with an appropriate device, rotate the hose around the axis of the nozzle. Repeat forward rotations until the resistance to removal weakens, then disconnect the hose. If possible, treat the hose and the outside of the fitting with silicone-based lubricant or other suitable lubricant to make removal easier. During subsequent installation, treat the inner surface of the hose and the outer surface of the pipe with the same lubricant - this will make the connection easier.
If there is an urgent need to replace a hose that cannot be removed, as a last resort you can cut it off and then remove the remaining part from the pipe. When cutting a part of the hose, be careful not to damage the surface of the pipe.
If there are signs of wear or damage to the mounting clamp, do not reinstall it under any circumstances. Spring clamps weaken over time, so it is recommended to replace them with worm clamps whenever a hose is removed/installed.
Tools
Selecting high-quality tools is the key to successful repairs and efficient vehicle maintenance. For motorists who do not have such tools, purchasing a complete set will cause a significant expense, which can only be partially reduced by making some of the accessories yourself. However, if the purchased tools meet safety requirements and are of high quality, they will last for many years and will be an extremely useful purchase.
To help the motorist decide what tools he needs to perform the various jobs described in this manual, the authors have compiled three lists under the following headings: "Set of tools for maintenance and minor repairs", "Set of tools for medium and major repairs" And "Special tools and accessories".
Car owners who do not have sufficient repair experience should start by purchasing a set of tools for maintenance and minor repairs, and limit themselves to performing simple work. Then, as you gain confidence and experience, you can move on to more complex tasks, purchasing additional tools as needed. Thus, over a long period of time and without large one-time costs, you can increase the set of tools for maintenance and minor repairs to a set intended for medium and major repairs. Experienced car enthusiasts can have a tool kit suitable for most repair jobs and supplement it with tools from "special" list, if they are sure that the costs of their acquisition are justified by frequent use.
Set of tools for maintenance and minor repairs
This list contains a set of tools necessary for maintenance and minor repairs. It is recommended to buy combination wrenches (a spanner on one side and an open-end wrench of the same size on the other); these wrenches are more expensive but have the benefits of both types.
- Set of wrenches:
Inch - from ¼ to 1 inch
Metric - from 6 to 19 mm inclusive
- Adjustable wrench - 35 mm or 8 inches (approximately)
- Candle key (with rubber insert)
- Tool for adjusting spark plug gap
- Set of probes
- Wrench for unscrewing brake bleeder fittings
- Flat end screwdriver - 100mm length, 6mm diameter (5/16 x 6 inches);
- Phillips head screwdriver - 100mm length, 6mm diameter (2 x 6 inches);
- Pliers
- Hacksaw (small) with a set of blades
- Pressure gauge
- Grease blower
- Oil can
- Fine-grit cloth sandpaper
- Wire brush
- Tool for servicing battery cables and terminals
- Oil filter remover
- Funnel (medium size)
- Protective glasses
- Vertical supports for a car raised by a jack (2 pcs.)
- Drain pan
Note: if regular maintenance procedures are supposed to be carried out in the context of current periodic maintenance, then the above list must be supplemented with a strobe flash frequency meter/breaker contact closure period, as well as a strobe light. These tools are included in the list of special tools, but are mentioned here because they are necessary for adjusting the ignition system on most cars.
