Design description
On-board network - direct current, with a nominal voltage of 12 V.
The electrical equipment is made according to a single-wire circuit: the negative terminals of the sources and consumers of electricity are connected to the "ground" - the body and the power unit of the car, which act as a second wire.
When the engine is off, the switched on consumers are powered by the battery, and after the engine is started, from the generator.
When the generator is running, the battery is charged.
The vehicle is equipped with a maintenance-free lead-acid starter battery 6ST-55A1.
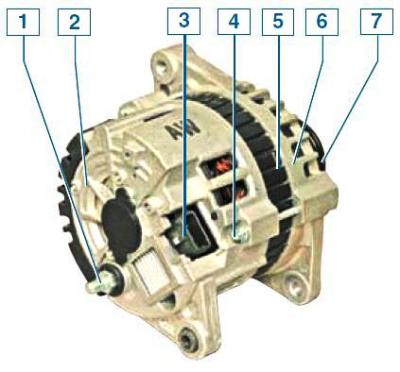
Generator: 1 - output "BAT"; 2 – back cover; 3 - connector; 4 - coupling screw; 5 - stator; 6 - front cover; 7 - pulley
The generator is a synchronous alternating current electric machine with a built-in rectifier unit and voltage regulator.
The alternator pulley is driven by a V-ribbed belt from the accessory drive pulley.
The stator and generator covers are tightened with three screws.
The rotor shaft rotates in ball bearings installed in the generator covers.
Sealed bearings, lubricated in them, designed for the entire service life of the generator.
The rear bearing is pressed onto the rotor shaft, and is installed in the cover with a small gap.
The front bearing is pressed into the front cover, and the bearing has a sliding fit on the rotor shaft.
In the stator of the generator there is a three-phase winding, made according to the "triangle" scheme.
The ends of the phase windings are soldered to the terminals of the rectifier unit, which consists of six silicon diodes (valves) - three "positive" and three "negative", pressed into two horseshoe-shaped aluminum plates-holders in accordance with the polarity (positive and negative on different plates).
On one of the plates there are also three additional diodes through which the excitation winding of the generator is fed after the engine is started.
The rectifier unit is fixed on the rear cover of the generator.
The excitation winding is located on the generator rotor, and its leads are soldered to two copper slip rings on the rotor shaft.
Power is supplied to the excitation winding through two brushes that are installed in the brush holder.
The brush holder and voltage regulator are mounted on the rear cover of the generator.
The voltage regulator is a non-separable unit; if it fails, it is replaced.
When the ignition is turned on, voltage is supplied to the excitation winding of the generator, and the battery charge indicator in the instrument cluster lights up.
After starting the engine, the field winding is powered by additional diodes of the rectifier unit (signaling device goes out).
If, after starting the engine, the warning light is on, this indicates a malfunction of the generator or its circuits.
The "minus" of the battery should always be connected to the "mass" of the car, and the "plus" - to the "BAT" terminal of the generator.
Reverse connection will lead to a breakdown of the generator diodes.
When the generator is running, the battery should not be disconnected, as the resulting voltage surges can damage the electronic components of the circuit.
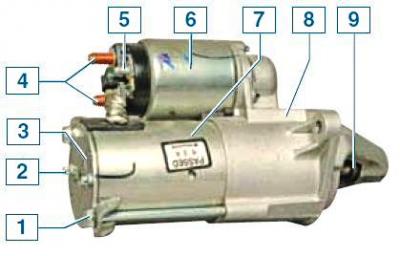
Starter: 1 - coupling bolt; 2 - screw for fastening the brush holder; 3 – back cover; 4 - contact bolts; 5 - control output of the traction relay; 6 - traction relay; 7 - body; 8 - front cover; 9 - drive shaft
The starter is a four-brush DC electric motor with permanent magnet excitation, with a planetary gear, a freewheel roller clutch and a two-winding traction relay.
Permanent magnets are attached to the steel body of the starter.
The body and covers of the starter are tightened with two bolts.
The armature shaft rotates in plain bearings.
The torque from the armature shaft is transmitted to the drive shaft through a planetary gearbox, consisting of a central and crown (with internal gear) gears and three satellites on the carrier (drive shaft).
Freewheel mounted on the drive shaft (overrunning clutch) with drive gear.
The traction relay is used to engage the drive gear with the ring gear of the flywheel of the crankshaft of the engine and turn on the power to the starter motor.
When the ignition key is turned to the "START" position, voltage is applied to both windings of the traction relay (pulling and holding).
The relay armature retracts and moves the drive lever, which moves the freewheel with the drive gear along the splines of the drive shaft, engaging the gear with the flywheel crown.
