Removal procedure
1. Remove the engine assembly.
2. Remove both cylinder heads as an assembly.
3. Remove the oil pan assembly.
4. Remove the connecting rod and piston assembly.
5. Remove the oil pump assembly.
6. Remove the rear oil seal and crankshaft cover assembly.
7. Remove crankshaft position sensor (CKP).
8. Unscrew the side bolts (3) securing the main bearing cap.
Attention! The main bearing cap outer bolts are dynamically tightened during reassembly and must be replaced before reassembly. The outer main bearing cap bolts, which will not be replaced, cannot be tightened to the correct clamping torque, which can cause severe engine damage.
9. Loosen the outer bolts (1) securing the main bearing cap.
10. Loosen the inner bolts (2) securing the main bearing cap.

11. Loosen nuts (1) crankshaft main bearing cap puller, tool no. J-41818 (2), to separate the beveled taper bushings. Insert the bushings into the holes for the internal bolts of the cover (3) front main bearing.
12. Tighten the puller nuts to 11 Nm (97 lb-in).
13. Install "slide hammer", tool no. J-6125-1B (4), onto the main bearing cap remover and remove the main bearing cap.
14. Repeat steps 9 through 13 for the remaining main bearing caps.
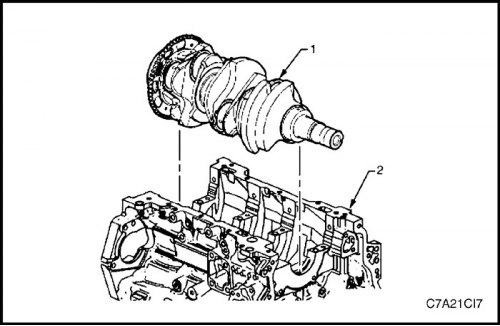
15. Remove the crankshaft (1) from cylinder block (2), lifting evenly to avoid pinching the main thrust bearing.
16. Move the crankshaft to a safe location.
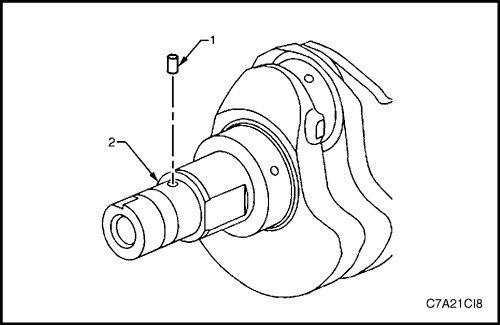
17. Remove pin if necessary (1) crankshaft sprocket drive from crankshaft (2).
Measuring the end play of the crankshaft
1. Install a dial indicator on the front end of the crankshaft.
2. Gently move the crankshaft lever towards the front and rear of the cylinder block while observing the movement of the dial indicator.
3. The axial play of the crankshaft must not exceed the specifications.
4. If specifications are exceeded, check thrust bearing OD and crankshaft thrust wall for wear and/or excessive wear. Compare the values with the specifications.
5. If necessary, replace the thrust bearing or crankshaft.
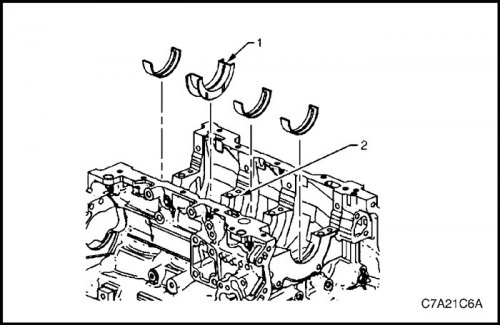
main bearing
1. Prepare a piece of cardboard or something similar numbered 1 to 4 to identify the bearings.
Note: The main bearing journals are numbered from the front of the engine.
2. Remove the upper halves of the crankshaft bearings from the cylinder block. Note the position of the thrust bearing (1) on the neck number 3 (2).
