Note: Installation procedures for individual parts not covered here are described above in the relevant sections. Ignore the final operations that are performed on the vehicle.
Before Assembly
- Dirt will cause premature wear on a repaired engine, so make sure you are assembling with absolute cleanliness.
- Use accurate measuring tools when evaluating wear or matching parts.
- If old parts are installed, install them in their original positions.
- When assembling, lubricate the parts with clean engine oil. This will provide initial lubrication when the engine is first started.
Installing cylinder block plugs
Note: Cylinder block plugs removed during disassembly can be reinstalled if they are not damaged.
1. Apply a bead of sealant with a diameter of approximately 3 mm to the sealing washer (115) coolant heater.
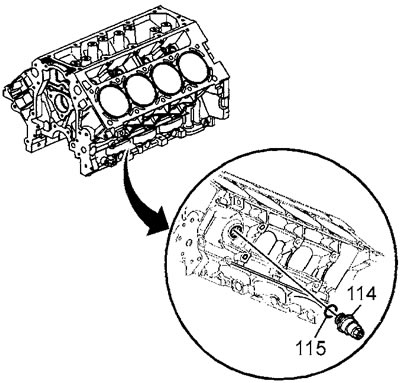
2. Install heater (114) to the cylinder block. Tightening torque 50 Nm.
3. Apply a bead of sealant with a diameter of approximately 3 mm to the sealing washer of the rear drain plug of the right half block.
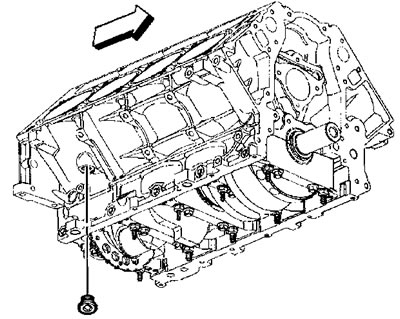
4. Install the right half block rear drain plug. Tightening torque 60 Nm.
5. Apply a bead of sealant with a diameter of approximately 3 mm to the sealing washer (117) front plug of the oil gallery of the left semi-block.
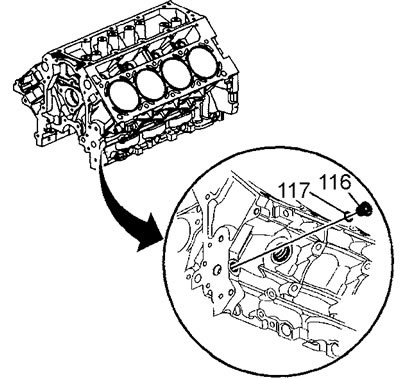
6. Install the front plug (116) oil gallery of the left semi-block. Tightening torque 60 Nm.
7. Apply a bead of sealant with a diameter of approximately 3 mm to the sealing washer (113) rear plug of the oil gallery of the left semi-block.
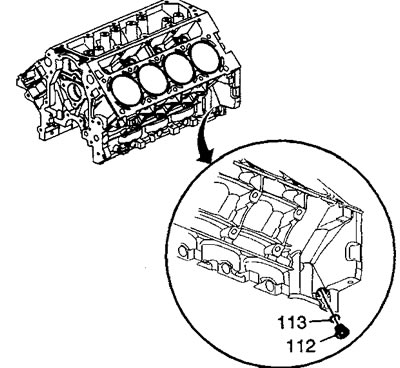
8. Install the front plug (112) oil gallery of the left semi-block. Tightening torque 60 Nm.
9. Check the condition of the sealing ring of the rear plug of the oil gallery of the block. If the O-ring is in good condition, it can be reused.
