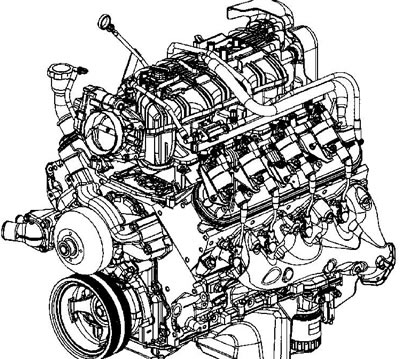
General view of the engine
Crankcase ventilation system The crankcase ventilation system is closed. Fresh air from the throttle body enters the crankcase, where it mixes with crankcase gases and then enters the intake manifold through the crankcase ventilation valve. The consumption of crankcase gases depends on the vacuum in the intake manifold and is maintained at the desired level by the valve of the ventilation system.
Attachment drive system
The system includes:
- drive belt and belt tensioner
- parasitic pulley
- crankshaft pulley
- attachment brackets
- mounted units:
- power steering pump (if driven by belt) - generator
- air conditioning compressor (
- radiator fan (if driven by belt)
- coolant pump
- Vacuum pump
- air compressor.
The system can have 1 or 2 V-ribbed belts. Both sides of the belt can be used for drive. Belt tension is maintained automatically by a spring tensioner. A parasitic pulley is installed to provide the required angle of wrapping the belt around the pulleys. Some systems use a parasitic pulley instead of an attachment that is not installed on this vehicle model.
Camshaft
The steel camshaft is mounted on five sleeve bearings pressed into the engine block. The camshaft is driven from the crankshaft by a chain. On LC9 / LY5 / LMG engines, the shaft drive is direct, on LY6 / L76 / L92 engines - through a variable valve timing drive. The timing ring of the camshaft position sensor is installed on the front side of the camshaft sprocket, the sensor itself is installed on the front cover of the engine. The camshaft is protected from axial movement by a lock.
Crankshaft
The crankshaft is cast from ductile iron. The crankshaft is mounted on five main bearings. The crankshaft journals are cut and knurled with a roller for hardening. A thrust bearing is installed in the central main bearing. A timing ring for the crankshaft position sensor is pressed onto the rear flange of the crankshaft. It is not serviced separately.
Cylinder head
The cylinder heads are cast aluminum and carry pressed-in guide bushings and valve seats made by powder metallurgy. In the front part of the heads there are air discharge channels from the cooling system. Valve covers are attached with 4 bolts.
Cylinder block
On LC9/L76/L92 engines, the block is cast aluminum, on LY5/LMG and LY6 engines it is cast iron. The block is made according to the V-shaped scheme with a camber angle of 90 degrees. The main bearing caps are attached with four vertical bolts and two pinch bolts. Engine blocks with and without cylinder deactivation are different.
Exhaust manifolds
The exhaust manifolds are cast iron. A heat shield is attached to each exhaust manifold.
Intake manifold
The intake manifold is common to both half-blocks of the engine. Brass inserts are screwed into the manifold for fastening the fuel manifold, throttle body and wire bundle support. The intake manifold is sealed along the semi-blocks with a special disposable gasket. The intake manifold does not have a cooling jacket.
Oil pan
The oil pan is cast aluminum. The oil sump carries the oil filter, damper screen and oil level sensor. On models of the early years of production, a channel was made in the pan for installing an oil filter bypass valve. Also installed in the sump is a pressure reducing valve for the oil pressure of the fuel control system. It is very important to correctly install the pallet at the junction of the rear of the block and the automatic transmission housing.
Piston and connecting rod
The pistons are cast aluminum and have two compression rings and one oil scraper ring. The piston head can be flat or displaced. Installation of a finger in the piston and connecting rod is carried out with a gap. Pistons of engines of all models have a graphite coated skirt. The piston and pin are replaced in pairs only.
Valve lid
The valve covers are cast aluminium. The covers carry the ignition coils. A valve of the crankcase ventilation system is installed in the cover of the left semi-block, in the cover of the right semi-block there is an oil filler neck and an air supply channel for the crankcase ventilation system.
Valve drive
Valves from the camshaft are driven through hydraulic tappets, rods and rocker arms. There is no clearance in the valve drive On some engine models, to improve fuel efficiency in some operating modes, cylinders 1, 4, 6 and 7 can be turned off, (even cylinders are in the right half-block, odd cylinders are in the left half-block).
Cylinder deactivation system
General Motors' active fuel management system can shut down four of the eight cylinders, converting the engine from a V8 to a V4 when the engine is lightly loaded to improve fuel efficiency.
Oil collector of hydraulic tappets of the cylinder deactivation system
Oil manifold (1) The hydraulic tappets are bolted to the top of the engine block under the intake manifold. Four normally closed solenoid valves are installed in the manifold (2). Each solenoid valve directs engine oil to the pushrods (5) inlet and outlet valve. The oil pressure in the system is regulated by a pressure reducing valve (6), which is installed in the oil pan.
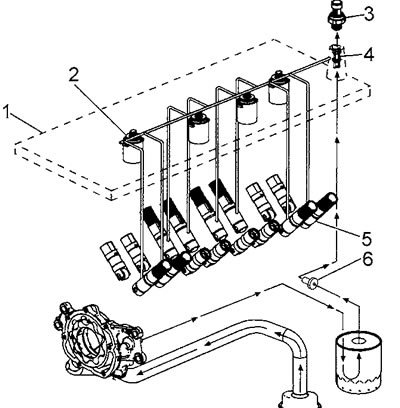
Oil collector of hydraulic tappets of the cylinder deactivation system
When the prerequisites for deactivating the cylinders arise, the electronic control unit begins to activate the solenoid valves in the order of the cylinders. When the solenoid valves are activated, the engine oil through eight vertical channels (two per cylinder) from the oil manifold is fed into the tappet gallery in the engine block and the engine goes into the V4 circuit, see below. When operating conditions call for a return to the V8 circuit, the ECM deactivates the solenoid valves and bleeds oil from the pushrod cavity to the oil manifold.