3. Lay the upper halves of the crankshaft bearings on the cardboard in their respective positions.
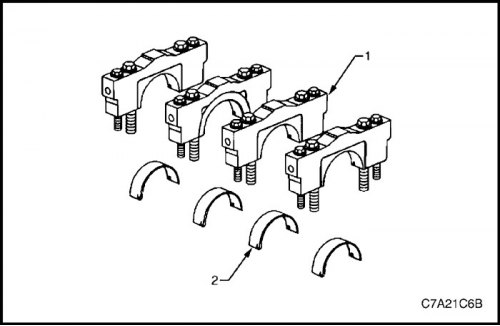
4. Remove the bottom halves (2) crankshaft bearings with caps (1) main bearings.
5. Lay the lower halves of the crankshaft bearings on the cardboard in their respective positions.
Cleaning and checking
Cleaning the crankshaft and main bearings
1. Clean the following components in solvent and then dry with compressed air:
- crankshaft bearings;
- Connecting rod bearings
- crankshaft journals;
- connecting rod journals of the crankshaft;
- channels for crankshaft lubrication, as well as
- threaded holes in the crankshaft.
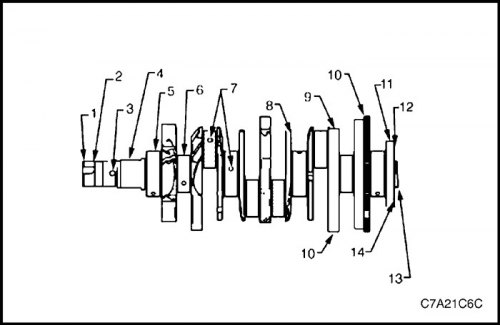
Inspection of the crankshaft and main bearings
1. Carry out the following inspections:
- Hole check (1) under the crankshaft vibration damper bolt for thread damage.
- Area check (2) crankshaft vibration damper mountings for damage.
- Hole check (3) under the crankshaft sprocket pin for damage.
- Flat Surface Inspection (4) oil pump drive for damage.
- Checking the main journals (5) crankshaft for damage.
- Checking the connecting rod journals (6) crankshaft for damage.
- Checking the lubrication channels (7) crankshaft for obstructions.
- Surface check (8) thrust wall of the crankshaft main bearing for damage.
- Checking counterweights (9) crankshaft for damage.
- Checking the teeth of the encoder ring (10) crankshaft for damage.
- Surface check (11) crankshaft rear main oil seal for damage.
- Checking the mounting surface (12) flywheel "flexplate" crankshaft for damage.
- Base hole check (13) crankshaft for damage.
- Hole check (14) under the engine flywheel bolts on the crankshaft for thread damage.
2. Repair or replace crankshaft if necessary.

Checking the crankshaft main bearings
Attention! All connecting rod and main journal bearings used with the engine running must be replaced. Never reuse crankshaft bearings or connecting rod bearings.
Note: The following bearing wear conditions should be used to diagnose engine operating conditions or the root cause of the condition.