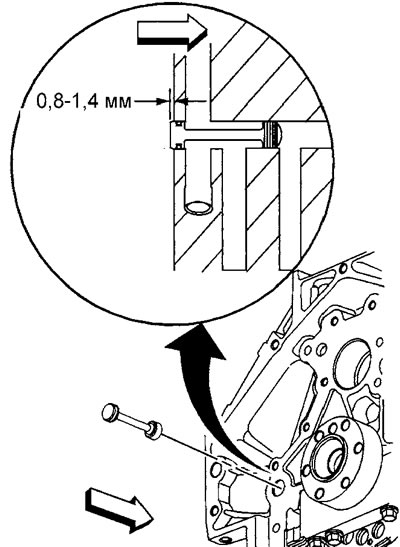
10. Lubricate the O-ring with clean engine oil.
11. Install the o-ring on the plug.
12. Install the rear plug so that it protrudes from the block by 0.8 - 1.4 mm.
13. Apply locking adhesive to the NEW front plug (101) oil gallery.
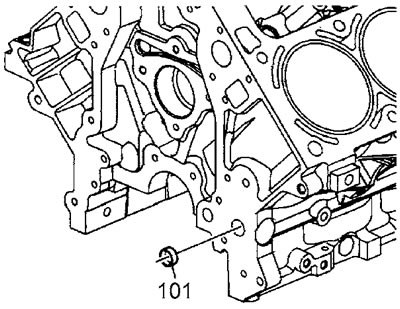
14. Install the front plug so that it sinks 2.2-2.8 mm beyond the plane of the block.
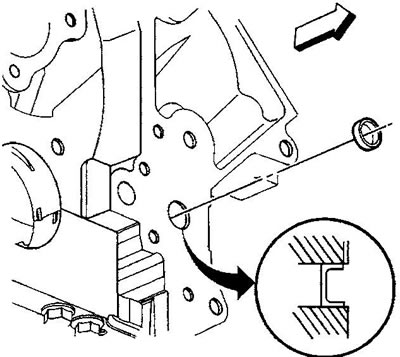
15. Install knock sensor (718) left half block side and tighten the bolt (739) sensor mounts.
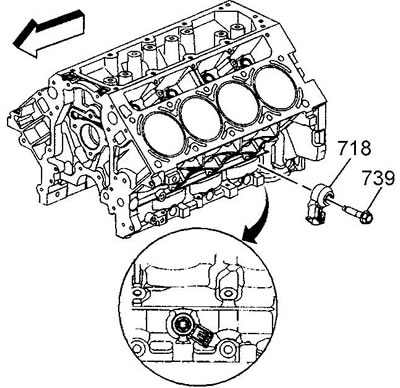
Tightening torque 20 Nm.
16. Install knock sensor (718) right semi-block and tighten the bolt (739) sensor mounts.
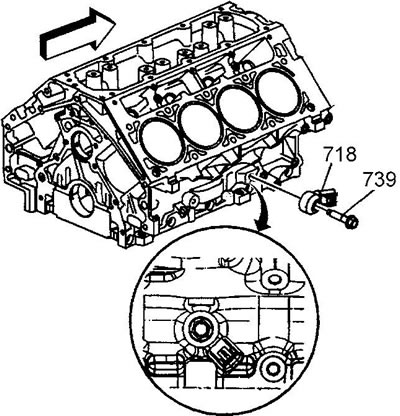
Tightening torque 20 Nm.
Installing the crankshaft
Attention:
- Main bearing clearances are critical. Excessive main bearing clearance can adversely affect the crankshaft position sensor signals and/or the operation of the OBDII system.
- The crankshaft main bearing caps must be in place and correctly oriented.
- When installing the main bearing shells, align the bearing retainer with the cutout in the block and cap.
- Always install earbuds in pairs, do not file the earbuds or mix earbuds of different pairs.
- Install new pinch bolts to prevent oil leakage (m8) main bearing caps. The new bolts are already sealed.
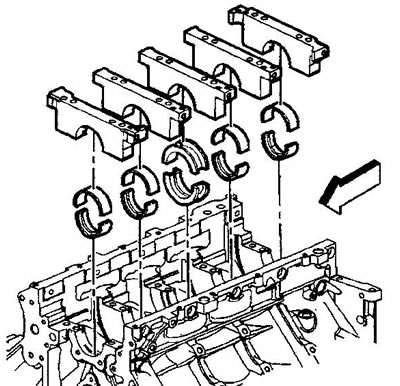
1. Install the main bearing shells in the cylinder block and bearing caps. The thrust bearing is mounted on the central neck of the shaft.
