Device Features
The main dimensions of valves, valve guides and valve seats are given in fig. 2-45.
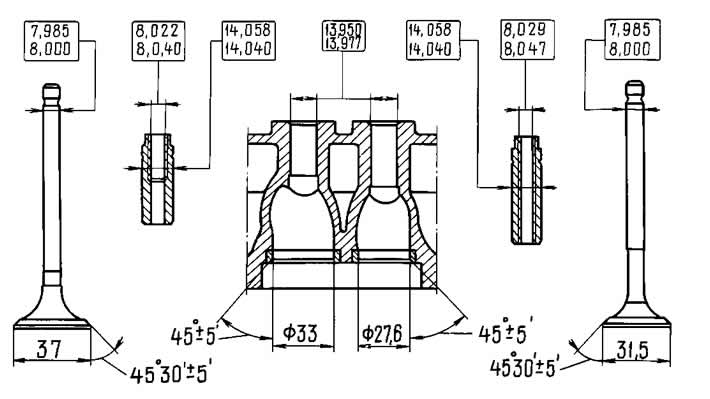
Pic. 2-45. Main dimensions of valves, valve guides and valve seats.
The cylinder head is cast from aluminum alloy, has pressed cast iron seats and valve guides. The upper part of the bushings is sealed with rubber-metal oil seals.
As spare parts, guide bushings are supplied with an outer diameter increased by 0.2 mm.
A bearing housing is fixed to the cylinder head, in which the camshaft is located.
Valve drive mechanism
Valves 2 (pic. 2-46) are actuated by camshaft cams through levers 3. At one end, the lever presses on the valve, and at the other end it rests on the spherical head of the hydraulic support 6. The hydraulic supports automatically eliminate the clearance in the valve mechanism and therefore, during vehicle maintenance, it is not required to check and adjust the clearance in the valve mechanism.

Pic. 2-46. Valve drive mechanism:
1 - cylinder head;
2 - valve;
3 - valve lever;
4 - oil ramp;
5 - camshaft;
6 - hydraulic pusher support;
7 - nut;
8 - hydrosupport bushing;
9 - spacer.
Chain tensioner
Oil from the lubrication system through pipe 3 (see fig. 2-12) enters the cavity «E» (pic. 2-47) tensioner, then through the hole «D» and valve assembly 2 enters the working cavity «IN» and presses on the plunger 5. In the body 1 of the tensioner there is a hole with a diameter of 1 mm to bleed air from the cavity «E».
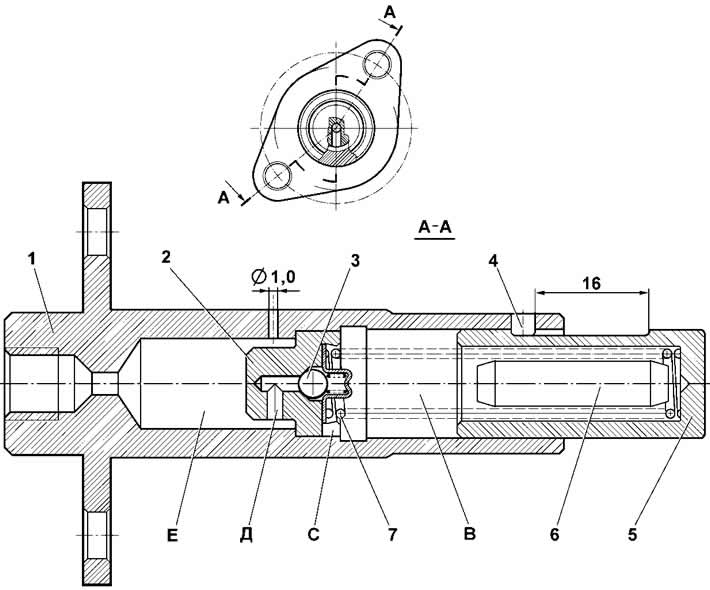
Pic. 2-47. Hydraulic chain tensioner:
1 - tensioner housing;
2 - valve assembly;
3 - check valve ball;
4 - restrictive pin;
5 - tensioner plunger;
6 - volume limiter;
7 - plunger spring;
B - working cavity;
C - installation groove;
D - hole;
E - reserve cavity.