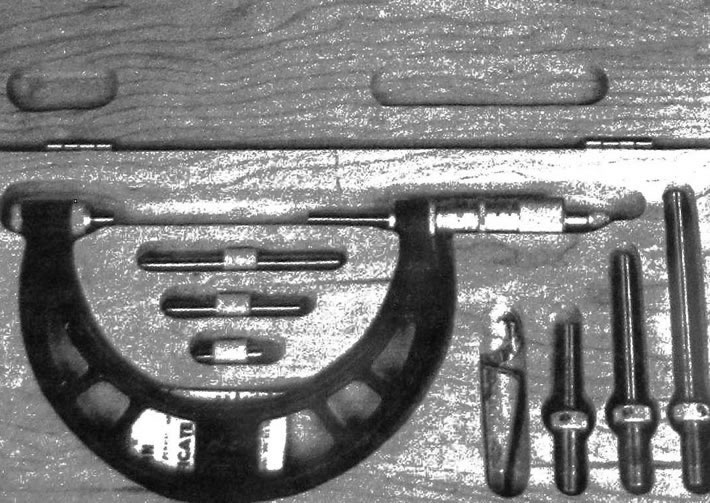
Pressure gauge
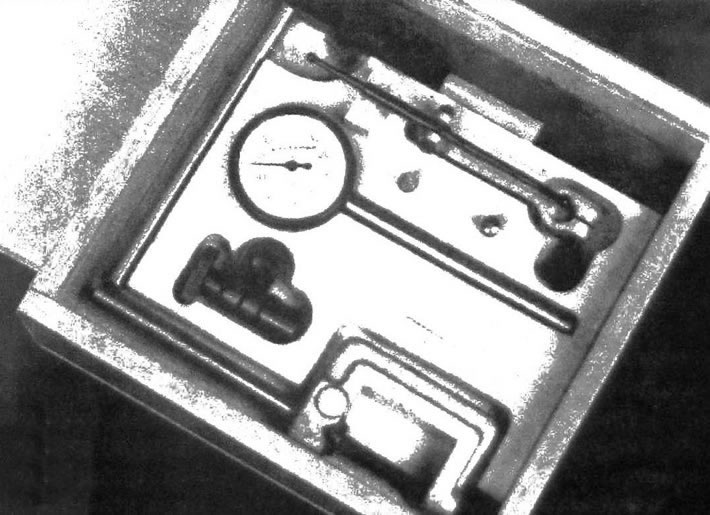
Meter with dial indicator
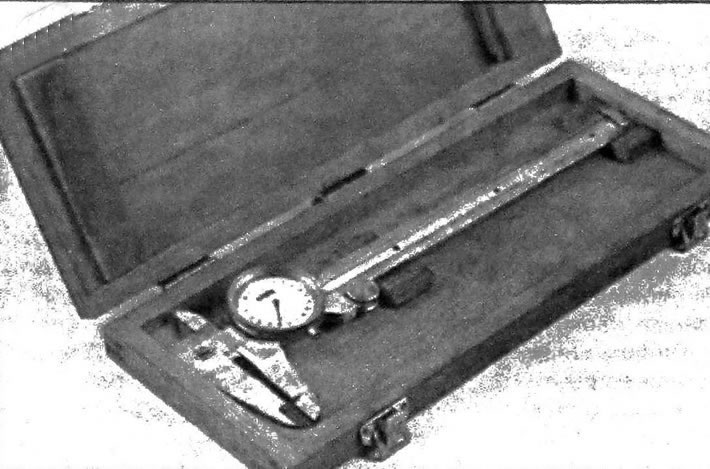
Caliper with dial indicator
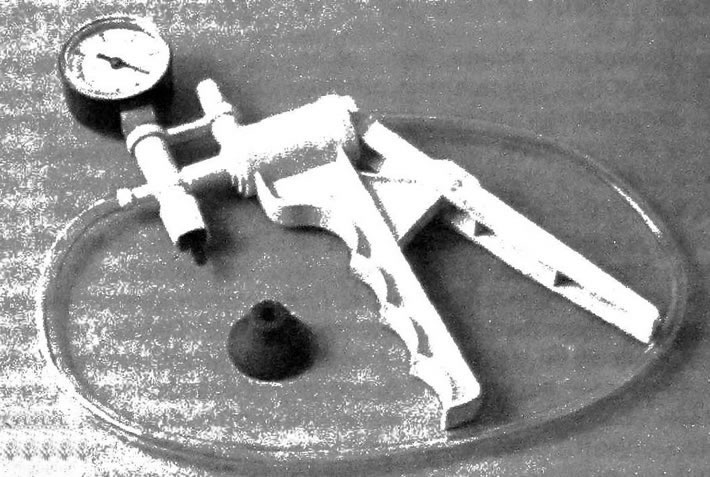
Portable Vacuum Pump
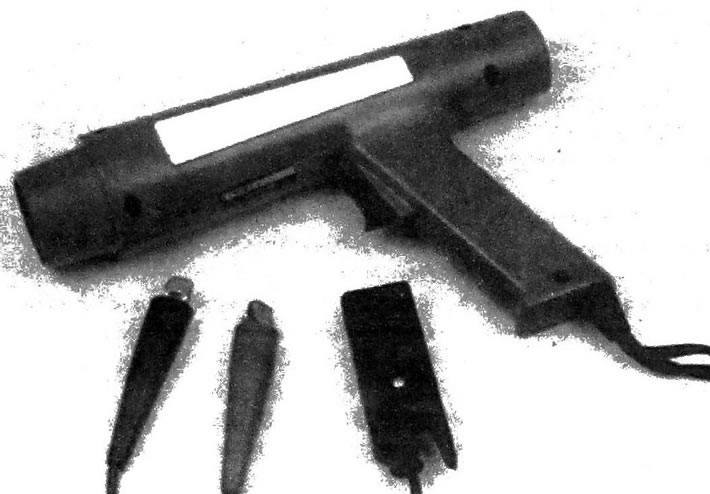
Strobe
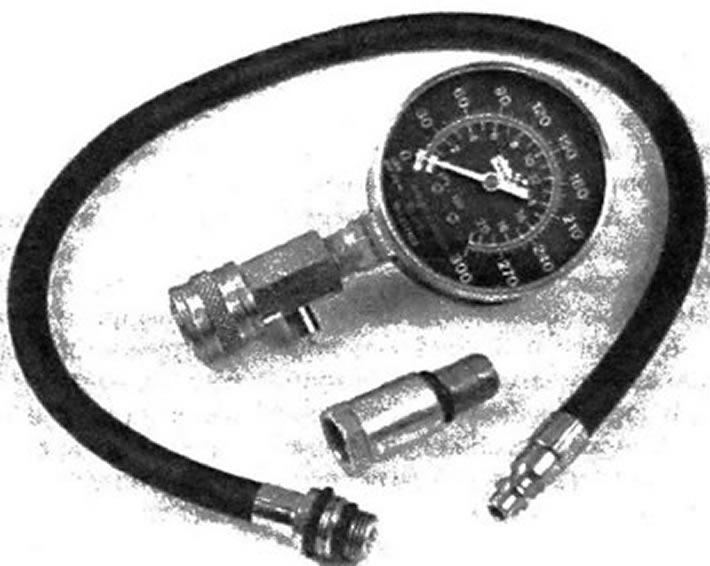
Compression gauge with adapter for spark plug hole
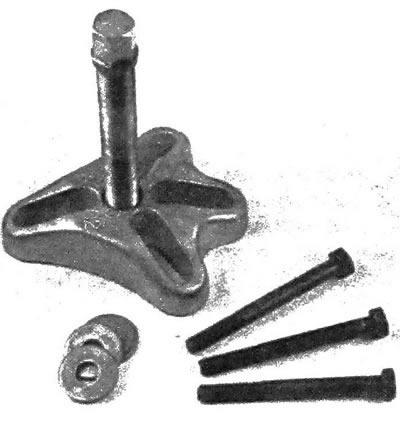
Steering Damper/Steering Wheel Puller
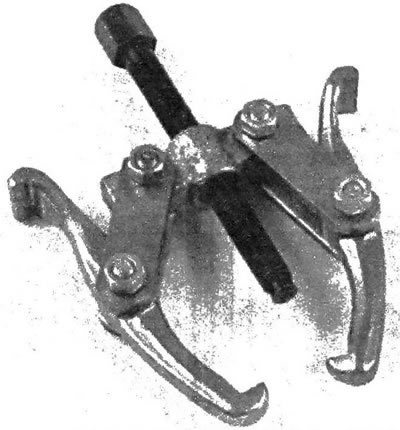
Universal puller
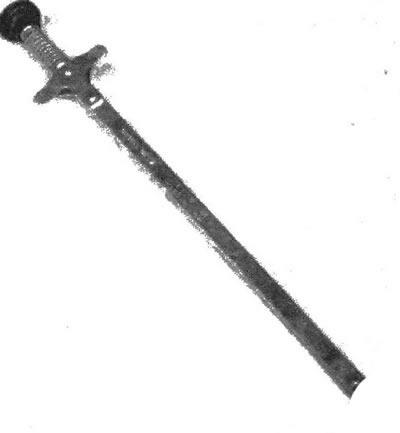
Hydraulic valve lifter puller
Set of tools for medium and major repairs
These tools are necessary when carrying out major repairs, in addition to the list of tools for maintenance and minor repairs. This listing includes a socket set. Although it is expensive, it is absolutely necessary for more or less serious work. It is recommended to purchase a lever with a ratcheting mechanism and a socket for 1/2 heads". However, despite the fact that the lever is 3/8" It has significant dimensions