You will need: key «at 14», a special pressure plate puller, a three-legged compressor pulley puller, a circlip puller, a press or a bearing extractor.
1. Remove the refrigerant from the air conditioning system (see «Removing refrigerant from the air conditioning system») and disconnect the wire from the terminal «minus» battery.
2. Remove the compressor (see «Removal and installation of the compressor of the conditioner»).
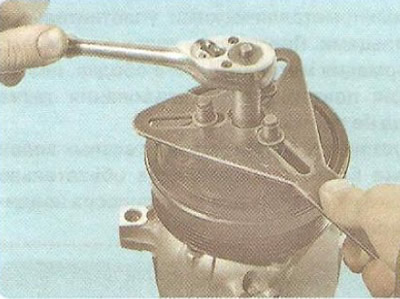
3. While holding the pressure plate from turning, unscrew the fastening nut.
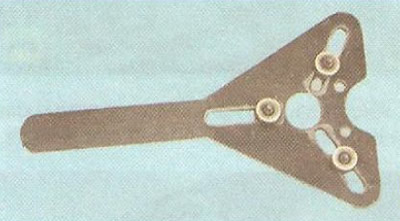
Notes: Use a tool to hold the compressor pressure plate from turning.
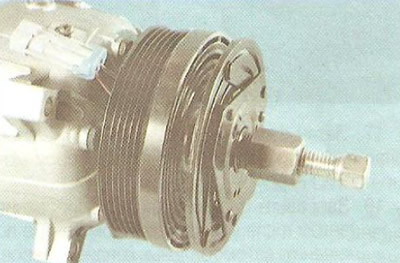
4, Install the special thread extractor and press the pressure plate off the compressor shaft.
Helpful Tip: The pressure plate is installed on the shaft with an interference fit, so do not try to remove it by inserting a screwdriver into the gap between the pulley and the plate. This will lead to deformation of the plate and the need to replace it.

To remove the pressure plate, use a special threaded puller.
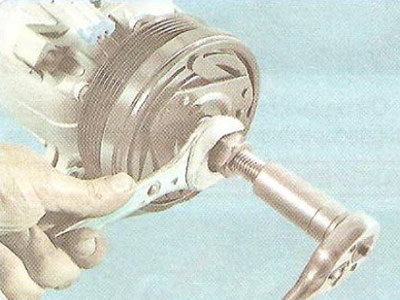
Screw the sleeve of the puller into the threaded hole in the hub of the pressure plate and, turning the stop screw of the puller, compress the plate.
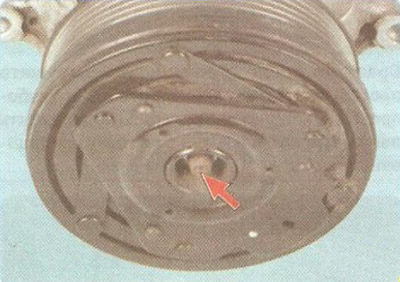
During operation, the thread in the hub hole can become clogged with dirt and rust. In this case, clean the thread before screwing in the puller sleeve.
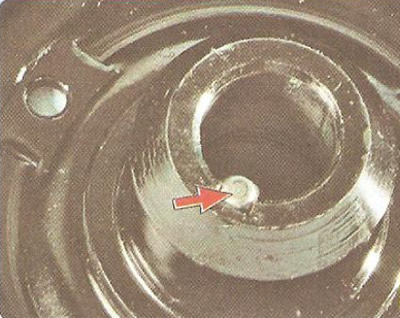
5. Inspect the pressure plate key and keyway. If the keyway is worn, replace the insert.
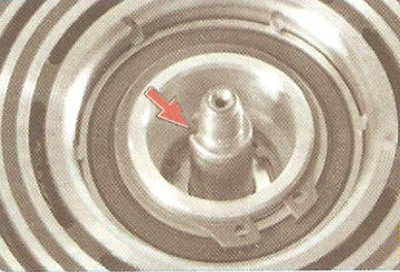
6. Inspect the surface of the shaft seal. If there are signs of oil leakage through the shaft seal, the compressor must be replaced.
Helpful Hint: In some cases, when a leak is detected, the seal can be replaced. However, it should be remembered that a leak, as a rule, is caused by shaft play due to wear of the support bearings, corrosion or wear of the shaft surface in the area of \u200b\u200bthe seal. Therefore, the replacement of the gland will give at best only a short-term result. If a gland leak is detected, we recommend replacing the compressor assembly.
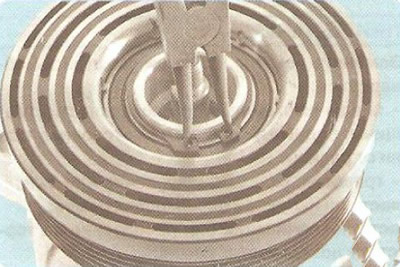
7. With a special puller, remove the pulley bearing circlip.
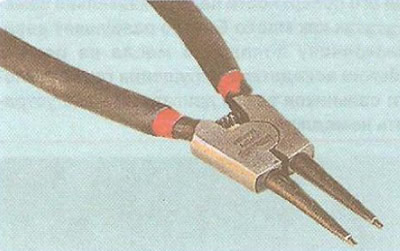
Note: To remove the retaining ring, use a special expanding tool.
