Note. Broken valve springs and damaged valve stem seals can be replaced without removing the cylinder heads. Typically, this operation requires two special tools and a source of compressed air, so read this section carefully and borrow or purchase the necessary equipment before starting work. If no compressed air source is available, use a piece of nylon cord to prevent the valves from falling into the cylinder during operation.
1. Remove the valve cover from the corresponding cylinder head (see section 4).
2. Remove the spark plug from the cylinder with damaged parts. If it is necessary to replace the cuffs on all valve stems, turn out the candles from all cylinders.
3. Turning the crankshaft, set the piston in the cylinder with damaged parts to the TDC position on the compression stroke (see section 3). If you are replacing the seals on all valve stems, start with the 1st cylinder and continue replacing them with the others one by one. Move from one cylinder to another, following the sequence of their work (see technical data in this chapter).
4. Screw the adapter into the spark plug hole (see illustration) and connect a hose from a compressed air cylinder to it. Note. Most compression gauges are equipped with a screw-on adapter that fits into a quick-release air hose fitting.
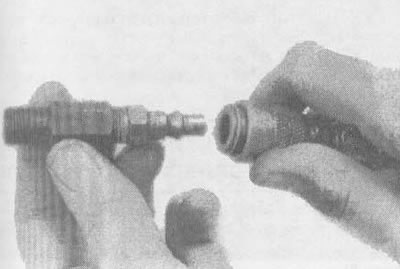
7.4. It looks like an adapter to the air hose, which is screwed into the hole for the spark plug
5. Having unscrewed a nut, remove racks and a yoke of the valve and take a bar. If it is necessary to replace the cuffs on all valve stems, then all valve rockers and rods must be replaced at the same time (see section 6).
6. Direct a jet of compressed air into the cylinder.
Attention! Under the pressure of the air jet, the cylinder may move down, resulting in a sudden turning of the crankshaft. If the wrench used to set the cylinder to TDC has not been removed from the end of the crankshaft, it may cause injury when the shaft is turned.
7. Valves must be held in place by air pressure. If the technical condition of the working surfaces or valve seats is unsatisfactory, then due to air leakage, the jet pressure will not be sufficient to hold the valves. In this case, you must use a different method.
8. If no compressed air source is available, position the piston just short of TDC on the compression stroke by about 45°, then push the end of a long nylon cord into the spark plug hole until it fills the combustion chamber. The other end of the cord must remain outside the engine, otherwise it will be difficult to reach. Using a ratchet wrench, turn the crankshaft in the direction of rotation until you feel slight resistance to turning.
9. Having stuffed rags into the holes of the cylinder head above and below the valves to prevent parts from falling out of the engine, compress the valve spring with a special tool. Take out the crackers.
Note. There are two types of valve spring compressors with the cylinder head not removed. One of them works on the principle of capturing the lower coils of the spring and pressing on the spring plate when turning the handle. The second device is a lever type; here, the stud and nut of the valve rocker are used as a stop (see illustration). Both devices are quite effective, but the cost of the second, as a rule, is somewhat lower.
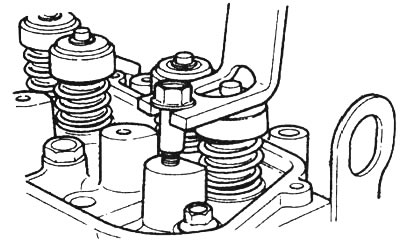
7.9. To replace the valve collar or valve springs without removing the cylinder head, you need to press the spring with a special tool and remove its cotters
10. After removing the spring plate, boot and valve spring, remove the cuff (see illustration).
Note. If the air jet is not strong enough to hold the valves closed during this operation, the seat or valve seat may be damaged. In this case, the cylinder head must be removed for additional repair work.
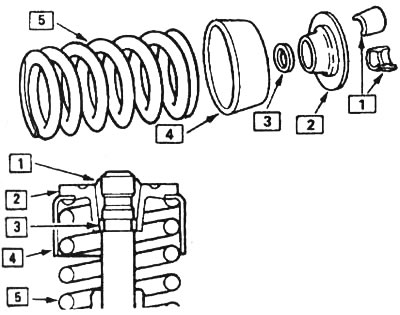
7.10. Valve spring with related parts: 1 - crackers, 2 - spring plate, 3 - sealing ring, 4 - boot, 5 - valve spring
11. Wrap a rubber band around the top of the valve stem to prevent the valve from falling into the combustion chamber, then reduce the air pressure.
Note. If a nylon cord was used instead of a jet of air, rotate the crankshaft slightly in the opposite direction of normal rotation.
12. Check the valve stem for damage. Turning the valve in the guide sleeve, check its shank for eccentricity. The presence of eccentricity may indicate that the valve stem is bent.
13. Move the valve up and down in the guide sleeve to check if it is sticking. The presence of sticking means that either the valve stem is bent or the valve guide is damaged. In both cases, you will have to remove the cylinder head for additional repairs.
14. Reapply compressed air to the cylinder to keep the valve closed and wind the rubber band off the valve stem. If a nylon cord was used instead of a jet of air, rotate the crankshaft in the direction of normal rotation until slight resistance to rotation appears.
15. Apply a layer of engine oil to the valve stem and install a new cuff.
16. Install a spring with a boot over the valve.
17. Install the spring plate. While compressing the valve spring, carefully insert the cotters. To prevent crackers from falling out during assembly, put a small amount of grease in them (see illustration).
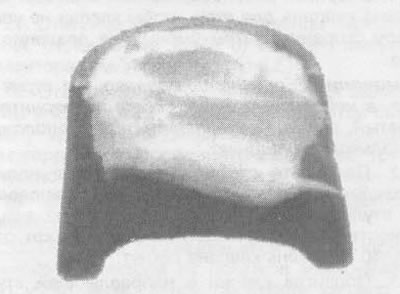
7.17. Crackers do not always spontaneously hold in place, so put a drop of lubricant in each of them before assembly, as shown in the photo: thanks to it, they will be held on the valve stem until the spring is installed
18. After releasing the pressure of the device on the spring, make sure that the crackers are in place.
19. Disconnect the air hose and unscrew the adapter from the spark plug hole. If a nylon cord was used instead of compressed air for this work, remove it from the cylinder.
20. Install rocker arm and stem (see section 6).
21. Screw in the spark plugs and connect the ignition wires to them.
22. Install valve covers (see section 4).
23. Start the engine and let it run for a while, then check the valve train for oil leaks or unusual noises coming from the head cover area.