The electrical circuit of the engine management system is given at the end of the book.
Warnings: Before removing any ECM components, disconnect the wire from the «minus» battery.
Do not start the engine if the cable lugs on the battery are loose.
Never disconnect the battery from the vehicle's electrical system while the engine is running.
When charging the battery, disconnect it from the car's on-board network.
Do not expose the electronic control unit (ECU) temperature above 65°C in working condition and above 80°C in non-working condition (e.g. in a drying chamber). If this temperature is exceeded, the ECU must be removed from the vehicle.
Do not disconnect or connect the wiring harness connectors to the ECU while the ignition is on.
Disconnect the wires from the battery and the wire connectors from the ECU before arc welding on the vehicle. Perform all voltage measurements with a digital voltmeter with an internal resistance of at least 10 MΩ.
The amount of fuel supplied by the injectors is regulated by an electrical pulse signal from the ECU It monitors the engine condition data, calculates the fuel demand and determines the required duration of fuel supply by the injectors (pulse duration - duty cycle). To increase the amount of fuel supplied, the ECU increases the pulse duration, and to reduce the fuel supply, it shortens
The ECU evaluates the results of its calculations and commands, remembers the modes of recent operation and acts in accordance with them. «self-learning» or adaptation of the ECU is a continuous process, but the corresponding settings are stored in the RAM of the electronic unit until the first power off of the ECU.
The ECU controls the fuel supply either synchronously, i.e. at a certain position of the crankshaft, or asynchronously, i.e. independently or without synchronization with the rotation of the crankshaft. Synchronous fuel injection is the most commonly used mode. Asynchronous fuel injection is used mainly in the engine start mode. The ECU turns on the injectors in series. Each of the nozzles is activated every 720°of crankshaft rotation. This method allows you to more accurately dose the fuel into the cylinders and reduce the level of toxicity of exhaust gases.
The amount of fuel supplied is determined by the state of the engine, i.e. its mode of operation. These modes are provided by the ECU and are described below.
When the crankshaft of the engine begins to scroll with the starter, the first pulse from the crankshaft position sensor causes a pulse from the ECU to turn on all the injectors at once, which allows you to accelerate the start of the engine.
Initial fuel injection occurs each time the engine is started. The duration of the injection pulse depends on the temperature. On a cold engine, the injection pulse increases to increase the amount of fuel; on a warm engine, the pulse duration decreases. After the initial injection, the ECU switches to the appropriate injector control mode.
Start mode. When the ignition is turned on, the ECU activates the fuel pump relay, which pressurizes the fuel supply line to the fuel rail.
The ECU checks the signal from the coolant temperature sensor and determines the amount of fuel and air required for starting.
When the engine crankshaft starts to crank, the ECU generates a phased pulse to turn on the injectors, the duration of which depends on the signals from the coolant temperature sensor. On a cold engine, the pulse duration is longer (to increase the amount of fuel supplied), and on warm - less.
Acceleration rich mode
The ECU monitors sudden changes in throttle position (throttle position sensor signal), as well as behind the signal of the absolute pressure sensor and provides the supply of additional fuel by increasing the duration of the injection pulse. Acceleration rich mode is only used for transient fuel control (when moving the throttle).
Fuel cut-off mode during engine braking
When braking with the engine in gear and clutch engaged, the ECU may completely shut off the fuel injection pulses for short periods of time. Turning off and on the fuel supply in this mode occurs when certain conditions are created for the coolant temperature, crankshaft speed, vehicle speed and throttle opening angle.
Supply voltage compensation
If the supply voltage drops, the ignition system may produce a weak spark and mechanical movement «discoveries» injectors may take longer. The ECU compensates for this by increasing the energy storage time in the ignition coils and the duration of the injection pulse.
Accordingly, with increasing battery voltage (or voltage in the vehicle's on-board network) The ECU reduces the energy storage time in the ignition coils and the duration of the injection.
Fuel cut mode
When the engine is stopped (off ignition) fuel is not supplied by the nozzle, thus eliminating spontaneous ignition of the mixture in an overheated engine. In addition, no pulses are sent to open the injectors if the ECU does not receive reference pulses from the crankshaft position sensor, i.e. this means the engine is not running.
The fuel supply is also cut off when the maximum permissible engine speed is exceeded to protect the engine from operating at unacceptably high speeds.
