Reducer 10.5"
1. Install the reducer.
Caution: Before servicing the bearing cap, measure and record the thickness of the pinion bearing cap shim.
2. Install the original pinion bearing cap shim. If the original washer is not available, install a 0.41mm thick washer.
Caution: Do not apply grease to the washer at this time.
3. Install the bearing cover.
4. Install the bearing cap bolts. Tighten the bolts. Tightening torque 88 Nm.
5. Adjust the engagement clearance.
6. Check the shape and position of the contact patch of the teeth of the drive and driven gears of the gearbox.
7. If the shape and position of the contact patch is not correct, adjust the position of the drive gear:
- A) Loosen the gear bearing cover bolts.
- b) Remove the cover.
- V) Remove the adjusting washer.
- If the contact patch is too high, install a washer one size larger (approx. 0.25 mm).
- If the contact patch is too low, install a washer one size smaller (approx. 0.25 mm).
- G) Install the selected shim.
- d) Install the bearing cover.
- e) Install and tighten the bearing cover bolts. Tightening torque 88 Nm.
- and) Check the shape and position of the contact patch of the teeth of the drive and driven gears of the reducer.
Note: shims are available in thicknesses from 0.15 to 0.61 mm in increments of 0.2-0.3 mm.
8. Check up size of a backlash in gearing.
Gearboxes 8.6" and 9.5"
Note: Special measuring devices are required here.
Attention: when taking measurements, all tools, the seats of the side bearings of the differential and the bearing rings of the drive gear of the gearbox must be absolutely clean.
1. Lubricate the gearbox drive gear bearings with gear oil.
2. Install the pinion bearings in the gear case.
3. Assemble and install the measuring tool as shown in the figure.
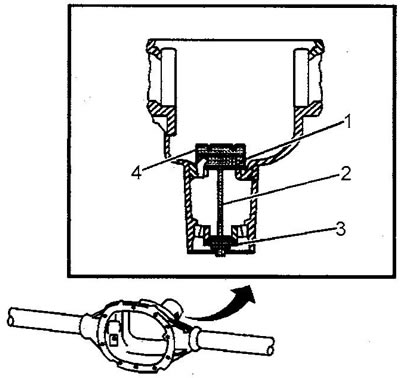
4. Holding the cork (4) tools with a torque wrench, turn the nut (3) until a torque of 1.7 Nm is obtained. Rotate the assembly several times in both directions to seat the bearings.
5. Check up size of the moment of cranking. If the torque is less than 1.7 Nm, tighten the nut until the torque falls within the range of 1.7-2.3 Nm.
6. Install the second tool in the gearbox housing as shown.
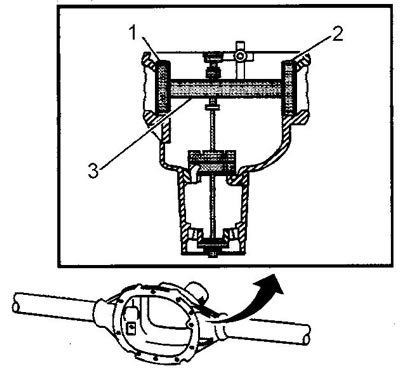
7. Install differential side bearing caps.
8. Install the bearing cap bolts. Tighten the bolts. Tightening torque 75 Nm.
9. Rotate the axis (3) in disks (1) And (2). The axle must rotate freely in both directions. If there is no free rotation, dismantle the device and inspect all seats, eliminate the noticed shortcomings (for example, skew). Install the fixture again.
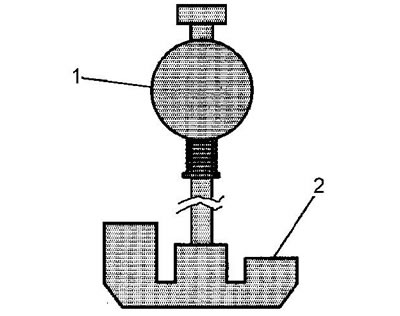
10. Align the axle plunger (1) measuring platform fixtures (2).
11. Install a dial indicator on the fixture axis as follows:
- A) Loosely slide the indicator clamp onto the axle.
- b) Install the indicator pad on the axle support post.
- V) Create a preliminary stroke of the indicator about three-quarters of the turn of the arrow.
- G) Tighten the indicator clamp.
12. Move the axle plunger back and forth and determine the location of the greatest deviation of the indicator needle.
13. At the point of maximum deflection, move the indicator until the indicator pointer is at zero.
14. Move the tool axle plunger to confirm that the indicator is properly zeroed.
15. Retract the axle plunger until it leaves the measuring platform.
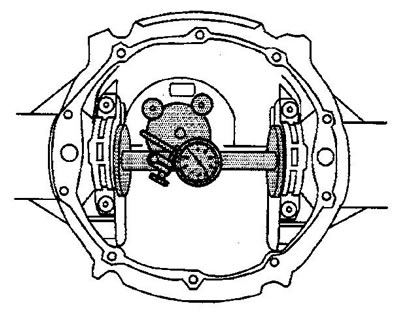
16. The value on the indicator now corresponds to the thickness of the drive gear shim.
17. Select the appropriate shim.
18. Remove measuring devices.
19. Remove pinion bearings.
20. Install the selected shim between the gear and the inner bearing.