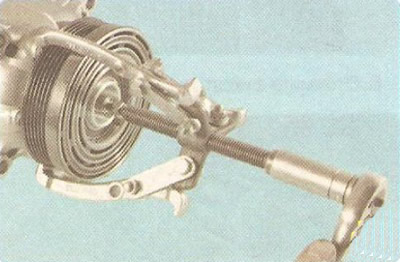
8. Install the puller and press the pulley off the compressor front cover seat.
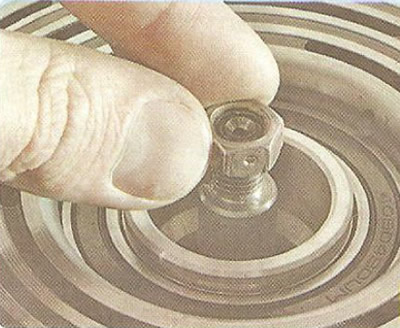
Warning: To avoid damaging the threaded end of the shaft when installing the puller, screw the old pressure plate mounting nut onto it a few turns.
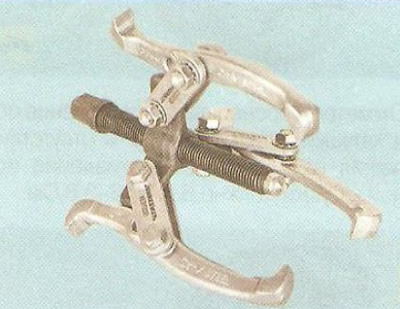
Helpful Hint: It is convenient to use a universal three-arm puller to remove the pulley.
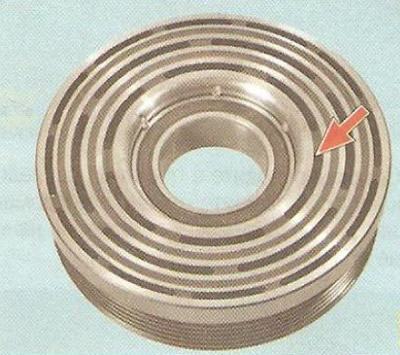
9. Inspect the working surfaces of the friction pulley...
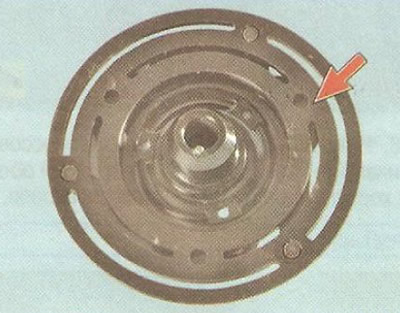
10.... and the pressure plate, paying attention to the presence of deep ring marks, scoring, obvious signs of wear and overheating. Replace defective parts if necessary.

11. Inspect rivet connections A and B, elastic steel leashes B of the plate. If the drivers are broken or the rivets are loose, replace the pressure plate.
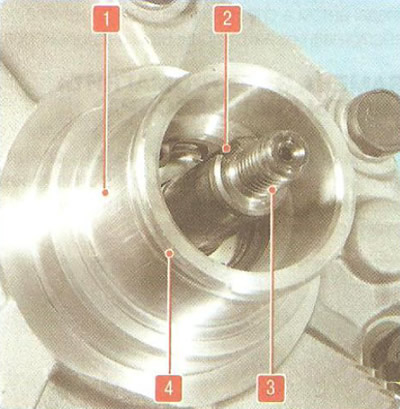
12. After removing the pulley, inspect the keyway 2 and the threaded tip 3 of the shaft, the groove 4 for the retaining ring and the seating surface 1 of the neck of the cover (for clarity, the magnet coil is removed). If they are worn or damaged, the compressor must be replaced.
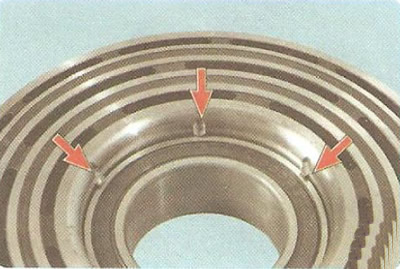
13. On a lathe, cut off the folds that secure the bearing in the pulley.
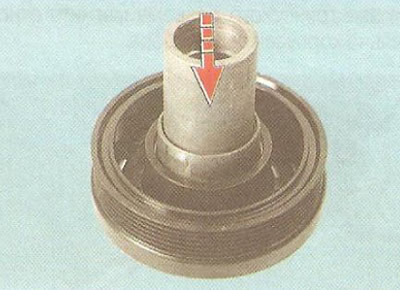
14. With a mandrel of a suitable diameter, press the old bearing out of the pulley.
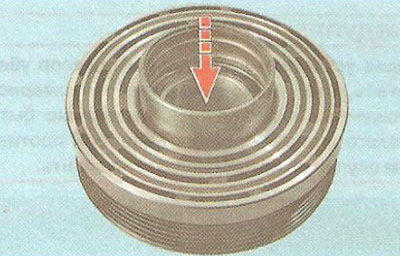
15. Press in the new bearing. When pressing in, apply force only to the outer race of the bearing. As a mandrel, you can use the outer race from the old bearing.
