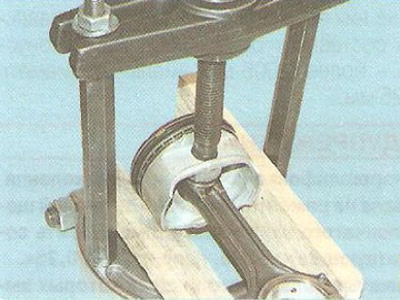
1. Insert the connecting rod into the piston, lubricate the piston pin with engine oil and press it into the connecting rod using the same tool on which the pin was pressed out, or with a hammer and a suitable mandrel inserted into the inner hole of the pin. The piston should be pressed with the boss against the upper head of the connecting rod in the direction of pressing the pin, which will allow it to take the correct position.
Note: The pin is inserted into the upper head of the connecting rod with an interference fit, therefore, to facilitate assembly and maintain its fit, it is recommended to heat the connecting rods by placing them with their upper heads for 15 minutes in an electric furnace heated to 240°C. The heating temperature of the connecting rod can be controlled using a thermochromic pencil. To properly connect the pin to the connecting rod, press in the pin as soon as possible, since after it cools down, the position of the pin cannot be changed.
2. Install the piston rings in the reverse order of removal, positioning them as shown in fig. 5.12.
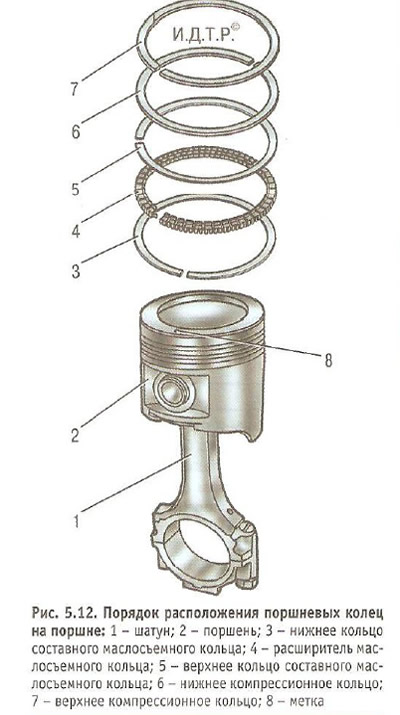
Warning: When installing, do not expand the rings more than necessary, so as not to deform or break them.
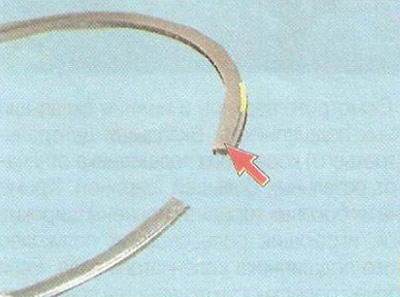
Notes: Install the lower compression ring with the undercut down (shown by arrow) into the second groove.
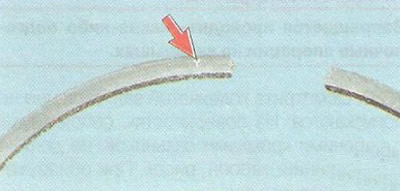
Marking «Y» on the compression rings must point upwards.
3. Orient the rings as shown in fig. 5.13. Install the rings on the remaining pistons.
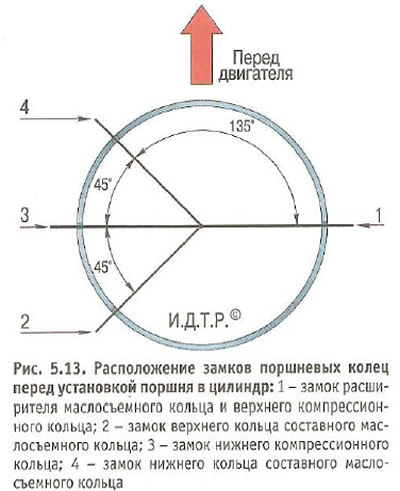
Note: The locks of the upper and lower rings of the compound oil scraper ring must be located at a distance of 25-30 mm, respectively, to the left and right of the expander lock.
4. Lay in bed of the block of cylinders the top loose leaves of radical bearings.
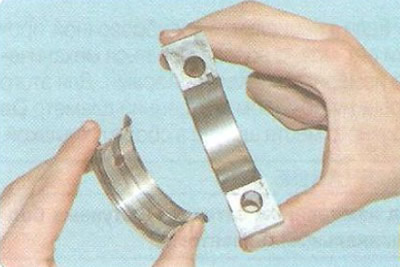
Notes: Medium (third) the main bearing, lay a bushing of increased thickness with support collars.