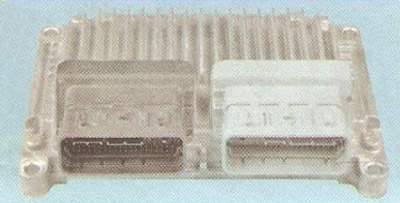
Electronic control unit
Electronic control unit (ECU, controller) engine is located in the central part of the air intake box and is the control center of the electronic engine control system. It continuously processes information from various sensors and manages systems that affect exhaust emissions and vehicle performance.
The ECU receives the following information:
- position and frequency of rotation of the crankshaft;
- camshaft position;
- coolant temperature;
- intake air temperature and pressure;
- accelerator pedal position;
- throttle position;
- oxygen content in the exhaust gases;
- the presence of detonation in the engine;
- vehicle speed;
- voltage in the vehicle's on-board network;
- request to turn on the air conditioner.
Based on the information received, the ECU controls the following systems and devices:
- fuel supply (injectors and fuel pump);
- air supply (throttle opening degree);
- ignition system;
- an adsorber of system of catching of vapors of gasoline;
- engine cooling fan;
- air conditioning compressor clutch;
- diagnostic system.
ECU turns on output circuits (injectors, various relays, etc.) by closing them «mass» through the output transistors, the only exception is the fuel pump relay circuit. The fuel pump is connected via a power relay. In turn, the relay winding is controlled by the ECU by closing one of the outputs to «mass».
The ECU is equipped with a built-in diagnostic system. It can recognize ECM malfunctions and warn the driver about them through a malfunction indicator in the engine management system. In addition, the ECU stores diagnostic codes that indicate the malfunction of a particular element of the system and the nature of this malfunction in order to assist specialists in diagnosing and repairing.
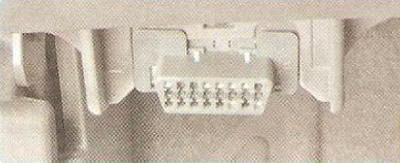
Diagnostic connector
The diagnostic connector is used to exchange data with the computer and is located on the left side under the instrument panel. A scanning device is connected to the diagnostic connector to read error information stored in the ECU memory, to check sensors and actuators in real time, to control actuators and reprogram the ECU.
The ECU contains the following types of memory:
- programmable read only memory (PROM);
- random access memory (RAM);
- electrically reprogrammable memory (ERPZU).
Programmable Read Only Memory (PROM). It contains a general program, which contains a sequence of working commands (control algorithms) and various calibration information. This information is injection, ignition, idle control data, etc., which depend on vehicle weight, engine type and power, transmission ratios, and other factors. PROM is also called a calibration memory. The contents of the PROM cannot be changed after programming. This memory does not need power to save the information recorded in it, which is not erased when the power is turned off, i.e. this memory is non-volatile.
Random access memory (RAM)
This «notebook» ECU. The unit's microprocessor uses it to temporarily store measured parameters for calculations and intermediate information. The microprocessor can enter data into it or read them out as necessary.
The RAM chip is mounted on the controller PCB. This memory is volatile and requires an uninterruptible power supply to maintain. When the power supply is interrupted, the diagnostic trouble codes and calculated data contained in the RAM are erased.
Electrically reprogrammable memory (ERPZU)
Used for temporary storage of car anti-theft system passwords (immobilizer). The password codes received by the ECU from the immobilizer control unit are compared with the codes stored in the EEPROM, as a result of which the engine start is allowed or prohibited.
The EEPROM records vehicle operating parameters such as total vehicle mileage, total fuel consumption, and engine operating time.
ERPZU also registers some violations of the engine and car:
- operating time of the engine with overheating;
- engine operating time on low-octane fuel;
- engine operation time exceeding the maximum allowable speed;
- engine operation time with misfiring of the air-fuel mixture, the presence of which is indicated by the signaling device of the engine management system;
- engine operation time with a faulty knock sensor;
- engine operation time with faulty oxygen concentration sensors;
- the time of movement of the car with excess of the maximum permitted speed during the break-in period;
- vehicle movement time with a faulty speed sensor;
- number of battery disconnections with the ignition switch on.
EEPROM is a non-volatile memory and can store information without powering the controller.