and a relatively high cost; it can be used with many large-diameter heads. It is preferable that the mechanic have two levers with sockets for socket heads - 1/2" and 3/8".
- Socket set
- Driver with reversible ratchet (for use with sockets)
- Extension 250 mm long (for use with sockets)
- Drive with cardan joint (for use with sockets)
- Torque wrench (for use with sockets)
- Impact tool for separating ball joints
- Soft-faced hammer (plastic, aluminum or rubber)
- Screwdrivers:
with flat end - long and strong, short (wide), narrow (for working with electrical system elements);
with cross-shaped end - long and strong, short (wide)
- Pliers:
with long grips; side cutters (for working with electrical system elements), pullers for spring rings - external and internal
- Chisel - 25 mm (½ inch)
- Marker for metal parts
- Scraper made from flattened copper tube
- Kerner
- Punchers
- Steel ruler
- Keys Alena (hexagons)
- Set of files
- Wire brush
- Car stands (2 pcs.)
- Hydraulic jack
Note: the list can be expanded to include another very useful tool - an electric drill with a set of drills and a chuck designed for a maximum drill diameter of 3/8 inches (M10).
Special tools and accessories
The tools and accessories on this list are not used regularly, are expensive, or have limited applications. The purchase of many of them will not be justified if complex mechanical work is rarely performed. Maybe it's worth teaming up with some friends (or join a car club), to purchase such tools. You can also rent them from specialists.
The following list includes only those tools and accessories that are commercially available, and not those that the vehicle manufacturer produces specifically for dealers and branded service stations. References to such tools may occasionally appear throughout this manual.
This book usually provides an alternative method of doing the job, without the use of special tools. But sometimes there is no alternative to them. If this is the case, and the appropriate tools cannot be purchased or rented, then the work will have to be entrusted to the specialists of the company station.
