Note: Be extremely careful not to cause any scratches, dents or other damage to the crankshaft. Such damage can impair engine performance.
Disassembly
1. Remove the engine.
2. Remove accessories: alternator, power steering pump, A/C compressor.
3. Remove the cylinder head along with the intake and exhaust manifolds.
4. Turn off screws of fastening of a flywheel.
5. Remove the crankshaft pulley.
6. Remove the timing belt tensioner.
7. Remove the timing case elements.
8. Remove the coolant pump.
9. Remove the crankshaft sprocket
10. Remove the flywheel.
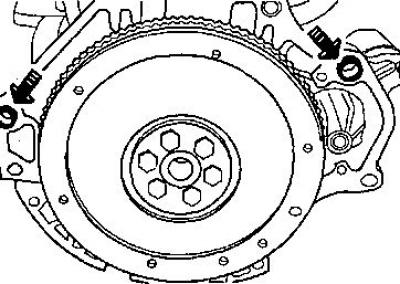
11. Remove the oil pan.
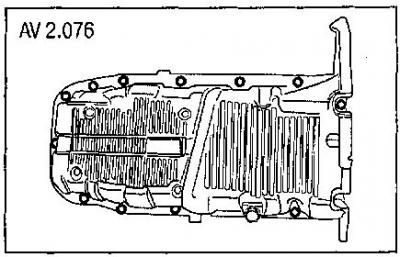
12. Remove the oil receiver.
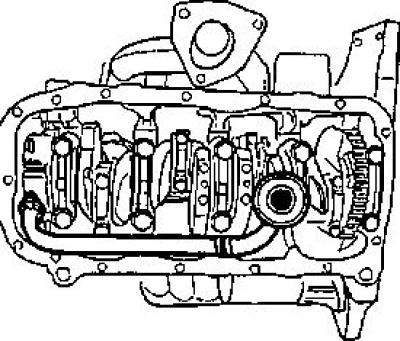
13. Remove the oil pump.
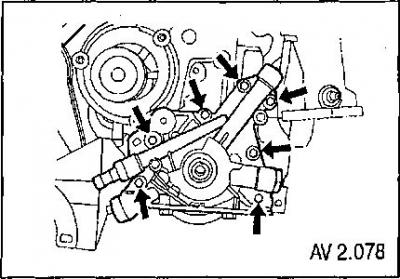
14. Unscrew the screws of the connecting rod bearing caps.
15. Remove the caps of the connecting rod bearings, noting the mutual belonging of the caps and connecting rods.
16. Note the installation order of the crankshaft main bearing caps.
17. Turn off screws of covers of radical bearings of a cranked shaft.
18. Remove the crankshaft main bearing caps.
19. Remove the crankshaft.
20. Remove the main and connecting rod bearing shells from their seats.
21. Remove the pistons with connecting rods, having previously processed the upper part of the cylinder to remove carbon deposits.
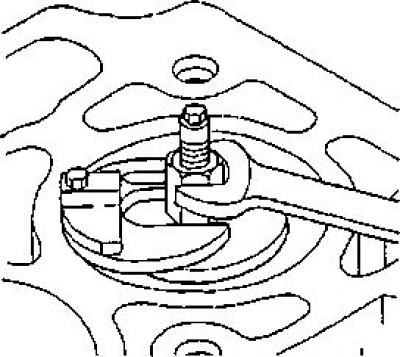
22. Remove piston rings. Use a ring expander.
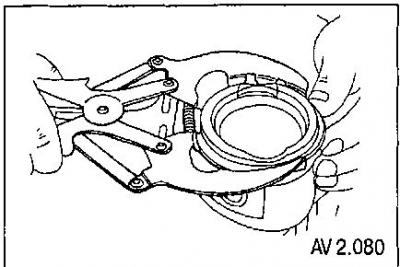
23. Remove the piston pins and separate the piston from the connecting rod.
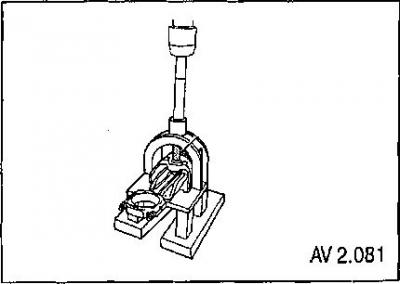
Checking the condition of parts
1. Check the connecting rods for deformation (bending and twisting). If the connecting rods are deformed, replace them.
2. Check the condition of the connecting rod bearings (only to determine the operating conditions of the engine before repair, since in any case new crankshaft bearing shells should be installed).