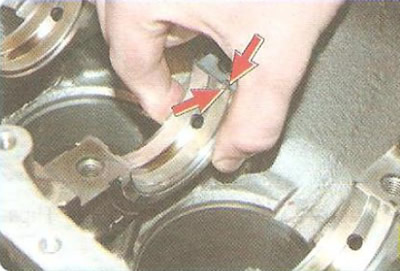
Install the inserts so that the insertion tab of the insert is aligned with the notch on the bed.
5. Lubricate the liners with engine oil.
6. Install the crankshaft in the cylinder block.
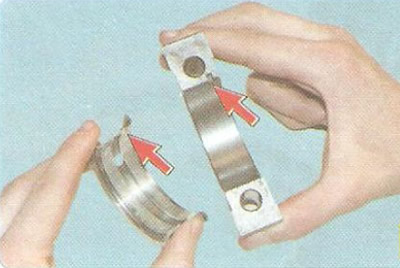
7. Lay the lower loose leaves in the main bearing caps, aligning the tabs of the loose leaves with the recesses on the caps.
Note: The upper and lower main bearing shells may differ in the location of the oil supply hole. Install the liners so that these holes coincide with the holes of the channels for supplying oil in the beds of the main bearing supports. After inserting the shells into the sockets, their ends protrude slightly, therefore, for the correct orientation of the shells, when the bearing cap bolts are finally tightened, make sure that the protrusion of both ends is the same.
8. Lubricate the crankshaft journals with engine oil.
9. Grease loose leaves in covers of radical bearings of a cranked shaft with engine oil.
10. Establish covers of radical bearings according to serial numbers, having oriented on labels.
Warning: Use a soft-faced hammer made of brass, lead, or polyurethane to install the crankshaft bearing caps. It is forbidden to install the covers by tightening the fasteners, since in this case the seating surfaces of the covers and the cylinder block will be damaged.
11. Install the cover bolts, evenly tighten the bolts to failure, without completely tightening, unscrew one turn, tighten with a torque of 50 Nm (5.0 kgf·m) and tighten 50°and then another 15°.
Warning: Be sure to replace the main bearing cap bolts with new ones.
12. Check up correctness of assembly, having turned a cranked shaft a hand on some turns. The shaft must rotate freely and smoothly.
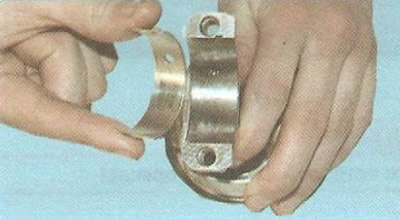
13. Install the liners in the connecting rods, aligning the insertion tab with the notch on the connecting rod.
14. Lubricate the cylinder mirrors, pistons, piston rings and connecting rod bearings with engine oil.
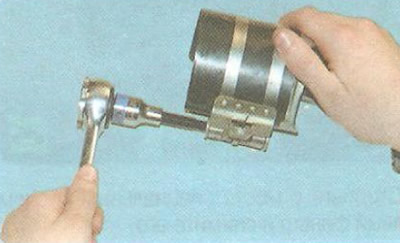
15. Install a ring compression tool on the piston and, turning the screw, compress the rings.
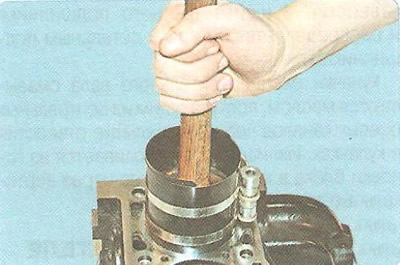
16. Turn the crankshaft so that its connecting rod journal, on which the connecting rod and piston group is mounted, is at TDC. Install the piston in the cylinder according to the marking of the cylinder number on the connecting rod, press (e.g. hammer handle) on the piston and slide it from the mandrel into the cylinder. Install the pistons in the rest of the cylinders in the same way.