In this case, the retracting winding is turned off and the contacts of the traction relay are closed, including the starter motor.
After the key is returned to the "ON" position, the holding winding of the traction relay is de-energized, and the relay armature returns to its original position under the action of the spring - the relay contacts open and the drive gear disengages from the flywheel.
The defective traction relay is replaced.
A starter drive malfunction is detected during inspection after disassembling the starter.
The lighting and alarm system includes two headlights; fog lights; side direction indicators; rear lights; license plate lights; additional brake signal; ceiling lamps for interior and luggage compartment lighting; sound signal.
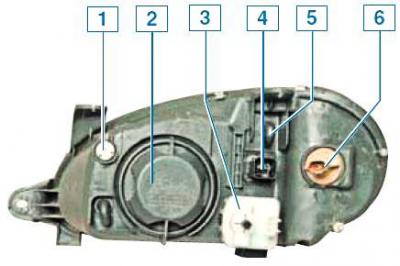
Block headlight: 1 - screw for adjusting the headlight beam in the horizontal plane; 2 — a cover of lamps of a far/dipped and dimensional light; 3 - motor-reducer of the headlight beam direction regulator; 4 - electrical connector; 5 - ventilation valve; 6 - turn signal lamp socket
The headlight unit is equipped with: a double-filament halogen high / low beam lamp, a side light lamp, a direction indicator lamp (orange color) and executive mechanism (gear motor) headlight beam direction controller.
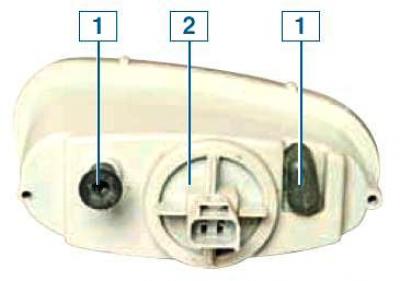
Anti-fog headlight: 1 - screw for adjusting the headlight beam; 2 - headlight lamp cover; 3 - ventilation valve
Fog lights are installed in the front bumper.
The fog lamp has a halogen lamp, the direction of the light beam of which is adjusted by a screw.
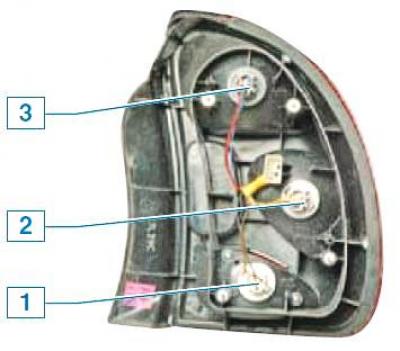
Location of lamps in the rear light: 1 - fog light; 2 - direction indicator; 3 - brake signal and side light
Lamps are installed in the rear lamp: brake signal and side light; direction indicator; fog light (in the left headlight); reversing light (in the right lamp).
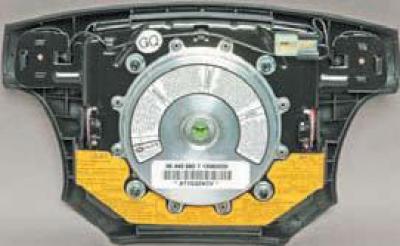
The car is equipped with a driver's airbag, which is located on the steering wheel.
The airbag control unit is located in the passenger compartment under the instrument panel console.
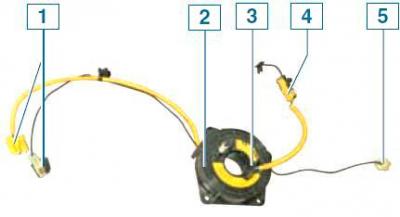
Drum unit with spiral cable: 1 - pads for connecting to the instrument panel wiring harness; 2 - body of the drum device; 3 - leash of the drum device; 4 — a block of wires of an airbag; 5 — block of wires of switches of a sound signal
For electrically connecting the airbag and horn switches to the instrument panel wiring harness instead of the conventional sliding contact (to avoid sparking and unintentional airbag deployment) a drum device with a spiral cable was used, operating on the principle of a tape measure.
The drum unit is attached to the steering column switch connector.
In the cylindrical plastic case of the device, several turns of a metal-plastic tape are spirally laid, which is an electrical conductor.
One end of the tape, through wires with pads, is connected to the instrument panel wiring harness.
The other end of the tape is brought out to the protruding leash of the drum and is connected by wires to the pads with the airbag and the horn switches.
The drum leash enters the hole in the steering wheel hub.
During rotation, the wheel by the leash turns the drum, and with it the tape, which is located in a cylindrical housing either on a larger or smaller radius.