2. Lubricate the bearings and main journals of the crankshaft with clean engine oil.
3. Install the crankshaft.
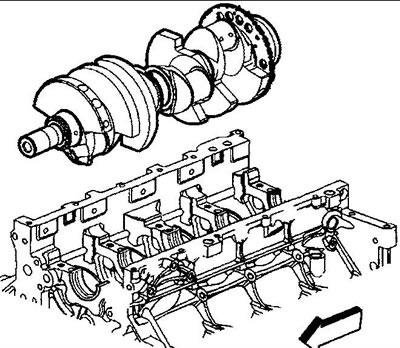
Note: install the crankshaft carefully, do not damage the thrust bearing.
4. Install the crankshaft main bearing caps, in place and in the correct direction.
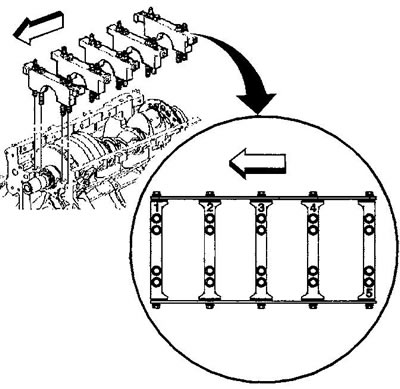
5. Install M10 bolts (129) And (128).
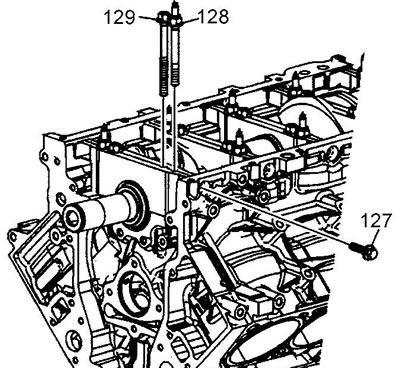
6. Use a plastic hammer to upset the main bearing caps.
7. Install NEW M8 tie bolts (127).
8. Tighten the M10 bolts (1-10) fastening the bearing caps with the first pass in the order shown in the figure.

Tightening torque 20 Nm.
9. Using a plastic mallet, drive the crankshaft back and forth until it stops to properly install the thrust bearing.
- A) Tighten M10 bolts (1-10) finally. Tightening torque - Tighten 80°.
- b) Tighten M10 bolts (11-20) the first pass in the specified sequence. Tightening torque 20 Nm.
- V) Tighten M10 bolts (11-20) finally. Tightening torque - Tighten 51°.
- G) Tighten the M8 tie bolts. Tightening torque 25 Nm.
Compress the bolt on 1 side of the bearing cap and then tighten the bolt on the opposite side of the same bearing cap.
10. Install the crankshaft position sensor.
- A) Check the condition of the sealing ring (750) sensor. If the ring is OK, it can be reinstalled.
- b) Lubricate the O-ring with clean engine oil.
- V) Install the O-ring on the sensor.
- G) Install the sensor (701), rotate the sensor until the mounting hole of the sensor is aligned with the mounting bolt hole in the block.
- d) install bolt (702) sensor mounting, tighten the bolt. Tightening torque 25 Nm.
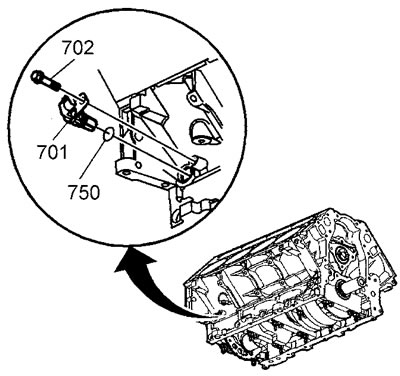
11. Measure the axial clearance of the crankshaft.
- A) Slide the crankshaft forward or backward until it stops.
- b) Insert a feeler gauge between the thrust bearing face and the crankshaft web and measure the bearing clearance. Axial clearance 0.04-0.2 mm.