3. Check the connecting rod bearing seat for wear.
4. Check the connecting rod bore for nicks or wear.
5. Check the crankshaft journals for wear.
Crankshaft |
||
root neck |
Diameter |
54.982-54.994 mm |
Taper (Max.) |
0.005 mm |
|
Deviation from round shape (Max.) |
0.004 mm |
|
Main bearing clearance |
0.005 mm |
|
Runout of the end of the crankshaft |
0.1 mm |
|
Connecting rod journal |
Diameter |
42.971-42.987 mm |
Taper (Max.) |
0.005 mm |
|
Deviation from round shape (Max.) |
0.004 mm |
|
Connecting rod bearing clearance |
0.019-0.070 mm |
|
Connecting rod side clearance |
0.070-0.242 mm |
6. Check pistons for scoring chips and wear.
7. Measure the diameter of the pistons with a micrometer.
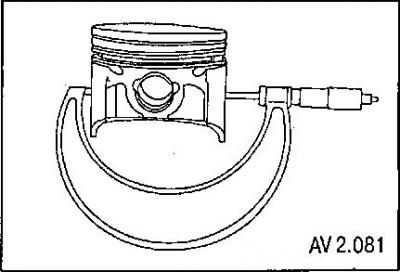
- Piston diameter - 76.470 mm
- The gap between the piston and the cylinder wall is 0.030 mm
8. Check the correct installation of the piston relative to the connecting rod (see labels).

- Piston pin diameter - 18,000 mm
- Finger offset - 0.5-0.7 mm
9. Check the cylinder block for flatness of the surface in contact with the head gasket using a ruler and feeler gauge.
10. Measure the bore diameter of the cylinder at various locations using a bore gauge (at the top, middle and bottom of the cylinder, along two mutually perpendicular diameters).
Engine cylinder bore diameter:
- Diameter - 76.5 mm
- Deviations from the round shape (Max.) - 0.0065 mm
- Taper (Max.) - 0.0065 mm
11. Check the condition of the cylinder walls for protrusions, burnouts of the walls, increased local wear, scoring.
12. Check the condition of the cylinder walls for the presence of varnish and carbon deposits, if necessary, lightly honing to clean.
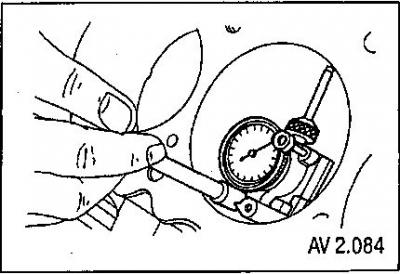
Assembly of the cylinder-piston group
1. Connect the connecting rods to the pistons so that the mark on the piston is directed towards the front of the engine (to timing).
2. Install the piston pin installer guide.
3. Apply a coat of clean engine oil to the pistons.
4. Install the piston pins.
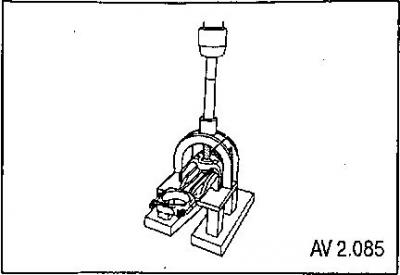
Piston pin:
- Diameter - 18,000 mm
- Finger offset - 0.5-0.7 mm
5. Measure the gap in the locks of the new piston rings by installing them in the cylinder without a piston.
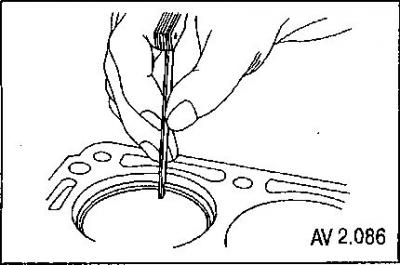
6. Measure the side clearances between the rings and the walls of the piston grooves. Based on the results of measurement, if the wear of the grooves is too great, replace the pistons.
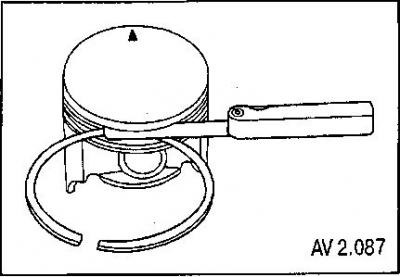
7. Install the piston rings in the sequence shown in the illustration using a ring expander.
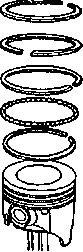
Piston rings: Lower oil scraper, Axial expander, Upper oil scraper, Lower compression, Upper compression.