The diametral gap between body 1 and plunger 2 should be 0.018-0.024 mm and is measured as the difference between the maximum measured diameter of plunger 2 and the minimum measured diameter of body 1.
When repairing, the tensioner housing and the plunger form a pair, in which the replacement of one part with another after the selection of the gap is not allowed. Plunger 2 must move without jamming in body 1 by a stroke equal to 16 mm.
When installing on the engine, the tensioner must be free of oil, pin 4 must not protrude from the housing.
Removal and installation of a head of cylinders on the car
The cylinder head is removed from the engine on the vehicle unless the entire engine needs to be disassembled to fix the problem. For example, if it is necessary to remove carbon deposits from the surface of combustion chambers and valves or to replace valves or valve guides.
Remove the cylinder head in the following order:
- put the car on a lift and release the pressure in the fuel supply system. To do this, disconnect the fuel pump wiring harness connector from the ignition system wiring harness, start the engine, let it run until it stops;
- disconnect the wire from the terminal «minus» battery;
- raise the car and drain the coolant from the radiator and cylinder block, following the recommendations outlined in subsection «Removal and installation of the engine»;
- disconnect the muffler intake pipe from the exhaust manifold, remove the coolant pump inlet pipe bracket;
- lower the car, disconnect the hose (see fig. 2-4) fuel supply from the fuel pipe. Plug the openings of the hose and tube so that dirt does not get into them;
- disconnect cable 2 (see fig. 2-5) accelerator drive from the throttle pipe and from bracket 4 on the receiver;
- remove the crankcase exhaust ventilation hoses by disconnecting them from the pipes on the cylinder head cover, from the intake pipe hose and from the throttle pipe;
- loosen the clamps and disconnect the hose 1 from the throttle pipe (see fig. 2-6) intake pipe, adsorber purge hose, coolant inlet and outlet hoses;
- disconnect from the receiver the vacuum selection hose to the vacuum brake booster;
- disconnect the wires from the spark plugs, from the sensors of the oil pressure indicator lamp and the coolant temperature gauge, from the throttle pipe; disconnect the wires from the injector wiring harness;
- disconnect the hoses from the outlet pipe of the engine cooling jacket;
- remove the cylinder head cover with gasket, engine screen brackets and accelerator cable;
- turn the crankshaft until the mark on the camshaft sprocket aligns with the mark on the bearing housing (see fig. 2-26);
- unscrew the camshaft sprocket mounting bolt, unscrew the fitting, nuts and remove the chain tensioner, remove the camshaft sprocket;
- unscrew the bolts securing the cylinder head to the block and remove the cylinder head with gasket.
Establish a head of cylinders in an order, the return to removal, observing the recommendations stated in subsection «Engine assembly». The gasket between the head and the cylinder block cannot be reused, so replace it with a new one.
After installing the cylinder head, adjust the accelerator drive.
Check the operation of the engine management system.
Dismantling and assembly of a head of cylinders
Disassembly. If only one part needs to be replaced, the cylinder head may not be completely disassembled and only what is needed for replacement can be removed.
Place the cylinder head on a stand, remove the nuts and remove the intake pipe, exhaust manifold and intake manifold screen. Remove the outlet pipe of the cooling jacket and the fluid outlet pipe to the heater. Remove spark plugs and coolant temperature sensor.
Turn away nuts of fastening and remove the case of bearings in gathering with a camshaft. Loosen the nuts securing the thrust flange to the bearing housing. Remove the flange and remove the camshaft from the bearing housing.
Remove levers 3 (see fig. 2-46) valves.
Unscrew the hydraulic bearings 6 (see fig. 2-46a) and remove the oil rail 4.
