1. Remove the alternator from the vehicle (see «Removal and installation of the generator»).
2. Remove the generator pulley from the rotor shaft (see «Alternator pulley replacement»)...
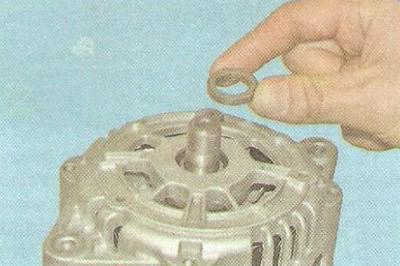
3....and a spacer.
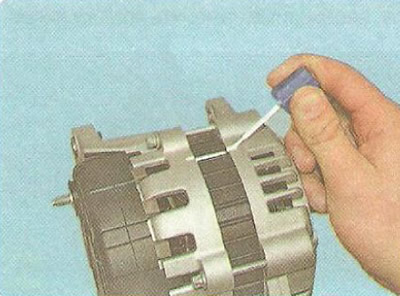
4. Mark the relative position of the stator and generator covers.
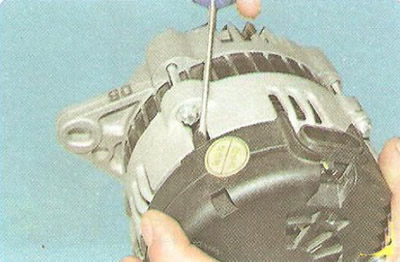
5. Press the four latches...
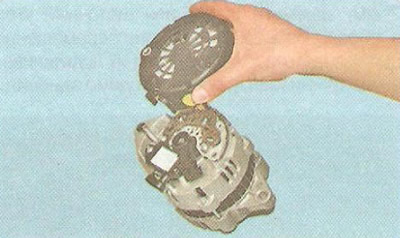
6.... and remove the protective casing of the generator.
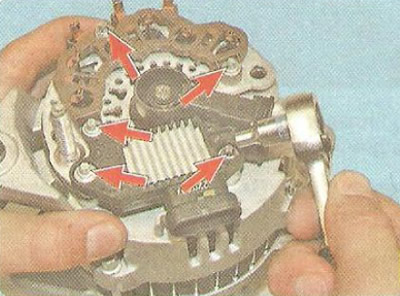
7. Using a TORX E4 key, remove the five bolts securing the voltage regulator with the brush assembly and the rectifier unit to the front cover.
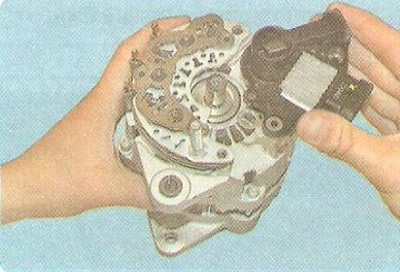
8. Remove the voltage regulator with the brush assembly.
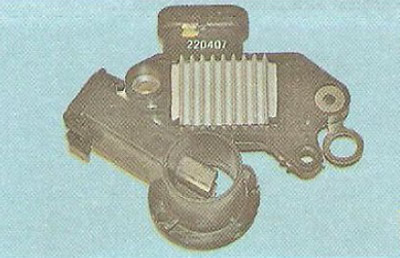
Note: This is how the voltage regulator with the brush assembly looks like, removed from the generator.
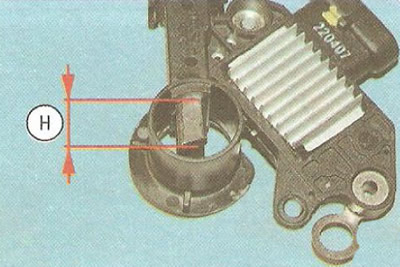
9. Check the free protrusion of the brushes. If the H dimension is less than 2 mm, replace the brushes or brush assembly. Check the ease of movement of the brushes in the brush holder. If they are wedged, the brush assembly also needs to be replaced.
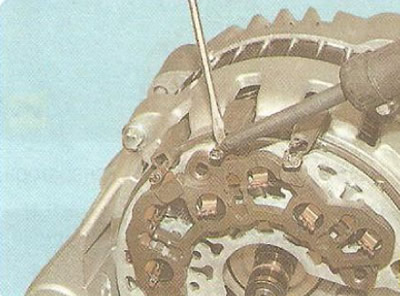
10. Unsolder the three leads of the stator winding from the rectifier unit...
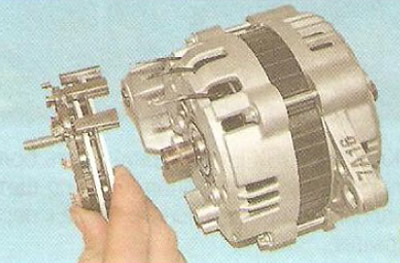
11.... and remove the rectifier block.