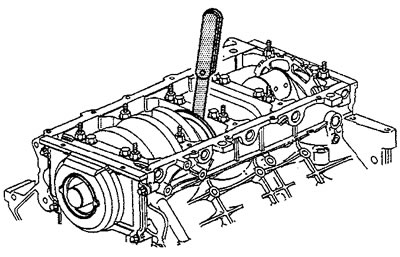
- V) If the clearance is out of range, check the condition of the surface of the crankshaft on which the thrust bearing runs.
Piston and connecting rod installation
1. Lubricate with clean engine oil:
- piston
- piston rings
- engine cylinder wall
- connecting rod bearing shells
2. Install the connecting rod bearing shells into the connecting rod and connecting rod cap.
3. Separate the locks of the scrapers of the oil scraper ring at least 25 mm apart.
4. Spread the locks of the compression rings 180 degrees apart.
5. Screw soft metal guides into the connecting rod.
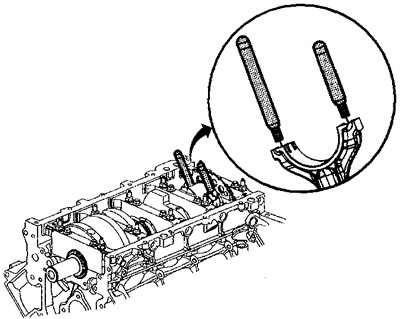
6. Check the correct assembly of the piston and connecting rod: label (1) on the piston head and lugs (2) on the connecting rod should be on one side.
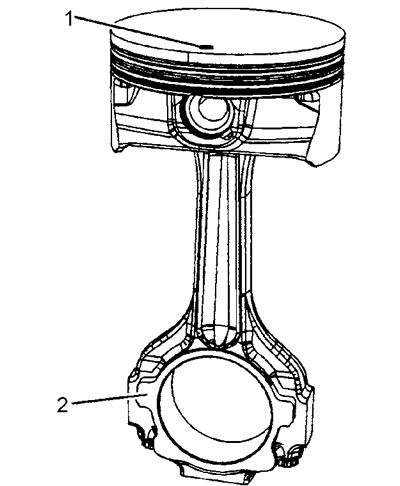
7. Using a swage, compress the piston rings.
8. Install the piston and connecting rod in the appropriate cylinder. The mark on the piston should be towards the front of the engine. Press the swage against the block and use the hammer handle to lightly tap the piston into the cylinder.
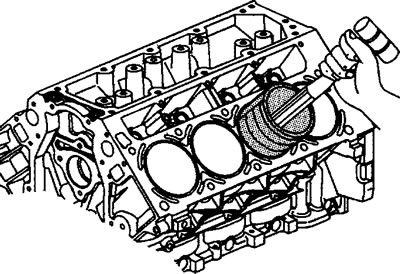
9. Turn out directing a rod.
10. Install the connecting rod cap (103) along with insert (104), tighten the bolts (102) cover fastening. Tightening torque: 1st pass 25 Nm; Tighten the 2nd pass by 70°.
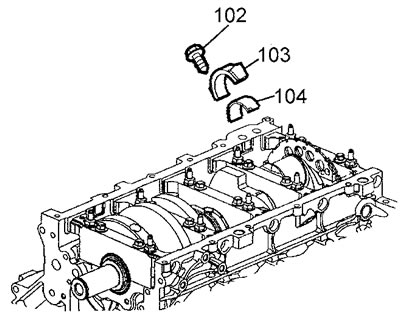
11. Measure the side clearance of the connecting rod, compare with given specifications.
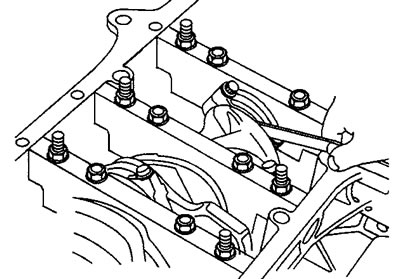
Further Assembly
Further assembly of the engine is carried out in the reverse order of disassembly.