On engines equipped with hydraulic bearings f. INA, remove hydraulic bearings 6 (see fig. 2-46b), unscrew bushings 8 of hydraulic bearings, remove oil rail 4 with spacers 8 as an assembly.
Install the cylinder head to tool 67.7823-9567, compress the valve springs and loosen the cotters.
Remove valve springs with plates and support washers. Turn the cylinder head and remove the valves from the underside. Remove the oil seals from the guide bushings.
Assembly. Assemble the cylinder head in the reverse order of disassembly. Lubricate valves and oil seals with engine oil before assembly.
Before installing the camshaft bearing housing, check that the locating sleeves are in place (see fig. 2-25). Tighten nuts of fastening of the case of bearings in the order specified in fig. 2-27. At the same time, pay attention to the fact that the adjusting sleeves fit into the sockets of the bearing housing without distortion.
Before installing the hydraulic bearings from spare parts, place each hydraulic bearing in a container with engine oil until it is completely immersed in oil and apply several pressures with your hands until the free play of the plunger is removed.
Checking the technical condition and repair
Cylinder head. Wash the cylinder head thoroughly and clean the oil passages. Remove carbon deposits from the combustion chambers and from the surface of the exhaust channels with a wire brush.
Inspect the cylinder head. Cracks in any places of the cylinder head are not allowed. If you suspect that coolant has entered the oil, check the tightness of the cylinder head.
To check the tightness, close the holes of the cooling jacket of the cylinder head with the plugs included in the tool kit A.60334 (pic. 2-48). Supply compressed air inside the head at a pressure of 0.15-0.2 MPa (1.5-2 kgf/cm). Within 1-1.5 minutes, no air bubbles should be observed from the head.
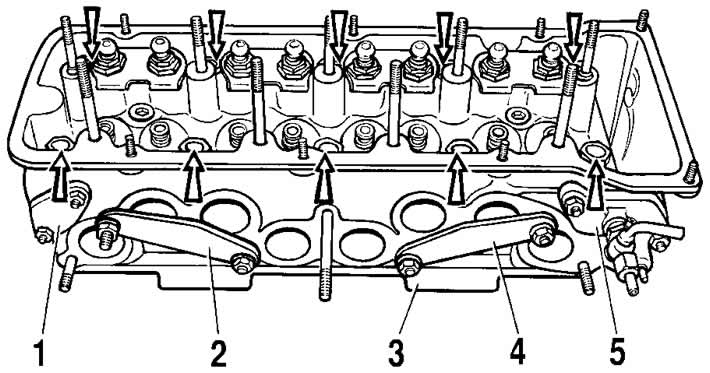
Pic. 2-48. Checking the tightness of the cylinder head using tool A.60334:
1, 2, 4 - plugs;
3 - fixture plate;
5 - flange with air supply fitting.
Valve seats. The shape of the chamfers of the valve seats is shown in fig. 2-49 and 2-50. On the working chamfers of saddles (valve contact area) there should be no pitting, corrosion or damage. Minor damage can be repaired by grinding the seats, removing as little metal as possible. You can grind both manually and with a grinder.
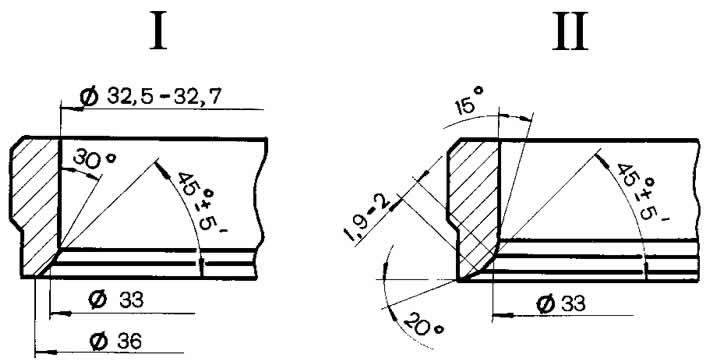
Pic. 2-49. Inlet valve seat profile:
I - new seat;
II - seat after repair.