1. Fatigue test for dimples or cavities (2). Flattened parts of bearing halves (1) also indicate fatigue.
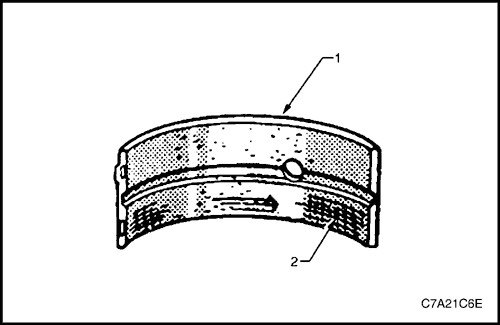
2. Check for excessive tearing or discoloration (2) on both front and back sides of bearing halves (1).
3. Check the main bearings for inclusions of dirt in the bearing material.
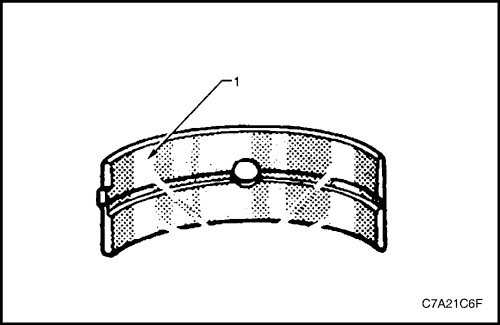
4. Check for improper fit, indicated by bright, polished parts (1).
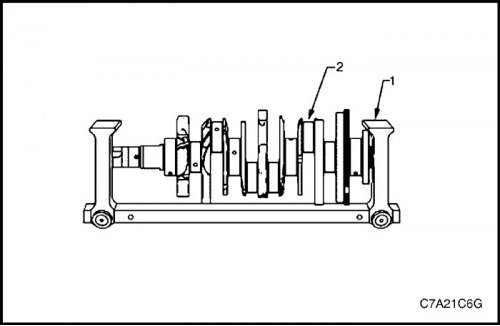
Crankshaft measurement
1. Use the right tool (1), to support the crankshaft (2).
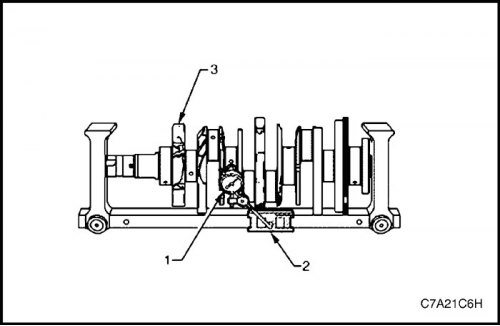
2. Using a dial indicator (1) and magnetic base (2), carefully rotate the crankshaft (3) hands. Measure the crankshaft journals with wear in mind and compare with engine specifications.
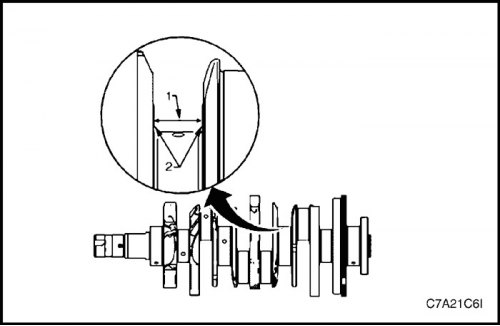
3. Measure Width (1) thrust wall of the crankshaft, referring to wear, with an internal micrometer with engine specifications.
4. Measure the surface (2) bearing wall of the crankshaft, referring to exhaustion, with a dial indicator mounted on a magnetic stand and compare with engine specifications.
5. If the crankshaft journals are damaged or worn outside of specifications, the crankshaft can be ground down 0.25mm. There is only one oversized rebuild main bearing available for service.
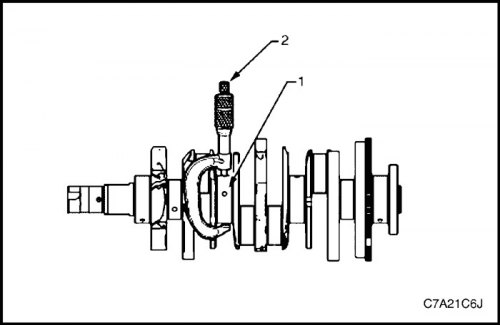
6. Check the main journals (1) crankshaft, referring to a reduction in size from nominal, the outer micrometer (2).
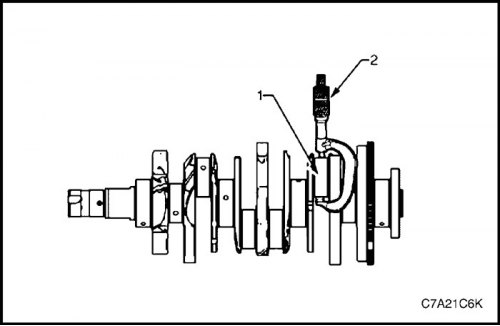
7. Check the crankpins (1), referring to the reduction in size from nominal, the outer micrometer (2).
8. Compare your measurements with the values listed in the engine specifications. If the crankshaft journals have wear outside of specifications, the crankshaft can be ground down 0.25mm. There is only one oversized connecting rod bearing rebuild available for service.