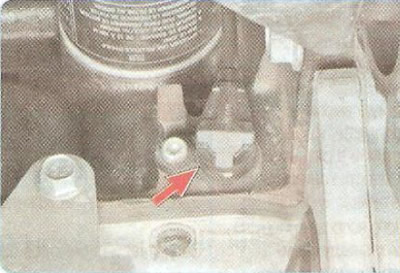
Crankshaft position sensor
The inductive type crankshaft position sensor is designed to synchronize the operation of the electronic control unit with the TDC of the pistons of the 1st and 4th cylinders and the angular position of the crankshaft.
The sensor is installed at the rear of the engine block opposite the drive disk on the crankshaft. The driving disk is a gear wheel with 58 slots, 57 of which are spaced at 6°intervals. The last groove is made wider to create a synchronization pulse («reference» momentum), which is necessary to coordinate the operation of the control unit with the TDC of the pistons in the 1st and 4th cylinders.
As the crankshaft rotates, the sensor's magnetic field changes, inducing AC voltage pulses. The control unit determines the speed of the crankshaft from the signals of the sensor and issues impulses to control the engine.
A malfunction of this sensor causes a complete failure of the engine control system: in the absence of its signal, it is impossible to start the engine.

Manifold absolute pressure sensor
The absolute pressure sensor in the intake pipe converts the vacuum in this pipe into an electrical voltage, by the value of which the ECU determines the engine load. The sensor is installed on the intake pipe and is connected to its cavity by a rubber tube. The output voltage of the sensor changes in accordance with the pressure in the intake pipe - from 4.9 V (at wide open throttle) up to 0.3 V (with damper closed). When the engine is not running, the control unit determines the atmospheric pressure from the sensor voltage and adapts the injection control parameters to the specific height above sea level. The atmospheric pressure values stored in the memory are updated periodically when the vehicle is in steady motion and during full throttle opening.
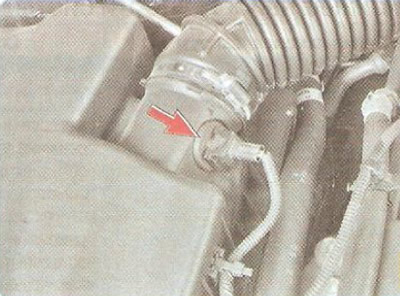
Intake air temperature sensor
The intake air temperature sensor is screwed into the hole in the air supply hose near the air filter. The sensor is an NTC thermistor. Based on the air temperature information from the sensor, the controller regulates the amount of fuel injected.
At the air temperature sensor, check the resistance at the sensor terminals under various temperature conditions.
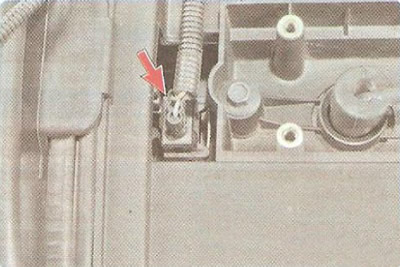
Phase sensor
The phase sensor is installed in the front part of the cylinder head between the toothed pulleys of the camshafts. The principle of its operation is based on the Hall effect. The sensor determines the TDC of the compression stroke of the piston of the 1st cylinder. The sensor signal is used by the controller to organize phased fuel injection in accordance with the order of operation of the cylinders. In the event of a circuit malfunction, the controller stores its code in its memory and turns on the engine control system alarm.
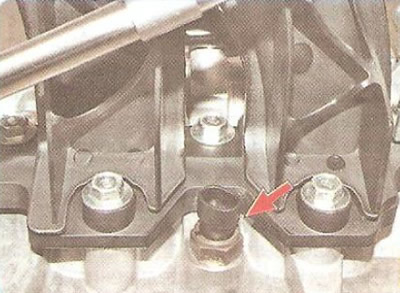
Coolant temperature sensor
The coolant temperature sensor is installed on the right side of the cylinder head between the first and second cylinders. The sensor is an NTC thermistor: the electrical resistance of the sensor decreases with increasing temperature. The ECU processes the sensor signal and sets the optimal enrichment of the working mixture when the engine warms up.
The electronic unit feeds the temperature sensor circuit with constant «pivotal» voltage. The signal voltage of the sensor is maximum when the air in the intake pipe is cold and decreases as its temperature rises. From the voltage value, the ECU determines the intake air temperature and makes adjustments when calculating the ignition timing. If the sensor fails or there are violations in its connection circuit, the ECU sets the fault code and remembers it. If the ECU continues to generate a DTC with good contact connections in the wiring, replace the air temperature sensor.