Several channels are made in the oil collector housing to release air that has entered the system.
A replaceable oil filter is installed at the oil manifold inlet to prevent dirt from entering the hydraulic valve control system (4). An oil pressure sensor is installed behind the filter (3), the signal of which is processed by the engine control unit.
Cylinder shut-off pushers
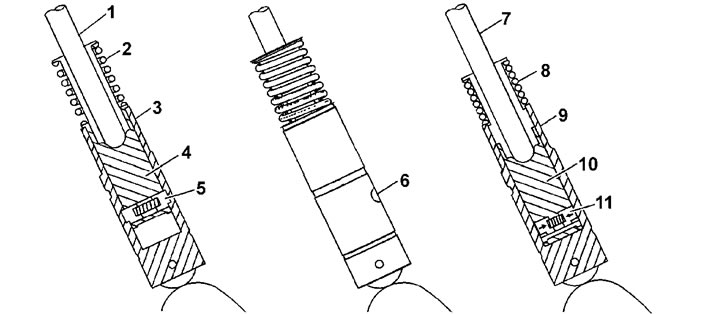
Cylinder shut-off pushers
When the engine is running according to the V8 scheme, the operation of the pushers of the cylinder deactivation system is no different from the operation of conventional pushers. Here, the oil manifold solenoid valves are closed and oil pressure is not transmitted to the pusher cavity. Barbell (1) The pushrod moves up and down and drives the cylinder valves through the rocker. Force loaded locking pins (5) protrude from the inner body of the pusher and mechanically connect the inner body of the pusher (4) with outer casing (3).
When the engine control unit decides to turn off the cylinders, the solenoid valves direct oil from the oil manifold to the inlet (6) pusher. The oil pressure overcomes the spring force of the locking pins, pushing the pins in (11) into the housing and breaking the mechanical connection of both pusher housings. The engine goes to work according to the V4 scheme. now barbell (7) remains stationary, and the outer casing (9) moves up and down regardless of the movement of the inner case (10). Spring (8) maintains contact in the actuator, eliminating valve actuator noise.
When the control unit puts the engine into V8 mode, the pressure at the inlet to the pushrod is released, the locking pin spring restores the mechanical connection in the pushrod.
Variable valve timing actuator and solenoid valve
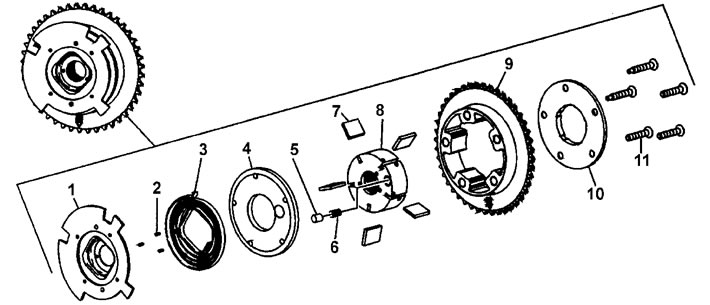
Variable valve timing drive. 1 - camshaft position sensor timing ring, 2 - pin, 3 - return spring, 4 - front cover, 5 - detent pin, 6 - detent spring, 7 - vanes, 8 - rotor, 9 - stator, 10 - rear cover, 11 - bolt
The camshaft of engines with variable valve timing has a channel for supplying oil to the drive.
Oil for the drive from the engine lubrication system is supplied from the neck of the 2nd bearing.
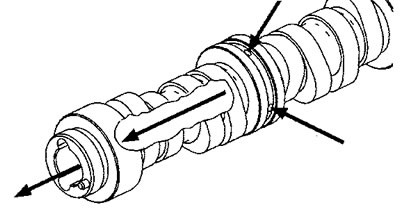
The solenoid valve for the phase change drive consists of a body, a spool valve (1), return spring (2), oil filter (3), check valve springs (4) and check valve ball (5).
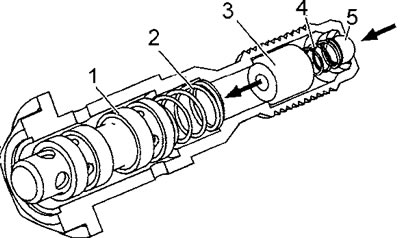
The position of the spool valve is determined by the system magnet and the engine control unit.
When the spool valve moves to a certain position, oil flows through the valve to the phase change actuator. The solenoid valve must be replaced every time it is removed. drive magnet (752) located in the front cover of the engine and sealed with a gasket (753).
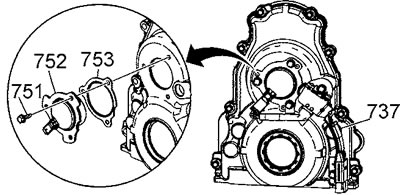
The actuator magnet is controlled by the engine control unit via a modulated 12-volt signal. When the magnet is activated, the actuator solenoid valve spool valve moves.
The variable phase drive is a vane-type hydraulic motor that changes the angular position of the camshaft relative to the position of the crankshaft.
The lift and the duration of the opening of the valves remain unchanged. The phase change drive is serviced only as an assembly.