16. After pressing, fix the bearing by punching the edge of the pulley mounting hole.
Warning: When pressing the bearing, be as careful as possible.
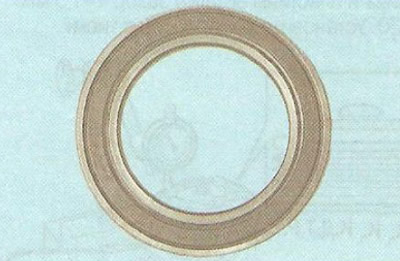
The outer race of the pulley bearing has a very thin wall. Even slight misalignment can lead to bearing failure. After pressing, check the condition of the bearing. It should rotate evenly, silently, without jamming. There must be no axial and radial play.
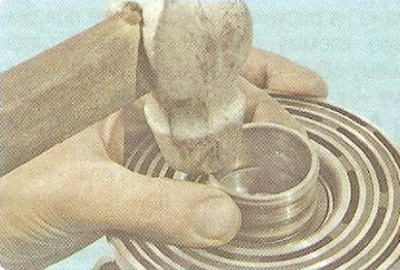
17. Press the pulley onto the compressor front cover. When pressing on, apply pressure only to the inner race of the bearing. As a mandrel, you can use the inner race from the old bearing.
18. Install retaining ring. Make sure the ring is fully seated in the groove.
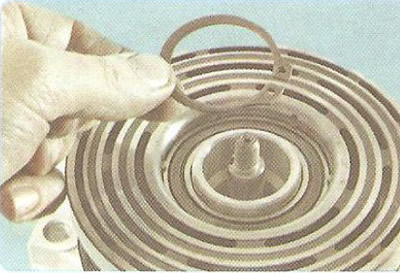
Warning: After installing the pulley on the compressor, make sure that the pulley rotates evenly, silently, without binding. There should be no axial or radial runout. Otherwise, the pulley must be replaced.
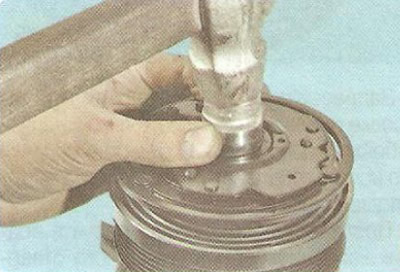
19. Slide the pressure plate onto the shaft, aligning the key and keyways on the shaft and the plate hub. Press the plate onto the shaft so that there is a gap of 1-1.5 mm between the friction surfaces of the pulley and the plate.
20. Install the compressor in a vise.
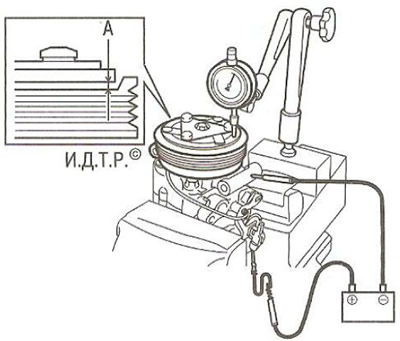
21. Install the dial gauge as shown. Connect the positive battery terminal to the coil winding connector and the negative terminal to the compressor housing. Measure the gap A between the friction surfaces of the pressure plate and the pulley (the clearance is equal to the measured difference in dimensions between the positions of the pressure plate with the compressor clutch engaged and disengaged) every 60°around the circumference. If the gap is not the same at different points on the circle, then the pressure plate is deformed and must be replaced. The nominal gap should be 0.35-0.85 mm. If the clearance is greater, press the hub onto the shaft. If less, press the hub off the shaft with a puller.
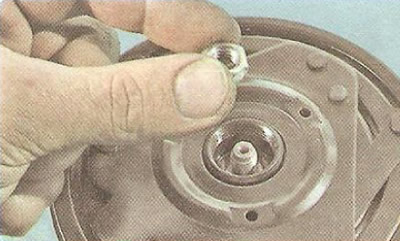
22. After completing the adjustment, screw on a new lock nut and tighten it to a torque of 5 Nm.
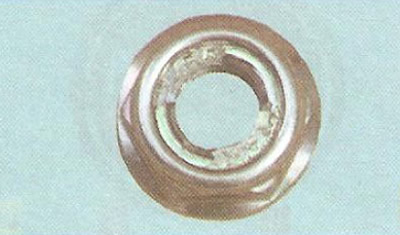
Note: Use the special disposable lock nut to secure the pressure plate.
23. Install the compressor and all removed parts in the reverse order of removal.
24. Charge the A/C system with refrigerant at a qualified automotive A/C service center.