Piston rings |
||
Compression, joint gap |
Upper |
0.3mm |
2nd compression |
0.3mm |
|
Axial clearance in the piston ring groove |
Upper |
0.02mm |
2nd compression |
0.02mm |
Distribute the piston ring gaps as shown in the figure.
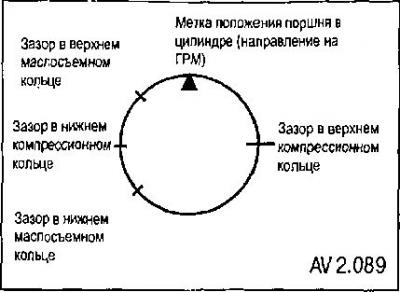
9. Apply a coat of engine oil to the cylinder walls.
10. Install the pistons into the cylinders using a ring crimping tool by lightly tapping with a wooden hammer handle,
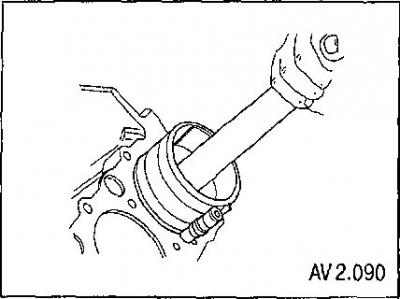
Assembly of the crank mechanism
All parts must be cleaned before assembly.
1. Use a plastic gauge to determine the clearances in all crankshaft bearings. See «Selection of connecting rod bearing shells using a plastic gauge» And «Selection of main bearing shells using a plastic gauge».
2. Check the radial runout of the crankshaft rear seal journal with the bearings installed.
3. Check up an axial run-up of a cranked shaft.
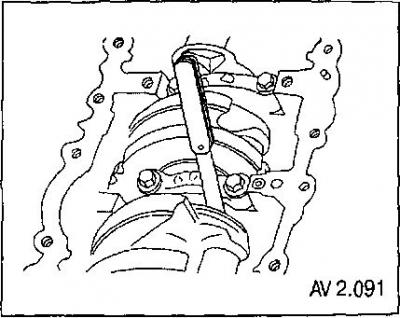
4. Check up runout of a surface of a neck of the average radical bearing of a cranked shaft.
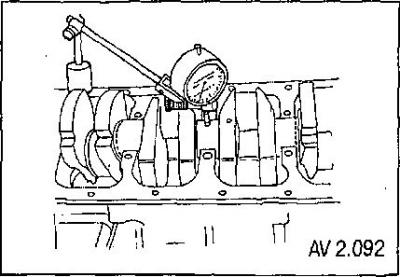
5. Apply a thin coat of engine oil to the crankshaft bearing shells.
6. Install the crankshaft.
7. Apply sealing compound to the rear main bearing cap.
8. Install the main bearing caps No. 1-4 of the crankshaft.
9. Install the #5 main bearing cap. At the same time, make sure that the sealant evenly seals the places of the connector of the cover with the cylinder block.
Note: Do not reuse old crankshaft main bearing screws.
10. Tighten the crankshaft main bearing cap screws:
- tighten the screws to 50 Nm;
- tighten to an angle of 45°+15°.
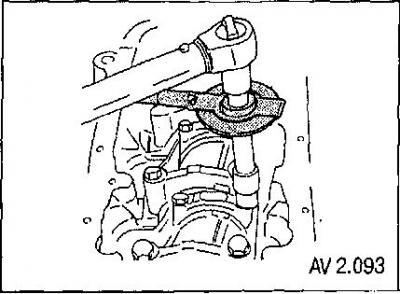
11. Install the connecting rod bearing shells into the connecting rods and into the connecting rod bearing caps.
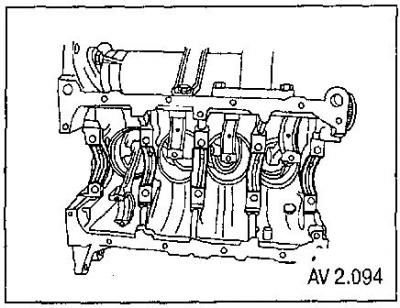
12. Install the connecting rod bearing caps.
Note: Do not reuse old connecting rod bearing cap screws.