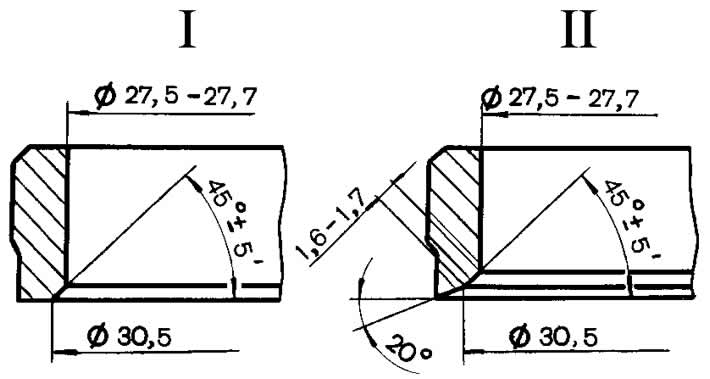
Pic. 2-50. Exhaust valve seat profile:
I - new seat;
II - seat after repair
To grind the seats, install the cylinder head on a stand, insert the rod A.94059 into the valve guide bushing and clean the chamfers of the seats from carbon deposits with A.94031 and A.94092 drills for exhaust valve seats and A.94003 and A.94101 drills for intake valve seats. Countersinks are put on the spindle A.94058 and centered by the guide rod A.94059. These rods are available in two different diameters: A.94059/1 for intake valve guides and A.94059/2 for exhaust valve guides.
Put on the guide rod A.94059 spring A.94069/5, install on the spindle A.94069 conical circle A.94078 for exhaust valve seats or circle A.94100 for inlet valve seats, fix the spindle in a grinder and grind the valve seat (pic. 2-51).
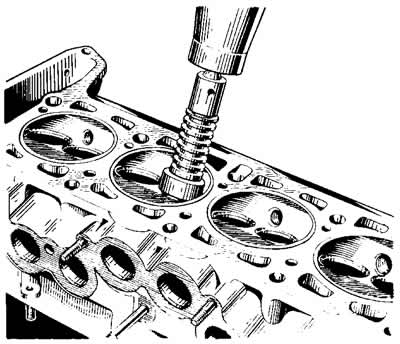
Pic. 2-51. Grinding of the working chamfer of the valve seat.
At the moment the wheel touches the seat, the machine must be turned off, otherwise vibration will occur and the chamfer will be incorrect. It is recommended to dress the wheel more often with a diamond.
For exhaust valve seats, bring the width of the working chamfer to the values \u200b\u200bspecified in fig. 2-51, countersink A.94031 (angle 20°), and countersink A.94092, which eliminates hardening on the inner diameter. Countersinks are put on the spindle A.94058 and, as in the case of grinding, are centered with the rod A.94059.
At the inlet valve seats, bring the width of the working chamfer to the values \u200b\u200bspecified in fig. 2-52, first processing the internal chamfer with a countersink A.94003 (pic. 2-52) until a diameter of 33 mm is obtained, and then a chamfer of 20°with a countersink A.94101 until a working chamfer with a width of 1.9-2 mm is obtained.

Pic. 2-52. Narrowing of the working chamfer of the valve seat with a countersink mounted on the spindle А.94058.
Valves. Remove carbon deposits from valves. Check if the rod is deformed and if there are cracks on the plate. Replace damaged valve.
Check the condition of the valve face. In case of minor damage, it can be sanded, maintaining a chamfer angle of 45°30'±5'. In this case, the distances from the lower plane of the valve disc to the base diameters (36 and 30.5 mm) should be within the limits shown in Fig. 2-53.
