2. Supply, drain and vent pipes run from the fuel tank to the engine compartment. The pipelines are attached to the bottom with clamps and screws. These pipelines should be inspected from time to time for leaks, kinks, kinks and dents.
3. If dirt is found in the system or fuel filter during disassembly, the pipeline must be disconnected and purged. Check the fuel pre-filter on the instrument for damage and wear (see section 7).
Steel pipelines
4. If fuel line or tube replacement is required, use welded steel tubes that meet GM 124-M specification or equivalent.
5. Do not use copper or aluminum tubing to replace steel tubing. These materials cannot withstand normal vehicle vibration.
6. Since the fuel lines are used on vehicles with high pressure fuel injection, they require special attention.
7. Most fuel lines have O-ring threaded fittings. If the fasteners loosen, carry out the following maintenance and replacement operations:
- A) When disassembling connections, use an auxiliary wrench in order to avoid twisting the pipelines.
- b) Check all o-rings for cuts, cracks and excessive wear. Replace those that are worn or damaged.
- V) If fuel lines are being replaced, always use genuine parts or parts that meet GM standards listed in this section.
Rubber hoses
Attention! For vehicles equipped with a multiport fuel injection system, use only branded hoses or their equivalents for replacement. Other hoses may fail due to the high pressure in this system.
8. If rubber hose is used to replace metal piping, use reinforced, fuel resistant hoses (specifications GM 6163-M) with an inscription "Fluoroelastomer". A hose that does not bear this label may fail prematurely or fail to meet ''Federal Exhaust Gas Control Standards''" USA. The inner diameter of the hose must match the outer diameter of the tube.
9. Do not install rubber hoses closer than four inches from exhaust system components or ten inches from catalyst. Metal tubes and rubber hoses should never rub against the frame. A minimum of 1/4 inch clearance must be maintained around the tube or hose to prevent contact with the frame.
Removal and installation
Note. Quick release (threadless) clean the fasteners before disconnecting to prevent dirt from entering the fasteners. After disconnection, clean the fasteners with compressed air and apply a few drops of oil.
10. Relieve fuel pressure (see section 2) and disconnect the supply, drain or vent pipes from the fuel tank (see illustration).
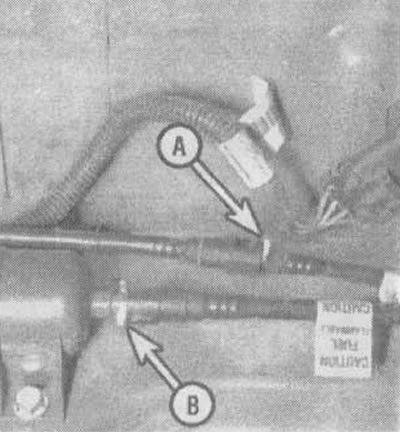
4.10. Drain (A) and serving (B) tubes are easily removed by squeezing the antennae and separating each connector (3.1L engine shown)
Note. Some fuel line connections may be threaded. To prevent twisting, use an auxiliary wrench when disconnecting the connectors.
11. Remove all parts securing the fuel lines to the car body.
12. Disconnect the fasteners connecting the fuel hoses to the metal tubes of the engine compartment (see illustration).
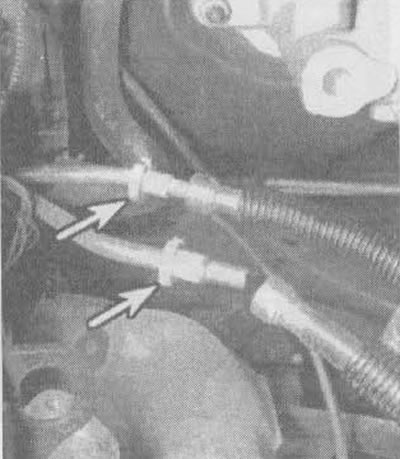
4.12. Use special tools to disconnect fuel lines (J37088-A or similar) and put them on the connectors (indicated by arrows), to disconnect the tubes (3.1L engine shown)
13. Installation is carried out in the reverse order. Make sure that new O-rings are installed on the threaded connections (see illustration). Apply a thin film of clean engine oil to the O-rings.
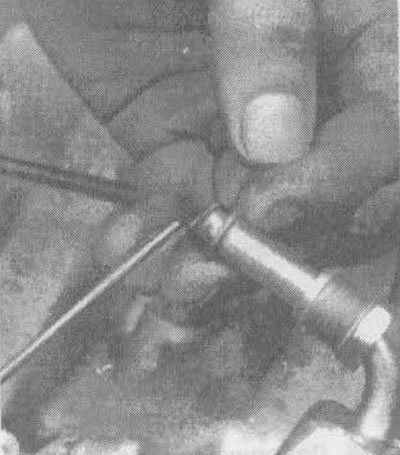
4.13. Always replace fuel line o-rings (if they are)
Repair
14. At repair locations, cut fuel hose four inches longer than the length of tube being replaced. If tubing longer than six inches is being replaced, use a combination of steel tubing and hose so that the length of the hose does not exceed ten inches. Always lay the pipeline in the same place.
15. Cut off the ends of the tubing with an appropriate tool. Use a flare tool and flare both ends of the tube. If the tube is too badly corroded to withstand the flaring operation without breaking, it should be replaced.
16. Use a screw clamp for the hose. Slide the clamp over the tube and push the hose through it. Tighten the clamps on each section of the repaired line.
17. Attach the pipes to the frame properly to prevent friction.