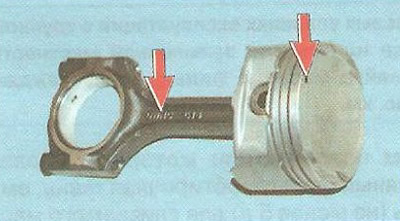
Note: When installing pistons in cylinders, the mark (triangle) on the piston and the lettering on the connecting rod must face the front of the engine.
Warning: Install the piston in the cylinder carefully so as not to damage the connecting rod journal of the crankshaft with the lower end of the connecting rod.
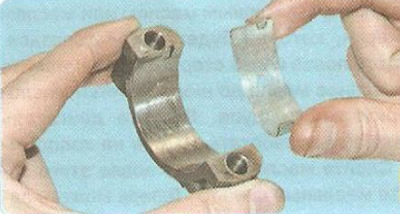
17. Install the connecting rod bearings into the connecting rod caps by aligning the insert tab with the notch in the cap.
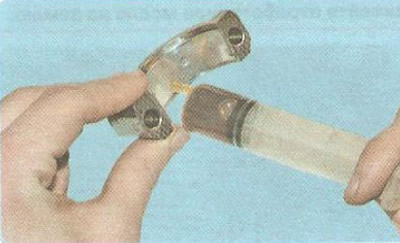
18. Lubricate the connecting rod bearings in the connecting rod caps and the connecting rod journals of the crankshaft with engine oil.
19. Establish a cover of a rod, having connected a rod with a neck of a cranked shaft and having combined labels on a rod and a cover.
20. Screw rod bolts without tightening them completely.
21. Tighten the connecting rod bolts to failure, without tightening them completely; then unscrew them one turn, tighten with a torque of 25 Nm (2.5 kgf·m) and tighten 30°and then another 15°.
22. Check up ease of movement of a rod along a rod neck. If seizing, unscrew the connecting rod bolts and re-tighten them to the specified torque.
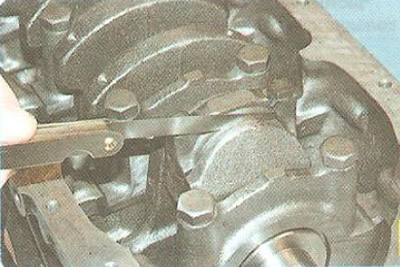
23. Check the side clearance of the connecting rod, it should be 0.070-0.242 mm. Increased clearance indicates excessive wear on the crankshaft crank cheeks. In this case, replace the crankshaft.
24. Similarly fix covers of other rods.
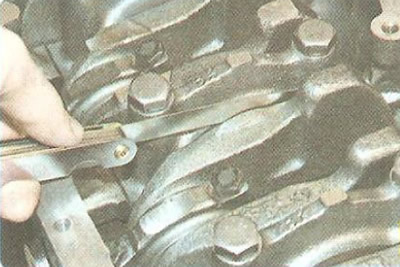
25. Check the axial clearance of the crankshaft, it should be 0.07-0.1 mm. Increased clearance indicates wear on the crankshaft support flanges or the middle main bearing bed. In this case, replace the crankshaft. If this does not lead to a decrease in axial clearance, the cylinder block will have to be replaced.
26. Install the crankshaft rear oil seal (see «Replacing the crankshaft seals»).
27. Install the oil receiver and oil pump (see «Removal and installation of the oil pump»).
28. Install the oil pan (see «Replacing the oil sump seal»).
29. Install flywheel (cm, «Removal, troubleshooting and installation of the flywheel»).
30. Next, assemble the engine in the reverse order of disassembly. Installation of a head of the block of cylinders is described in subsection «Replacing the cylinder head gasket», water pump - subsection «Water pump replacement», timing belt - in subsection «Replacing the timing belt and its tension roller».
Helpful advice: After assembling the engine, it is recommended to run it on the stand. Since it is impossible to do this outside of special repair organizations, after installing the engine on the car, run it in a simplified cycle in the following order.
1. Make sure that the throttle actuator is adjusted correctly, fill in oil and coolant, check the tightness of all connections.
2. Start the engine and let it run without load for the next cycle. Do not bring the engine to maximum conditions.
Crankshaft speed, min-1 | Operating time, min |
820-900 | 2 |
1000 | 3 |
1500 | 4 |
2000 | 5 |
3. During operation, check the tightness of the engine and its systems, oil pressure, pay attention to the presence of extraneous noise.
4. If extraneous noises or other malfunctions are found, stop the engine and eliminate their cause.
5. After starting the operation of the car, observe the modes provided for the break-in period of a new car.