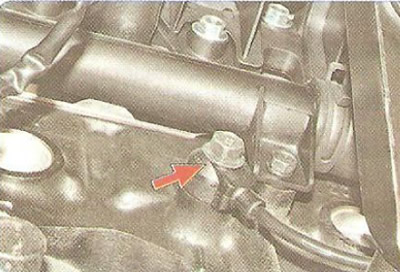
Knock sensor
The knock sensor is attached to the top of the cylinder block, picks up abnormal vibrations (detonation strikes) in the engine.
The sensitive element of the sensor is a piezoelectric plate. During detonation, voltage pulses are generated at the output of the sensor, which increase with increasing intensity of detonation impacts. The controller, based on a sensor signal, regulates the ignition timing to eliminate detonation fuel flashes.
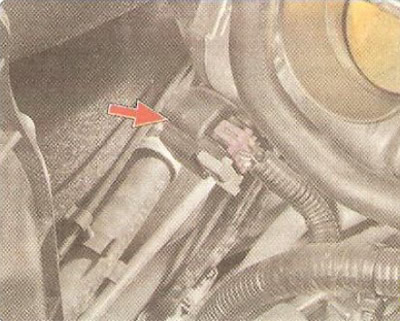
Throttle position sensor
Throttle position sensor (TPS) mounted on the side of the throttle body (under cover) and is connected to the throttle axis.
It is a potentiometer, one end of which is supplied with «plus» supply voltage (5 V), its other end is connected to «weight». From the third output of the potentiometer (from the slider) is the output signal to the ECU. When the throttle is turned (from impact on the control pedal), the voltage at the output of the sensor changes. When the throttle is closed, it is below 0.5 V. When the throttle opens, the voltage at the sensor output rises and should be more than 4 V when the throttle is fully open. By monitoring the output voltage of the sensor, the ECU adjusts the fuel supply depending on the throttle opening angle (those. at the request of the driver). TPS does not require adjustment, as the electronic unit perceives idling (those. full throttle closing) as a zero point.
In the event of a throttle sensor failure, the ECU memorizes the sensor's fault code, turns on the engine management system warning lamp, and calculates the estimated throttle valve opening angle value from the crankshaft speed and from the signals from the temperature and absolute air pressure sensors in the intake pipe.
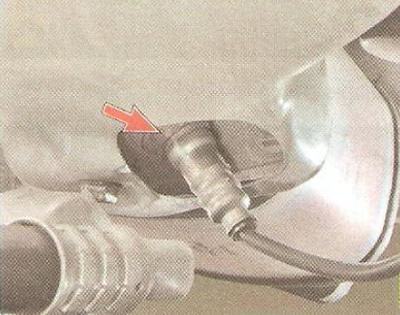
Control oxygen sensor
The oxygen concentration control sensor is used in the feedback injection system and is installed in the exhaust manifold. To correct the calculations of the duration of the injection pulses, information is used on the presence of oxygen in the exhaust gases, this information is provided by the control oxygen concentration sensor. The oxygen contained in the exhaust gases reacts with the sensor, creating a potential difference at the sensor output. It varies from approximately 0.1 V (high oxygen content - lean mixture) up to 1 V (low oxygen - rich mixture).
By monitoring the output voltage of the oxygen concentration sensor, the controller determines which command to adjust the composition of the working mixture to apply to the injectors. If the mixture is lean (low potential difference at the sensor output), then the controller gives a command to enrich the mixture; if the mixture is rich (high potential difference) - to lean the mixture.
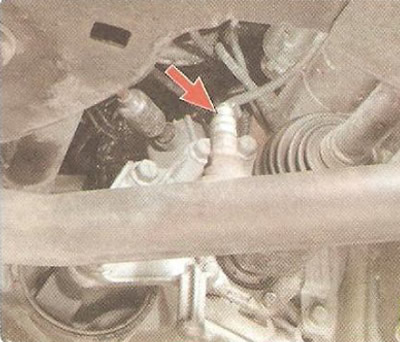
Diagnostic oxygen sensor
The diagnostic oxygen concentration sensor is installed in the exhaust pipe after the converter, it works on the same principle as the control sensor. The signal generated by the diagnostic oxygen concentration sensor indicates the presence of oxygen in the exhaust gases after the converter. If the converter is working properly, the readings of the diagnostic sensor will differ significantly from the readings of the control sensor,