Note: This is how the removed rectifier unit looks from the side of the protective cover...
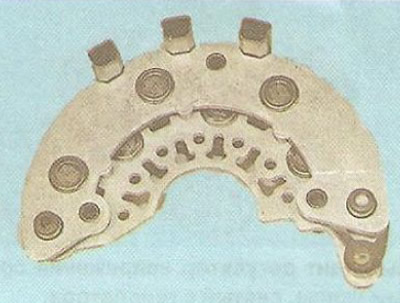
...and from the stator side.
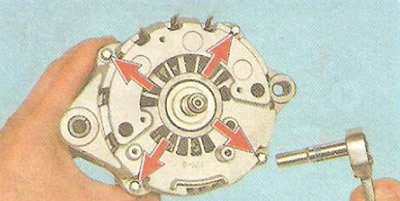
12. Using the E8 TORX key, remove the four tie bolts.
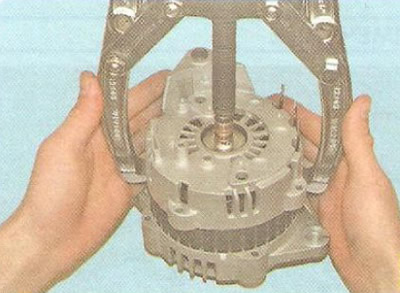
13. Press the front cover off the rotor shaft bearing...
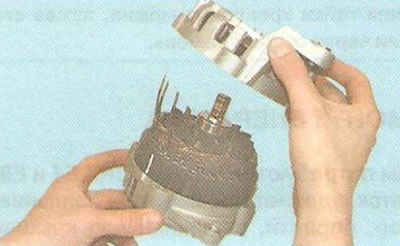
14.... and remove it.
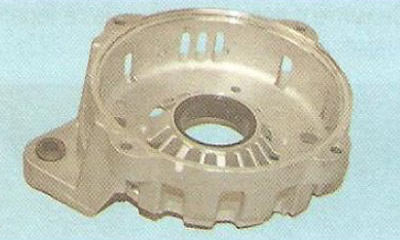
15. Inspect the front cover. The plastic bushing of the alternator rotor rear bearing must be firmly seated in the hole in the cover. If the bearing is correctly seated in the sleeve, there should be no evidence of slippage of the bearing outer ring. If cracks are found in the cover, especially in the places where the generator is attached, it is necessary to replace the cover with a new one.
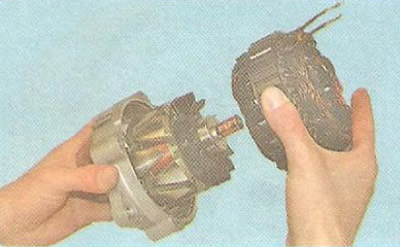
16. Carefully prying off the stator with a screwdriver, separate the stator and rear cover.
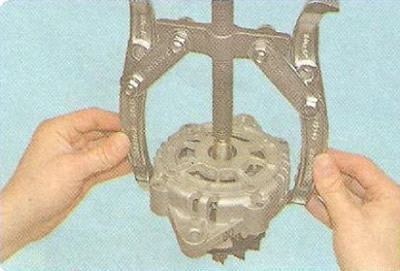
17. Press the rotor shaft out of the rear cover bearing...
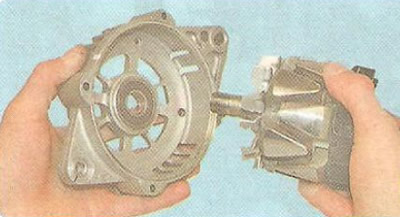
18.... and separate the rotor and cover.
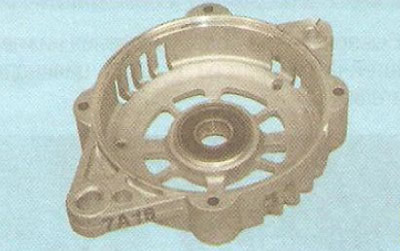
19. Examine the back cover. If, during rotation of the bearing, play is felt between the rings, rolling or jamming of the rolling elements, the protective rings are damaged, or there are lubricant leaks, replace the bearing. If cracks are found in the cover, especially in the places where the generator is attached, it is necessary to replace the cover with a new one.