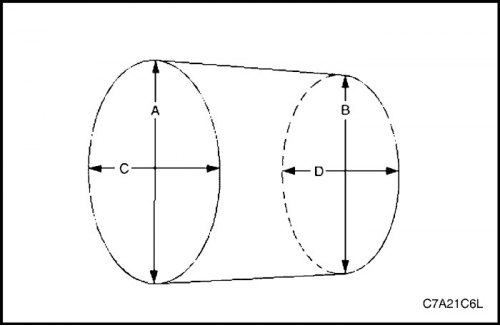
9. Measure the crankshaft main and connecting rod journals for out-of-roundness in the following order:
A. With an outside micrometer, measure the neck in two places, at the extreme anterior and the extreme posterior. Let's call these points A and B.
b. Measure the neck at two other locations exactly 90 degrees from the first points. Let's call these points C and D.
c. Subtract A from C and B from D. These differences will indicate the ovality of the neck.
d. The ovality should not exceed a maximum of 0.004 mm.
e. If the journals have wear outside of specifications, the crankshaft can be ground down to 0.25 mm. There is only one oversized rebuild crankshaft and rebuild connecting rod bearings available for service.
10. If the journals have wear outside of specifications, the crankshaft can be ground down to 0.25 mm. There is only one oversized rebuild crankshaft and rebuild connecting rod bearings available for service.
A. Using an outside micrometer, measure the neck at the frontmost point (A) and extreme back point (B) journals parallel to the center line of the crankshaft.
b. Subtract the smaller measurement value from the larger one. The result will be a tapered neck.
c. If the main bearing journal taper exceeds 0.004 mm, replace the crankshaft.
d. If the journals have wear outside of specifications, the crankshaft can be ground down to 0.25 mm. There is only one oversized rebuild crankshaft and rebuild connecting rod bearings available for service.
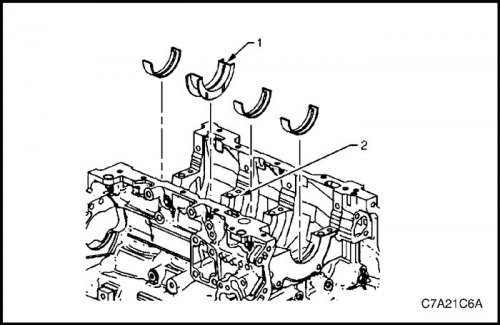
Installation procedure
Main bearing installation procedure
Attention! If the crankshaft bearings have been used with the engine running, replace them with new crankshaft bearings when reassembling.
1. Clean the big end crankcase hole with a lint-free cloth.
2. Clean all oil from the back of the new bearing halves.
3. Install the new upper crankshaft bearings in their original position. Thrust bearing (1) suitable for neck no. 3 (2). Make sure that the upper bearing shell has a hole and a grease redistribution groove. Roll the bearing into its original position so that the locking lug enters the crank groove. The bearing should sit flush with the upper crankcase.
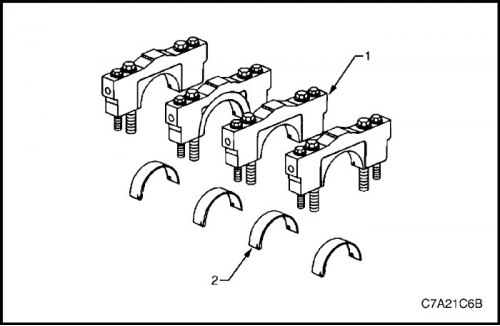
4. Install new crankshaft lower bearings (2) to its original position in the main bearing caps (1). The lower bearings of the crankshaft are different in that they do not have grooves and holes. The bearings must be flush with the main bearing caps.