- Valve Spring Puller
- Tool for cleaning piston ring grooves
- Piston ring puller
- Piston ring installation tool
- Compressometer
- Reamer for cylinders
- Hone for surface treatment of engine cylinders
- Engine cylinder bore gauge
- Micrometer and/or caliper with dial indicator
- Hydraulic valve lifter puller
- Hinge pin release tool
- Universal puller
- Pneumatic impact wrench
- Meter with dial indicator
- Strobe
- Portable vacuum/pressure pump
- Strobe flash frequency/breaker contact closure period meter
- Tachometer
- Multimeter
- Telfer
- Device for removing and installing springs of brake system mechanisms
- High load hydraulic floor jack
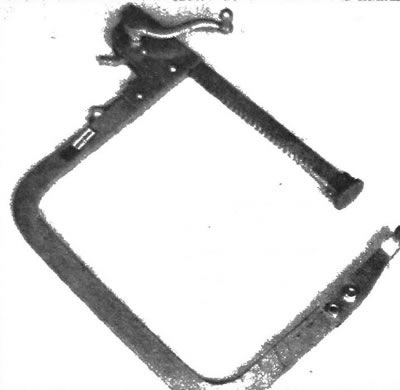
Valve spring remover
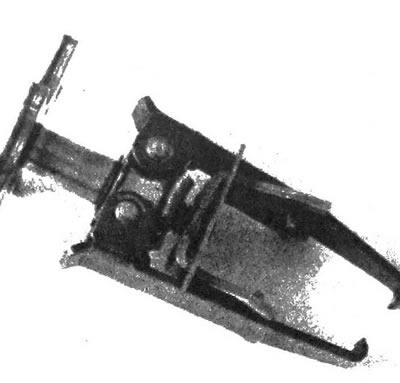
Valve Spring Puller
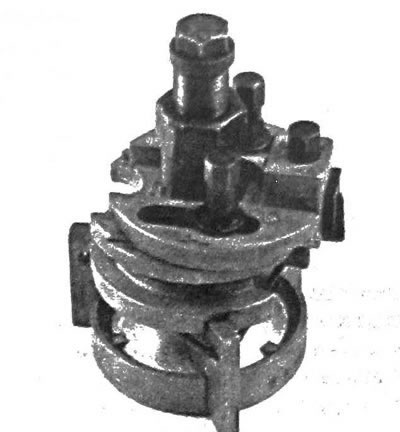
Scan
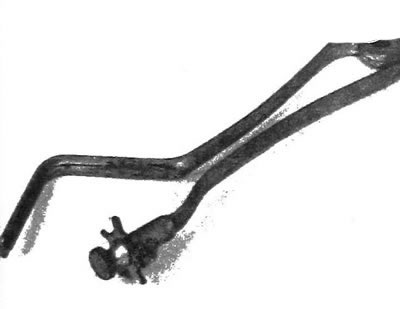
Tool for cleaning piston ring grooves
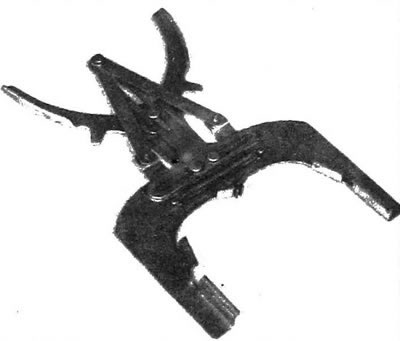
Tool for removing/installing piston rings
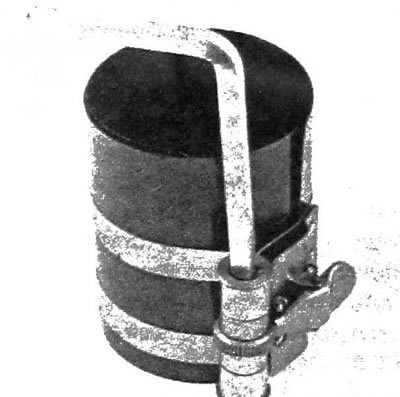
Piston ring puller
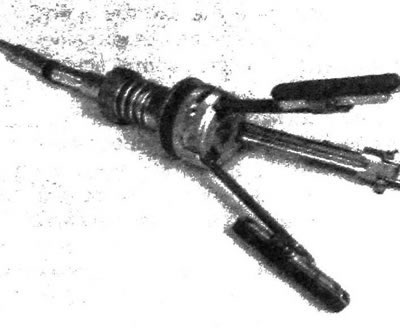
Hone for processing the working surface of engine cylinders