From its middle position, the drum can rotate in each direction until it stops by 3.75 turns.
This prevents the tape from breaking when the steering wheel is rotated from neutral to full stop in each direction.
Before installing the steering wheel, it is necessary to set the drum of the device to the middle position, while the leash must be located on top.
Locks of all doors are blocked by electric drives.
Removal of electric door locks is shown in Ch. Body.
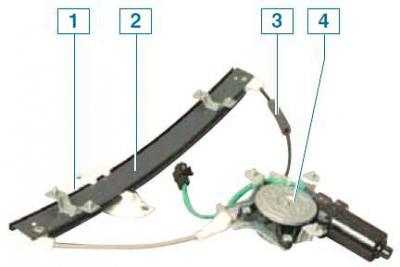
Power window: 1 - slider; 2 - guide; 3 - cable; 4 - motor reducer
Depending on the configuration, the car may be equipped with power windows in front of the doors.
Removal of power windows is shown in Sec. Body.
The power window motor-reducer consists of a worm gear and a reversible DC motor.
A drum with a cable is installed on the output shaft of the gearbox.
A slider is fixed on the cable, moving along the guide.
Glass holders are attached to the slider with two self-tapping screws.
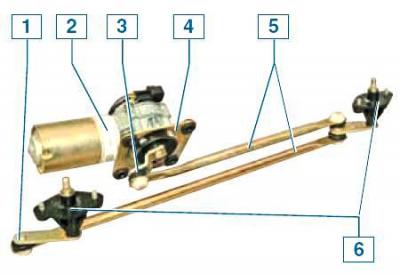
Windshield wiper: 1 - shaft lever; 2 - motor-reducer; 3 - crank; 4 - bracket; 5 - thrust; 6 - shaft support
The windshield wiper is installed under the windshield trim.
The cleaner motor-reducer is fixed in the engine compartment on the front panel.
The electric motor of the cleaner is three-brush, two-speed, with excitation from permanent magnets.
The windshield washer consists of a polyethylene tank with an electric pump, nozzles on the hood and connecting hoses.
The washer reservoir is located behind the left front fender.
The filler neck of the tank is displayed in the engine compartment.
Most electrical circuits are protected by fuses.
Powerful Consumers (rear window heating element, engine cooling fan, power windows and others) connected via a relay.
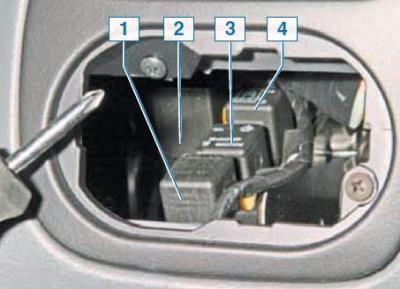
Relay location in the instrument panel: 1 - relay for turning on the fog light lamp in the left rear light; 2 - relay of the fourth speed of the electric motor of the heater fan; 3 - intermittent windshield wiper relay; 4 - relay direction indicators and alarms
The fuses and most of the relays are installed in two mounting blocks, one of which is located on the left, in the engine compartment, and the second is in the cabin, under the left side trim.
Four relays are installed in the instrument panel, behind the headlight beam direction control.
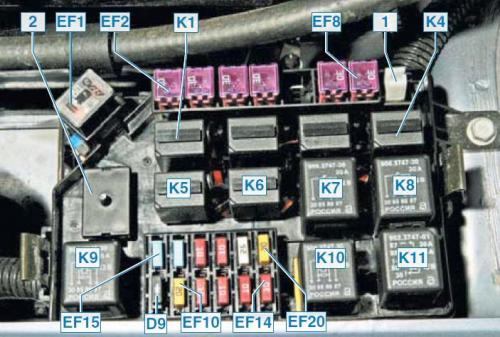
Mounting block fuses and relays in the engine compartment: EF1-EF20 - fuses; K1-K6 - small relay; K7-K11 - large relay; 1 - tweezers for extracting fuses and small relays; 2 - jumper block
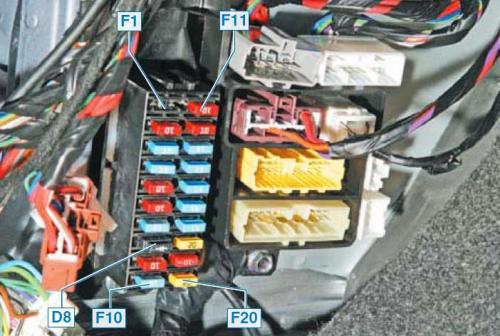
Mounting fuse block in the passenger compartment