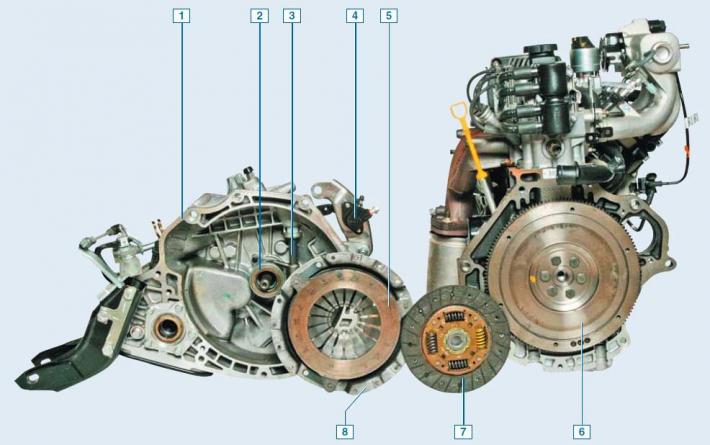
Clutch elements: 1 - gearbox housing; 2 - clutch release bearing; 3 - clutch release shaft; 4 - working cylinder; 5 - pressure plate; 6 - flywheel; 7 - driven disk; 8 - clutch cover (basket)
The clutch is single-disk, dry, with a central spring of the diaphragm type.
It is located in an aluminum crankcase structurally integrated with the gearbox and attached to the engine block.
The clutch cover is connected to the engine flywheel with six bolts.
By three pairs of elastic steel plates, the casing is connected to the pressure (leading) disk.
This node (it is also called the "basket" of the clutch) the assembly is balanced on the stand, so it is replaced entirely.
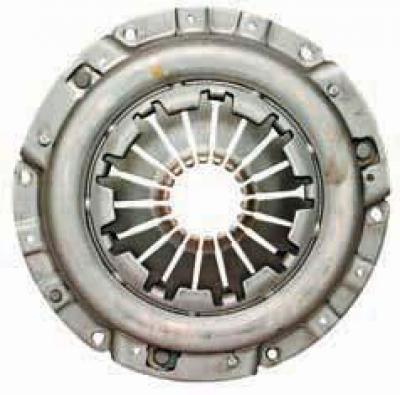
casing (basket) clutch
A diaphragm spring is installed in the casing.
Replacing the "basket" is necessary when the annular wear of the pressure spring petals, and if the ends of the petals are not at the same level.
We reject the "basket" also when the force on the pedals decreases during the clutch disengagement, which indicates a large wear on the surface of the pressure plate or "draft" of the spring.
The driven disk with a spring damper of torsional vibrations is located on the splines of the input shaft of the gearbox between the flywheel and the pressure plate.
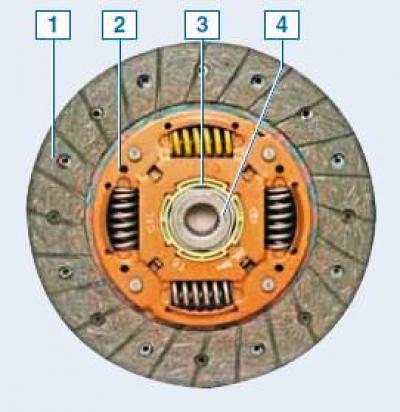
Driven clutch disc: 1 - friction linings; 2 - torsional vibration damper; 3 - idle damper; 4 - hub
Two disc friction linings are riveted on both sides to a spring plate, which, in turn, is riveted to one of the two damper plates.
The spring plate has a wavy shape.
When the clutch is engaged, the friction linings compress the spring plate, which contributes to a smoother engagement of the clutch.
A disk hub is installed between the damper plates.
Damper springs are installed in the grooves of the hub and damper plates.
The damper plates are connected by bearing pins.
In the disc hub, opposite the support pins, there are cutouts that allow the hub to rotate within certain limits relative to the damper plates, while compressing the damper springs.
This allows you to reduce dynamic loads in the transmission when starting the car and when shifting gears.
An idle damper is located on the hub of the driven disk in a plastic housing, which serves to dampen torsional vibrations and eliminate knocks in the gearbox at idle speed of the engine.
The driven disk is replaced when the axial runout of the linings is more than 0.5 mm, oiling, cracking, scuffing or uneven wear of the linings, weakening of the rivet joints, and also if the distance between the working surface of the lining and the head of the rivet is less than 0.2 mm.
The clutch release drive is hydraulic.
The force in it from the pedal to the clutch release fork is transmitted through the working fluid.
The reservoir of the hydraulic drive of the clutch is common with the reservoir of the hydraulic drive of the brake system.
The clutch release shaft with a lever welded to it rotates on bushings installed in the clutch housing.
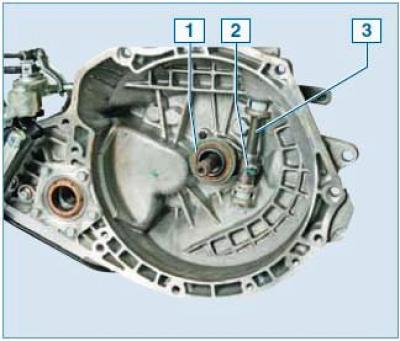
Elements of the clutch release drive mechanism: 1 - clutch release bearing; 2 - clutch release fork; 3 - clutch release shaft
The clutch release fork is bolted to the shaft.
A clutch release bearing is installed between the clutch release fork and the diaphragm spring petals.
The bearing moves freely along the guide sleeve, which is attached to the clutch housing with three bolts.
The spring in the working cylinder through the pusher, lever and clutch release fork constantly presses the bearing against the casing diaphragm spring.
The clutch pedal is mounted on the axis of the pedal assembly bracket.
The pedal is connected to the clutch master cylinder piston pusher.
The free travel of the clutch pedal is adjusted by rotating the push rod of the clutch master cylinder.
Clutch disengagement occurs as follows.
When the clutch pedal is pressed in the hydraulic system of the clutch release drive, pressure of the working fluid is created, as a result of which the piston of the working cylinder, moving together with the pusher, presses on the lever of the clutch release shaft, which rotates together with the clutch release fork and moves the bearing along the guide sleeve.
The bearing presses on the petals of the diaphragm spring.
The spring, deforming, ceases to press the pressure plate against the flywheel, while the pressure plate moves away from the flywheel, as a result of which the engine crankshaft and the gearbox input shaft can rotate independently of each other.
When the clutch pedal is released, the bearing returns to its original position, while the diaphragm spring again begins to press on the pressure plate, which, in turn, presses the driven disc against the flywheel - as a result, the transmission of torque resumes.
The clutch release bearing contains a "lifetime" supply of grease and is therefore maintenance free.
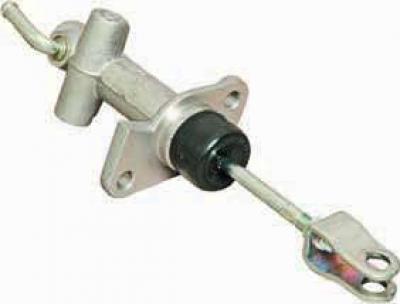
Clutch Master Cylinder
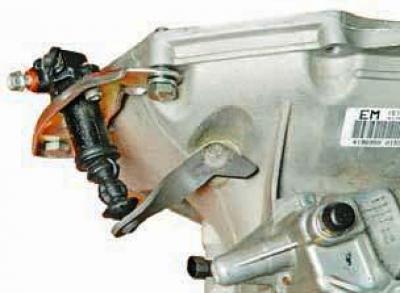
Clutch release slave cylinder