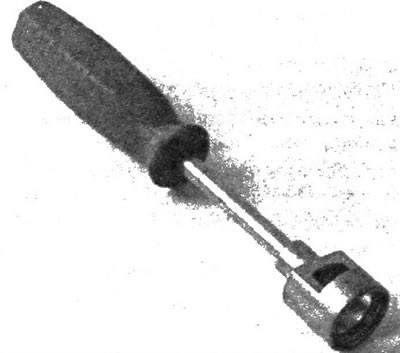
Device for compressing brake system springs
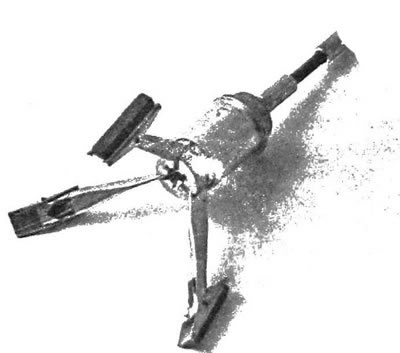
Hone for surface treatment of brake cylinder
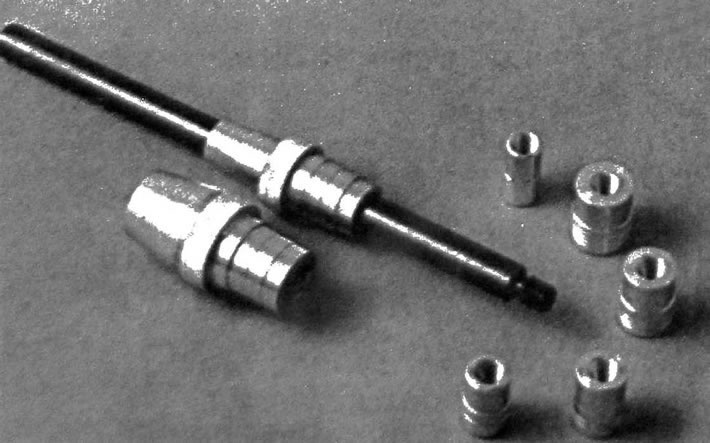
Clutch disc centering tool
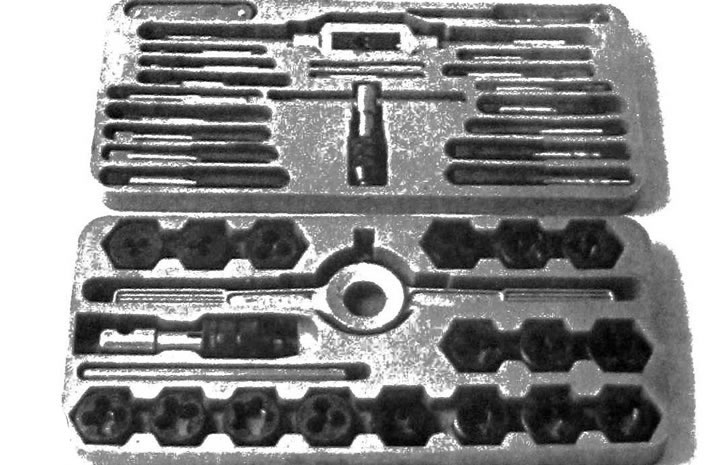
Set of dies and taps
Purchasing tools
For a car enthusiast - a mechanic who independently carries out maintenance and repair of a car, even with relatively little work experience, there are several sources for purchasing tools. If you intend to carry out only maintenance and minor repairs, then you can limit yourself to purchasing tools that correspond to this level in a retail chain. If you plan to carry out serious repair work, then you should purchase a simple set of tools in one of the company stores. As a rule, such a set can be purchased at a wholesale price; moreover, special boxes are often supplied with the set. Since additional tools may be needed in the future, it is advisable to purchase a box, thus allowing for possible expansion of the set. Purchasing tools over time allows the mechanic to avoid large one-time costs and to purchase only those tools that are needed.