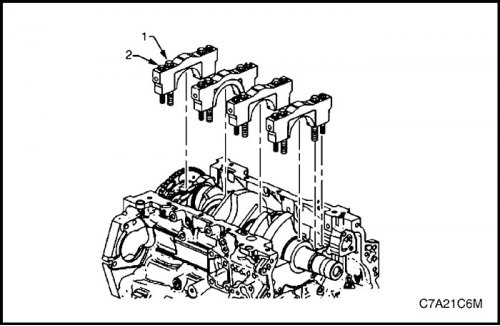
Crankshaft Main Bearing Clearance Measurement
1. Place a piece of fresh, room temperature plastic gauge material all the way across each main bearing journal.
2. Install the crankshaft main bearing caps.
3. Loosely tighten the original internal bolts (1) root caps.
4. Loosely tighten the original outer bolts (2) root caps.
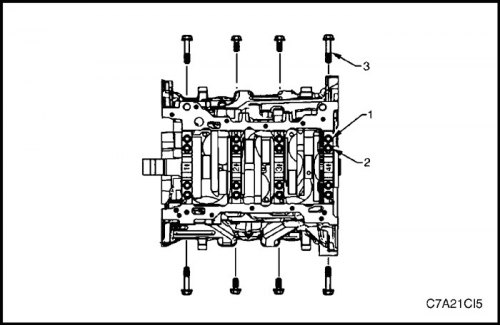
5. Loosely tighten the original short/inner side main cap bolts.
6. Loosely tighten the original long/outer side bolts (3) root caps.
7. Lightly tap with a soft-faced hammer to place the covers in place.
8. Tighten the main cap bolts.
Tighten
Tighten the crankshaft main bearing cap inner bolt to 20 Nm (15 lb-ft), plus another 80°.
Tighten the bolt of the outer fastening of the crankshaft main bearing cap to 15 Nm (11 lb-ft), plus another 110°.
Tighten the crankshaft main bearing cap side bolt to 30 Nm (22 lb-ft), plus another 60°.
Note: Do not rotate the crankshaft.
9. Let the assembly settle for 2 minutes.
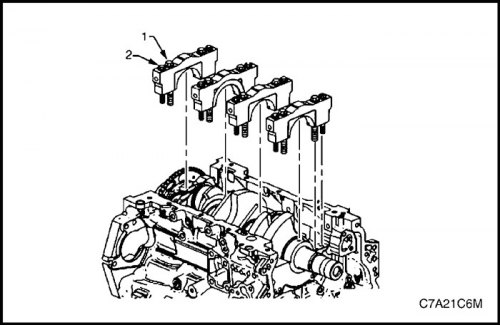
10. Unscrew the side bolts of the main bearing cap.
11. Loosen the outer bolts (2) securing the main bearing cap.
12. Loosen the inner bolts (1) securing the main bearing cap.
13. Install the Crankshaft Main Bearing Cap Remover, Tool No. J-41818 as previously described, and remove the main bearing cap.
14. Repeat steps 10 to 13 for the remaining main bearing caps.
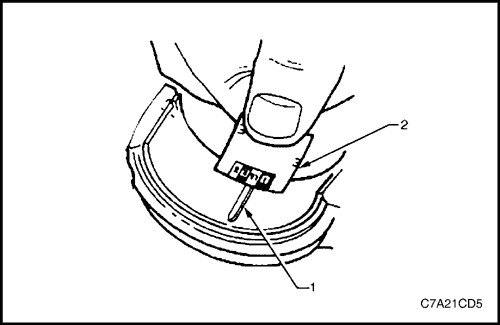
15. Determine the main bearing clearance by comparing the width of the flattened plastic gauge (1) at its widest point with divisions on the measuring scale (2).
16. Compare the measurement data with those given in the technical data. If the new bearings do not provide the correct clearance between the crankshaft and the bearing, check the following:
A. Measure the crankshaft journals to the correct size and make sure new bearings are installed. If the crankshaft journals are out of size, replace or regrind the crankshaft. The crankshaft is allowed to be machined and undersized bearings are available.
b. Measure the diameter of the cylinder block crankshaft bearing recess and make sure it is the correct size. The cylinder block crankshaft bearing recess cannot be machined and if it is out of specification, the block must be replaced.