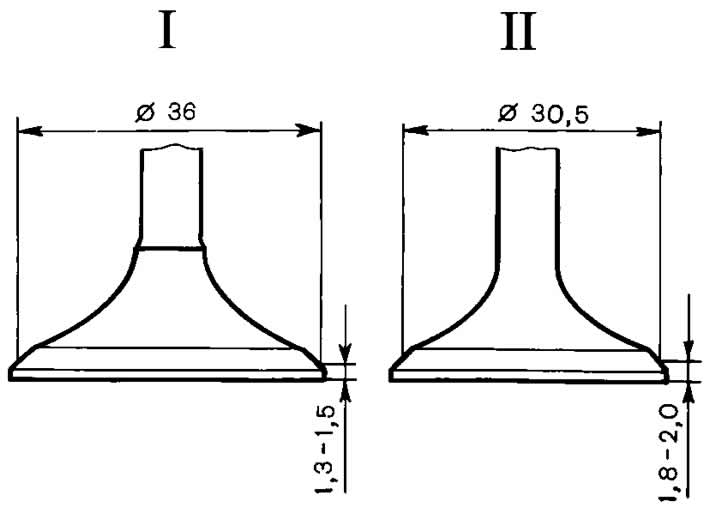
Pic. 2-53. Maximum dimensions when grinding chamfers of valves:
I - inlet valve;
II - exhaust valve.
Valve guides. Check the clearance between the valve guides and the valve stem by measuring the diameter of the valve stem and the bore of the valve guide.
Estimated clearance for new bushings: 0.022-0.055 mm for intake valves and 0.029-0.062 mm for exhaust valves; maximum allowable clearance (when worn) - 0.3 mm, provided there is no increased noise of the gas distribution mechanism.
If the increased clearance between the guide sleeve and the valve cannot be eliminated by replacing the valve, then replace the valve sleeves using the A.60153/R tool for pressing and pressing in (pic. 2-54).
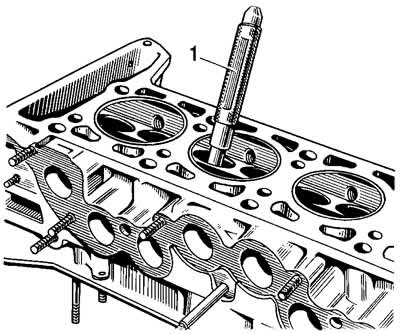
Pic. 2-54. Pressing out guide bushings:
1 - mandrel A.60153/R.
Press in the guide bushings with the retaining ring on until it stops against the body of the cylinder head.
After pressing, expand the holes in the guide bushings with A.90310/1 reamers (for intake valve bushings) and A.90310/2 (for exhaust valve bushings).
When repairing the engine, always replace the oil deflector caps with new ones.
Replace damaged oil seals with the cylinder head removed. To press the caps, use the mandrel 41.7853.4016.
Springs. Make sure that the springs are not cracked and their elasticity has not decreased, for which check their deformation under load (pic. 2-55).
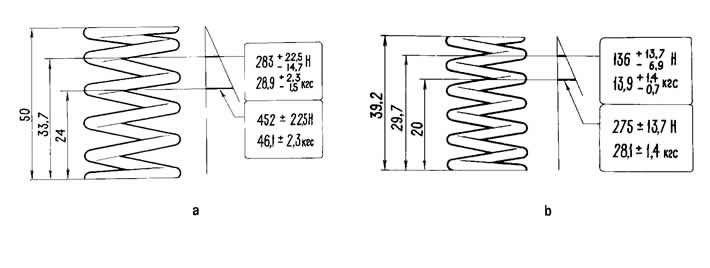
Pic. 2-55. Basic data for checking the outer (A) and internal (b) valve springs.
Bolts of fastening of a head of cylinders. With repeated use of the bolts, they are pulled out. Therefore, check whether the length of the bolt shaft exceeds (head length not included) 117 mm and, if it is more, then replace the bolt with a new one.
Hydrosupports. Check the condition of the hydraulic bearings. The plunger of the hydraulic support installed in the cylinder head should not move when they are sharply pressed by hand. If the plunger moves freely, replace the hydraulic support.
Valve levers. Check the condition of the working surfaces of the lever mating with the valve stem, with the camshaft cam and with the spherical end of the hydraulic bearing plunger. If nicks or marks appear on these surfaces, replace the lever with a new one.