13. Tighten the connecting rod bearing cap screws to 25 Nm.
14. Tighten the connecting rod bearing cap screws 30°+15°.
15. Install the oil pump.
16. Tighten the oil pump screws to 10 Nm.
17. Install the oil receiver.
18. Tighten the oil receiver screws to 10 Nm.
19. Install the oil pan gasket.
20. Install the oil pan no later than 5 minutes after applying the gasket sealant.
21. Tighten the oil pan screws to 10 Nm.
22. Install the crankshaft sprocket.
23. Install the rear of the timing case.
24. Tighten the screws on the rear of the timing case to 10 Nm.
25. Install the automatic camshaft timing belt tensioner.
26. Tighten the automatic timing belt tensioner screw to 20 Nm.
27. Tighten the camshaft pulley screw to 45 Nm.
28. Install the timing belt.
29. Adjust the tension of the camshaft timing belt.
30. Install the valve cover with gasket.
31. Tighten the camshaft cover screws to 10 Nm.
32. Install the lower part of the timing case.
33. Tighten the screws on the bottom of the timing case to 10 Nm.
34. Install the power steering pump.
35. Tighten the power steering pump screws to 25 Nm.
36. Install the top of the timing case.
37. Tighten the screws of the upper part of the timing case to 10 Nm.
38. Establish a back epiploon of a cranked shaft by means of a mandrel.
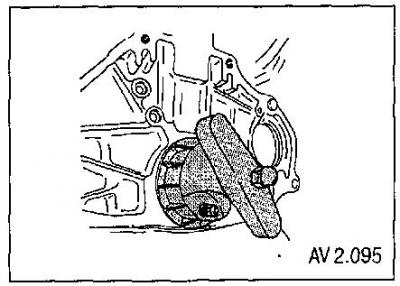
39. Install the flywheel.
40. Tighten the flywheel mounting screws to 35 Nm.
41. Tighten the flywheel mounting screws to an angle of 30°+15°.
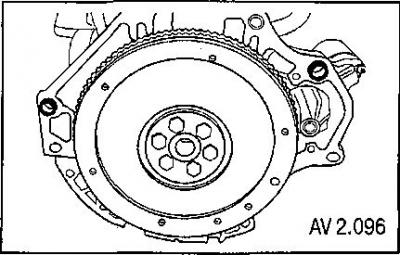
42. Install the engine in the car.
Selection of main bearing shells using a plastic gauge
1. Apply a coat of engine oil to the crankshaft main bearings.
2. Install the upper and lower crankshaft main bearings.
3. Install the crankshaft.
4. Check up radial palpation of a back condensed neck of a cranked shaft at established bearings.
5. Check up an axial run-up of a cranked shaft.
6. Check the runout of the surface of the neck of the middle main bearing of the crankshaft on the crankshaft mounted on the front and rear bearings.
7. Check up all backlashes in bearings of a cranked shaft.
8. Cut plastic measuring strips to a length equal to the width of the bearings. Position them along the axis between the crankshaft journals and the main bearing shells.
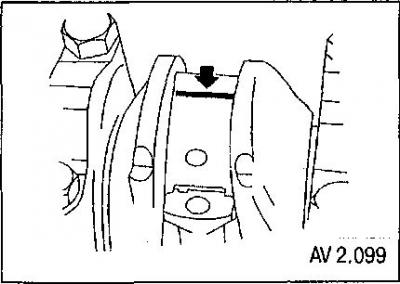
9. Install the crankshaft bearing caps.
10. Tighten the crankshaft main bearing cap screws to 50 Nm.
11. Tighten the screws of the crankshaft main bearing caps at an angle of 45' + 15".
12. Remove the crankshaft main bearing caps.
13. Measure the width of the flattened part of the plastic strip with a ruler.
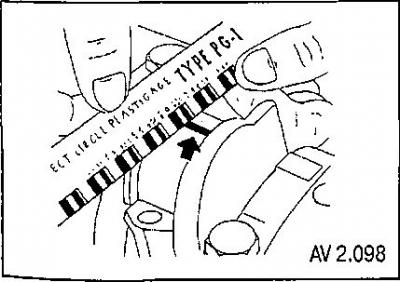
Selection of connecting rod bearing shells using a plastic gauge
1. Apply a coat of engine oil to the connecting rod bearing shells.
2. Install the upper and lower connecting rod bearings.
3. Establish the lower loose leaves of rod bearings.
4. Check clearances in connecting rod bearings.
5. Cut plastic measuring strips to a length equal to the width of the bearings. Position them along the axis between the connecting rod bearing journals with the connecting rod bearing shells.
6. Install the connecting rod bearing caps.
7. Tighten the connecting rod bearing cap screws to 25 Nm.
8. Tighten the screws of the crankshaft cover to an angle of 30°+15°.
9. Remove the connecting rod bearing caps.
10. Measure the width of the flattened plastic layer with a ruler.
11. Compare your results with the allowable bearing clearances.