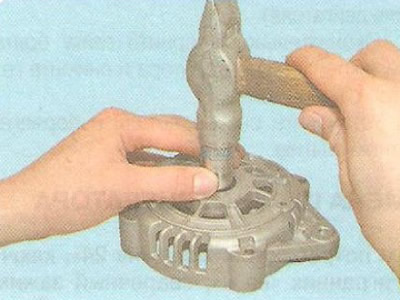
20. To replace the rotor shaft front bearing, press it out of the cover.
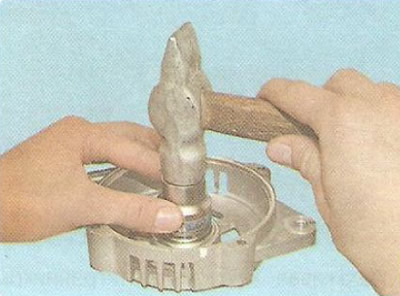
21. Press the new bearing into the cover with a drift of suitable diameter, applying force to the outer ring,
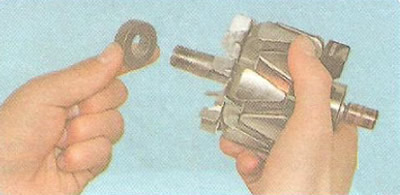
22. Remove the distance ring from the rotor shaft...
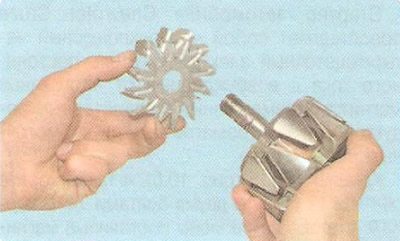
23.... and the fan impeller.
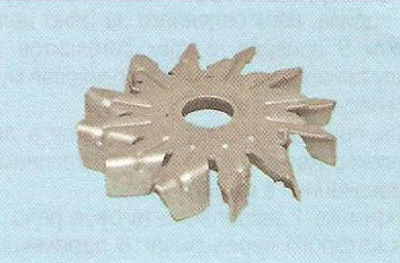
24. Inspect the fan impeller. It should not be mechanically damaged, all blades should be located at the same angle to the plane of rotation. Otherwise, replace the impeller
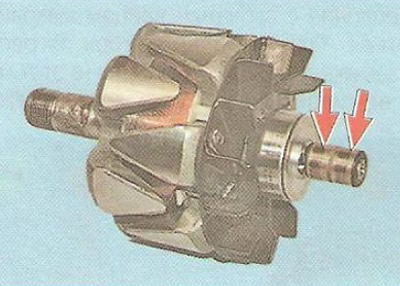
25. Inspect slip rings. If they have scuffs, scratches, scratches, wear marks from brushes and other damage, the rings must be ground. If damage to the rings cannot be removed with sandpaper, you can grind the rings on a lathe, removing the minimum layer of metal, and then grind.
26. Check up ease of rotation of the bearing from slip rings. If during rotation of the bearing there is play between the rings, rolling or jamming of the rolling elements, damaged protective rings or there are grease leaks, the bearing should be replaced. For this...
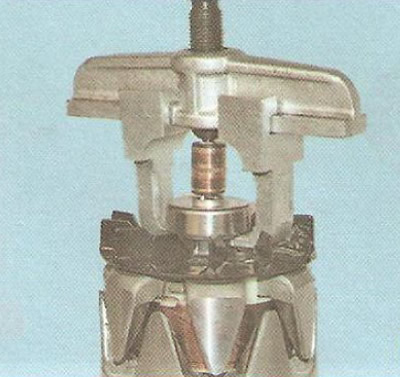
27.... press the bearing off the bearing journal of the rotor shaft...
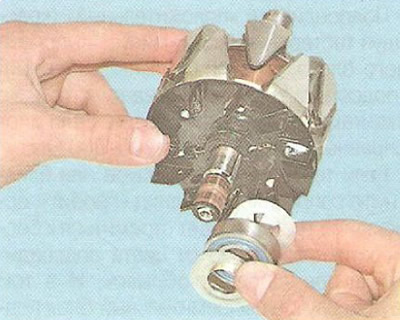
28.... and remove the bearing from the shaft and the protective washers.
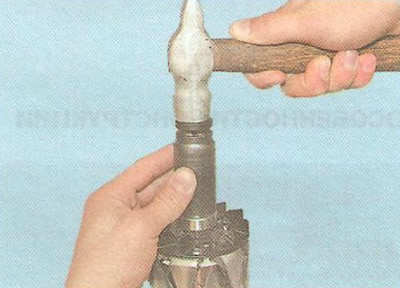
29. Press the new bearing onto the rotor shaft against the stop against the shoulder of the shaft, applying force to the inner race of the bearing through a mandrel of suitable diameter.