Supermarkets and specialty parts stores often offer excellent, high quality tools and accessories at low prices.
Remember that you don't have to buy the most expensive tools, but avoid buying the cheapest ones too. Beware "profitable" purchases of tools offered in car parks, or sold at car markets from car trunks. There are many high-quality tools available for sale at reasonable prices, but you should always try to buy products that meet safety requirements. If necessary, consult the owner or manager of the store, (www.monolith.in.ua)
Storage and maintenance of proper technical condition of instruments
Having purchased the necessary set of tools, keep it clean and in good condition. Before storing tools after use, always clean them with a clean, dry cloth to remove dirt, oil and metal particles. Never leave them scattered after work.
After finishing work in the engine compartment, make sure that all tools and accessories are removed from the hood. This will prevent them from being lost during the engine mileage test. For tools such as screwdrivers and pliers, a regular shelf on the wall is very convenient. Store wrenches and socket wrench heads in a metal box. Any measuring instruments, indicators, etc. must be stored in places where they will be protected from damage and corrosion.
When using tools, take some time to care for them. Sooner or later, chips appear on the hammer head, and screwdriver blades become dull. Timely treatment with sandpaper or a file will quickly restore the original technical condition of such tools.
Restoring damaged and worn threads
Sometimes the threads of a nut or bolt hole become damaged.
As a rule, this occurs due to exceeding the permissible tightening force.
Wear and damage to threads is a fairly common occurrence, especially when it comes to the threads of parts made of aluminum alloys, since such material is quite soft and quickly wears out due to friction.
There is usually acceptable thread wear. After being driven with a tap or die, it is still capable of fulfilling its purpose. One day, the wear of each thread will reach its limit. There are three ways to restore worn threads:
1) Drill a hole, cut a thread of a larger repair size in it and install a bolt, screw or stud of a larger diameter.
2) Drill a hole and cut a thread in it for the repair bushing, drill a hole in the bushing and cut a thread in it for a bolt of the original size. You can also purchase a bushing with an existing threaded hole of the required original size. In this case, all that remains is to drill a hole and cut a thread in it for the bushing, then install the bushing using a bolt and locknut. After installing the bushing, the locknut and bolt are removed.
3) The third restoration method involves the use of a patented thread repair kit «Heli-Coil» or «Slimsert» . Use these easy-to-use repair kits to repair damaged through-hole and blind-hole threads. They can also be used to cut threads of various diameters. Drill a hole and cut a thread in it using the special tap included in the kit. Installing the repair kit will ensure the presence of a threaded hole of the required diameter and with the specified thread pitch.
Regardless of the method used, carry out the work carefully and consistently. Carelessness in performing these relatively simple procedures can result in a waste of time and money, as well as possible material damage if an expensive part is destroyed.
Workplace
When talking about tools, we should not forget about the workplace. If the work being carried out is outside the scope of normal maintenance, then the need to have a suitable workstation is obvious.
Many car enthusiasts, due to circumstances, are forced to remove the engine or similar units from the car in conditions that are not as favorable as those available in a repair shop. Such work should always be carried out indoors or under cover.
Any disassembly should be done on a clean, flat workbench or table of suitable height. Any workbench should be equipped with a vice with a jaw opening of at least 100 mm, which is suitable for most jobs.
As mentioned above, it is necessary to provide a dry and clean place for storing tools, as well as for all kinds of lubricants, liquids, touch-up paint, etc. You should also have a container for draining used engine oil and operating fluids. Old plastic cans of antifreeze or antifreeze are ideal for this purpose. To turn such a canister into a drain pan, simply cut off one of the large edges.
To protect the floor surface from oil and liquids that may leak from the vehicle, place a large sheet of cardboard under the vehicle. You should keep an old blanket or a special vinyl cover on hand to protect your car's paintwork and glass.
Last but not least, always keep some old newspapers and clean cloth napkins in your work area that do not leave threads or lint on the surface being wiped, and keep your work area clean.