17. Remove the plastic measuring material from the main bearing journals with a soft, lint-free cloth.
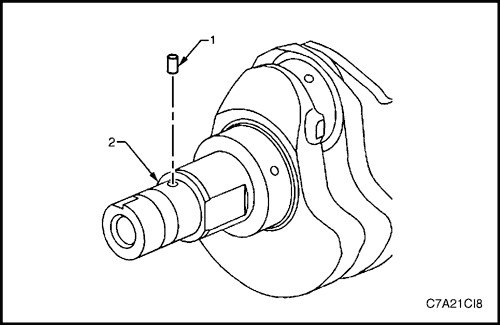
The procedure for the final installation of the crankshaft
1. Set the pin (1) crankshaft sprocket drive, if removed. Using a small soft-faced bronze/plastic mallet, lightly tap the pin into place until it rests on the bottom of the hole.
Attention! Before loading the crankshaft, make sure that the crankshaft position sensor is removed from the cylinder block, as the sensor may be damaged.
2. Liberally coat the upper and lower bearing surfaces with engine oil.
3. Carefully lower the crankshaft (1) to its original position in the cylinder block (2).
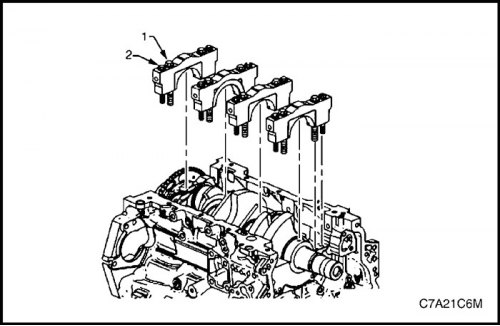
4. Install the crankshaft main bearing caps.
5. Loosely tighten the original internal bolts (1) root caps.
Attention! External bolts (2) main bearing cap fasteners are dynamically tightened during reassembly and must be replaced before reassembly. The outer main bearing cap bolts, which will not be replaced, cannot be tightened to the correct clamping torque, which can cause severe engine damage.
6. Loosely tighten the new outer bolts (2) main bearing caps.
7. Lightly tap with a soft-faced hammer to place the covers in place.
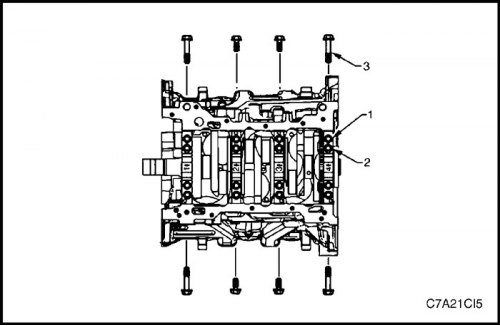
Attention! Initially, the short/inner side bolts of the main bearing caps have sealant on the bolt head flange. New bolts must be used. If new bolts are not used, oil may leak past the bolts from the crankcase.
8. Loosely tighten new short/inner side bolts (4) main bearing caps.
Attention! Initially, the long/outer side bolts of the main bearing caps have sealant on the bolt head flange. New bolts must be used. If new bolts are not used, oil may leak past the bolts from the crankcase.
9. Loosely tighten new long/outer side bolts (3) main bearing caps.
10. Tighten the main cap bolts.
Tighten
Tighten the crankshaft main bearing cap inner bolt to 20 Nm (15 lb-ft), plus another 80°.
Tighten the bolt of the outer fastening of the crankshaft main bearing cap to 15 Nm (11 lb-ft), plus another 110°.
Tighten the crankshaft main bearing cap side bolt to 30 Nm (22 lb-ft), plus another 60°.
11. Make sure the crankshaft rotates without binding or noise.
12. Install the remaining components in the reverse order of removal, see the appropriate section.