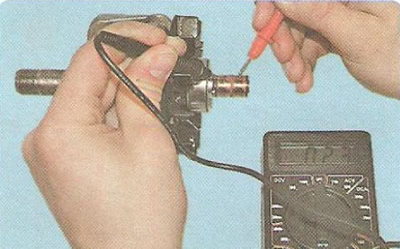
30. Check the resistance of the rotor winding with a tester by connecting it to slip rings. The resistance should be approximately 3-5 ohms. If the tester shows infinity, then there is a break in the rotor winding - the rotor must be replaced.
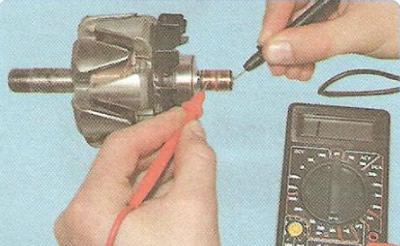
31. Check the absence of a short circuit in the rotor winding to the housing by connecting the tester leads to any slip ring and the rotor housing. The tester should show infinity.
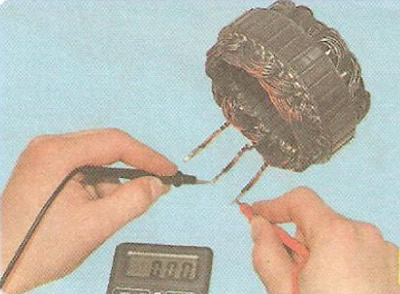
32. Check the stator winding for an open circuit, alternately measuring the resistance between all winding leads with a tester. If the measured resistance tends to infinity, then the stator must be replaced.
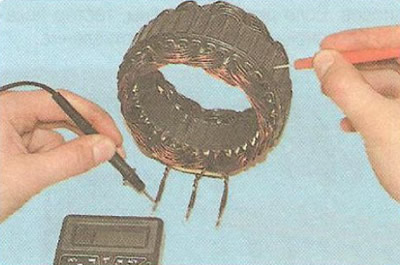
33. Connect the tester probes to the stator housing and, in turn, to each winding terminal. The measured resistance must be very large (tends to infinity). Otherwise, replace the stator.
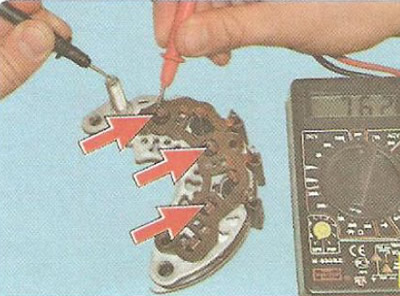
34. Check «positive» diodes by connecting «negative» (black) tester probe to output «plus» generator, and «positive» (red) the probe is alternately connected to the three contact leads of the diodes. If the diodes are working, the tester will show 700-800 ohms.
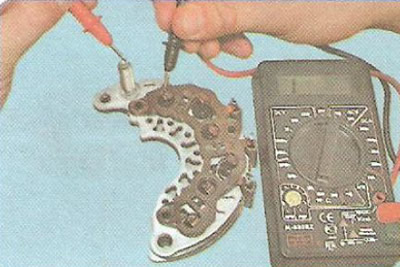
35. Connect «positive» (red) tester probe to output «plus» generator, and «negative» (black) connect the probe in turn to the same three contact leads of the diodes. If the diodes are good, the tester will show infinite resistance.

36. Check «minus» diodes by connecting «negative» (black) tester probe to output «minus» rectifier block, and «positive» (red) the probe is alternately connected to the three contact leads of the diodes. If the diodes are good, the tester will show infinite resistance.
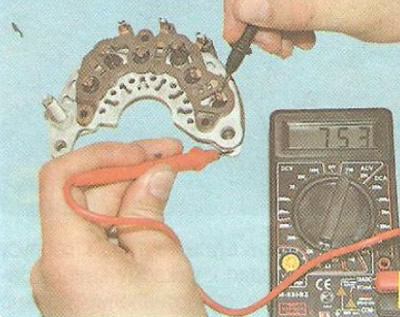
37. Connect «positive» (red) tester probe to output «minus» rectifier block, and «negative» (black) connect the probe in turn to the same three contact leads of the diodes. If the diodes are working, the tester will show 700-800 ohms.
38. If the tester shows low or close to zero resistance, the diode «broken»; if the tester reading tends to infinity, regardless of the color of the connected probes, the diode «in the cliff». In both cases, the rectifier unit must be replaced.
39. Assemble the generator in the reverse order of disassembly, orienting the generator covers and the stator according to the previously made marks.